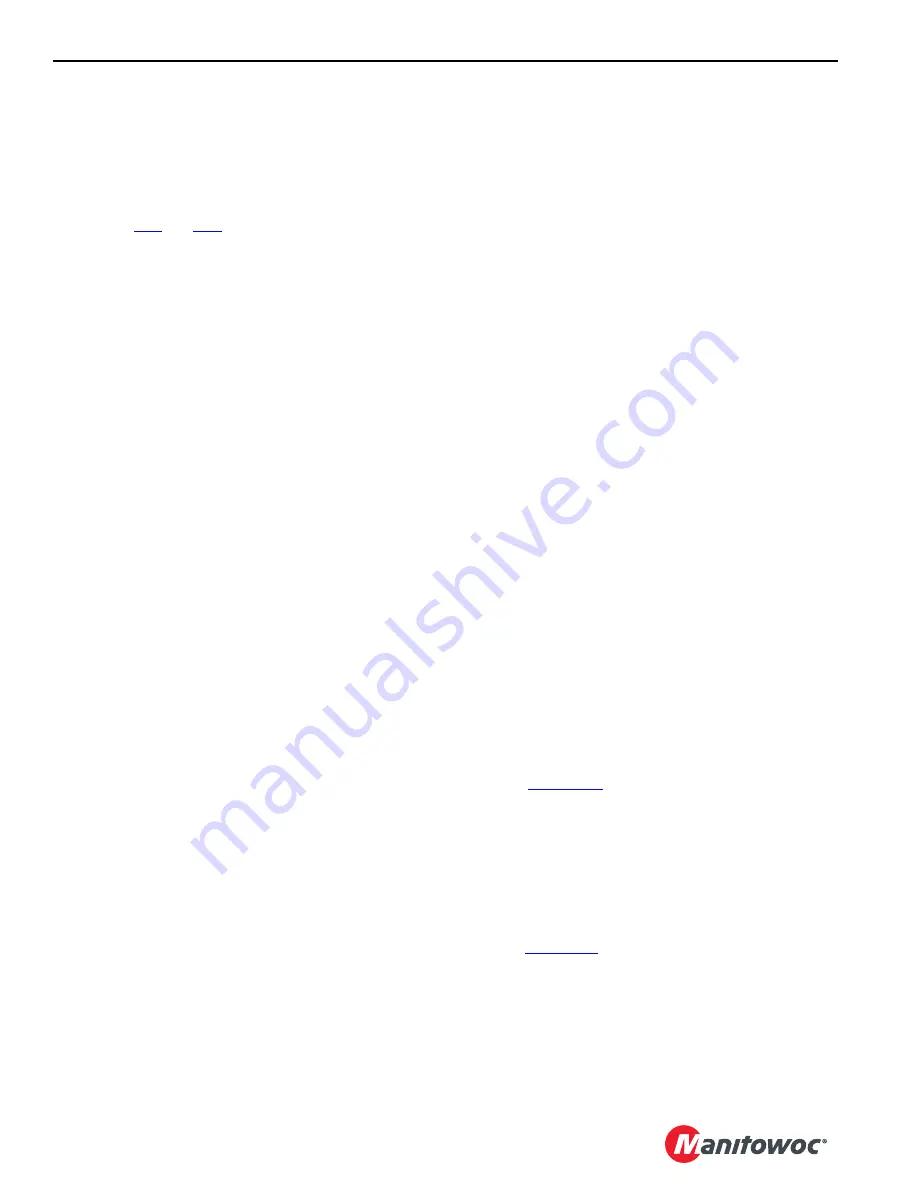
Only
INTRODUCTION
18000 SERIVCE/MAINTENANCE MANUAL
1-30
Published 12-05-17, Control # 035-23
SWING SYSTEM OPERATION
NOTE:
All reference to swing lock is past production.
Current production cranes do not have a swing lock
installed.
Swing System Components
See Figures
One hydraulic swing pump drives two swing motors (optional
swing drive has two swing pumps and four swing motors).
There are equalizing lines between legs A and legs B when
two pumps drive two motors. Both swing systems are
controlled with swing control handle movement and node
controllers. Swing control handle is inoperable when swing
brake is applied or the swing lock is engaged. Each motor
driven swing gearbox drives a tooth gear that is meshed with
lowerworks turntable bearing to swing the upperworks.
