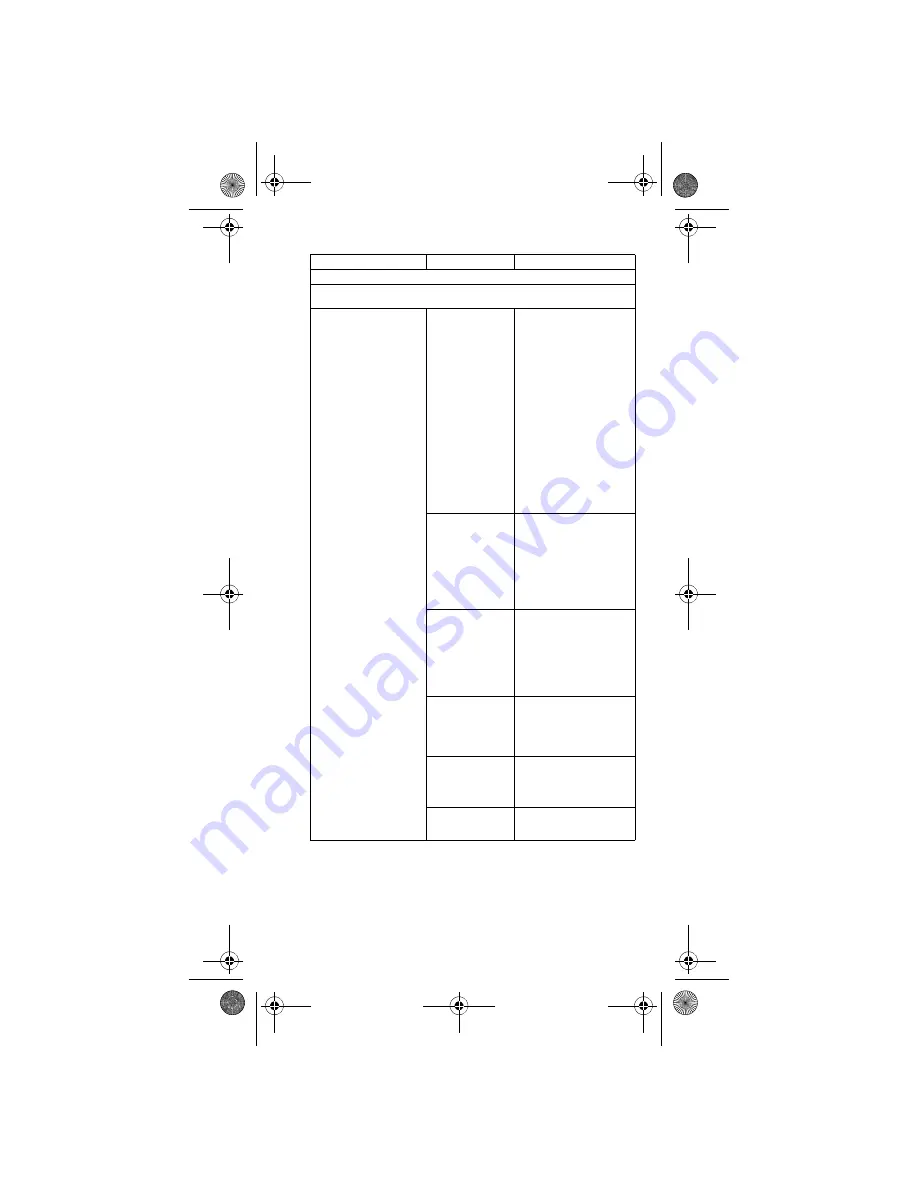
123
Section 2: Beermaster Glycol Chiller System
When troubleshooting a closed remote system, one should consider the
following areas:
Temperature
Beer draws warm
and is all foam.
Check coolant circulation
by:
•
Inspecting the coolant
circulation pump to
ensure it is on and
running.
•
Inspecting the coolant
return line in reservoir
to ensure it is
circulating. Replace
pump if necessary.
Check coolant temperature
by:
•
Adjusting the range
from 27°F (-2.7°C) to
29°F (-1.6°C).
•
Fill reservoir to proper
level with 3:1 glycol
mix.
No beer flows
through system.
Check tap check ball and
free if stuck. Check
Coolant temperature. If it is
less than 27°F (-2.7°C), the
beer in the lines may be
frozen. Turn OFF coolant
compressor, then adjust
coolant temperature to be
between 27°F (-2.7°C) and
29°F (-1.6°C).
First beer out
always seems
foamy or streaky.
Ensure that coolant line is
in direct contact with the
beer line right up to the
back of the shank. If not,
place aluminum foil
between beer line and
coolant line, then insulate.
This will transfer the cold to
the beer line.
Beer in cooler is
above 40°F
(4.4°C).
Temperature of cooler
ideally should be less than
38°F (3.3°C). Contact an
authorized refrigeration
service agency to set
cooler.
Glycol is dirty or
too weak.
Clean reservoir and add
new glycol solution (add
new glycol to weak
solution). Should give Brix
on sugar refractor.
Glycol solution is
too warm.
Check outlet and inspect
agitator for proper
operation.
Problem
Possible Cause
To Correct
STH13_Tech.book Page 123 Wednesday, September 15, 2010 3:20 PM