Swing motors are controlled directly by the output fluid
volume of the swing pump. Node controllers do not control
the fixed displacement swing motors. Swing pressure
senders monitor the pressure on swing left and swing right
sides of swing closed loop system. Swing brake pressure is
monitored by a pressure sender through Node-7 on current
production cranes without swing lock. While in MAX-ER
mode, travel will be disabled if the swing brake is applied.
The upperworks is free to coast if swing control handle is in
neutral position, swing brake is released, and swing lock is
disengaged.
Swing speed and swing torque can be selected for type of
work being performed by referring to “Speeds” screen in
Crane Diagnostics in Section 10 of the Service/Maintenance
Manual.
Continuous changing of closed-loop fluid occurs through
leakage in pumps and motors.
When swing control handle is moved from off, node-5
controller sends a 24 volt signal to enable swing/travel alarm.
When swing control handle is moved to off, node-5 controller
sends a 0 volt signal to disable swing/travel alarm.
Swing Brake and Swing Lock
NOTE:
To verify if the crane does not have a swing lock
installed, scroll to the swing brake diagnostic
screen on the crane display. The swing brake
pressure bank will be present only on cranes
without a swing lock.
The swing system has a spring-applied hydraulically
released brake on each drive shaft and a mechanical brake
(swing lock) that places locking pins into slots in shaft locking
flange of each gearbox.
The source hydraulic pressure for releasing the swing
brakes and swing locks is from high pressure accessory
pump system through a pressure reducing shuttle valve at
500 psi (34 bar). For swing brake and swing lock operation
the system pressure must be above 200-psi (14 bar) for full
release brake and lock. If system pressure is below 200-psi
(14 bar), swing brake or swing lock could be partially applied
and damage the swing system. If brake pressure or electrical
power is lost when operating, the swing brake is applied.
After startup, place swing brake switch in off - park position.
An input voltage is sent to node-1 controller. Node-7
controller sends a 24 volt output to enable swing brake
solenoid valve HS-32 and swing lock out solenoid valve HS-
33.
Swing brake solenoid valve shifts to hydraulically release
swing brake from each shaft. Swing lock out solenoid valve
shifts to block tank port and supplies hydraulic system
pressure to rod end of cylinders to hydraulically release
mechanical locking pins from each shaft-locking flange. Fluid
from piston end of cylinders flows to tank.
Before shutdown, place swing brake switch in on - park
position. An input voltage is sent to node-1 controller. Node-7
controller sends a zero output voltage to disable swing brake
solenoid valve HS-32 and enable swing lock in solenoid
valve HS-34.
Swing brake solenoid valve shifts to block fluid to brake and
swing brake is applied. Fluid from brake flows to tank. Swing
lock in solenoid valve HS-34 shifts to block tank port and
supplies hydraulic system pressure to piston end of cylinders
to hydraulically engage mechanical locking pins into shaft
locking flange. Fluid from rod end of cylinders flows to tank.
Swing Right or Left
When swing control handle is moved to the
left
,
an input
voltage of 2.4 volts or less is sent to node-1 controller. Node-
3 and node-5 controllers send a variable zero to 24 volt
output that is divided by a resistor and applied to swing
pump(s) EDC. Pump EDC tilts swashplate relative to control
handle movement. Fluid flows from pump ports to motor
ports (see
), rotating upperworks to the left. An
orifice, across swing motor ports A and B allow smoother
fluid flow when shifting swing directions.
When swing control handle is moved to
right
,
an input
voltage of 2.6 volts or more is sent to node-1 controller.
Node-3 and node-5 controllers send a variable zero to 24
volt output that is divided by a resistor and applied to swing
pump(s) EDC. Pump EDC tilts swashplate relative to control
handle movement. Fluid flows from pump ports to motor
ports (see
), rotating upperworks to the right.
As swing control handle is moved to neutral position, node-1
controller compensates for hydraulic system leakage or
changing engine speed. Node-3 and node-5 controllers send
a zero output voltage to adjust swashplate to centered
position.
Summary of Contents for 18000
Page 1: ...R e f e r e n c e O n l y Service Maintenance Manual Manitowoc 18000 ...
Page 2: ...R e f e r e n c e O n l y ...
Page 4: ...R e f e r e n c e O n l y THE ORIGINAL LANGUAGE OF THIS PUBLICATION IS ENGLISH ...
Page 210: ...R e f e r e n c e O n l y NOTES SKETCHES AND PHOTOGRAPHS ...
Page 315: ...R e f e r e n c e O n l y ...
Page 316: ...R e f e r e n c e O n l y ...