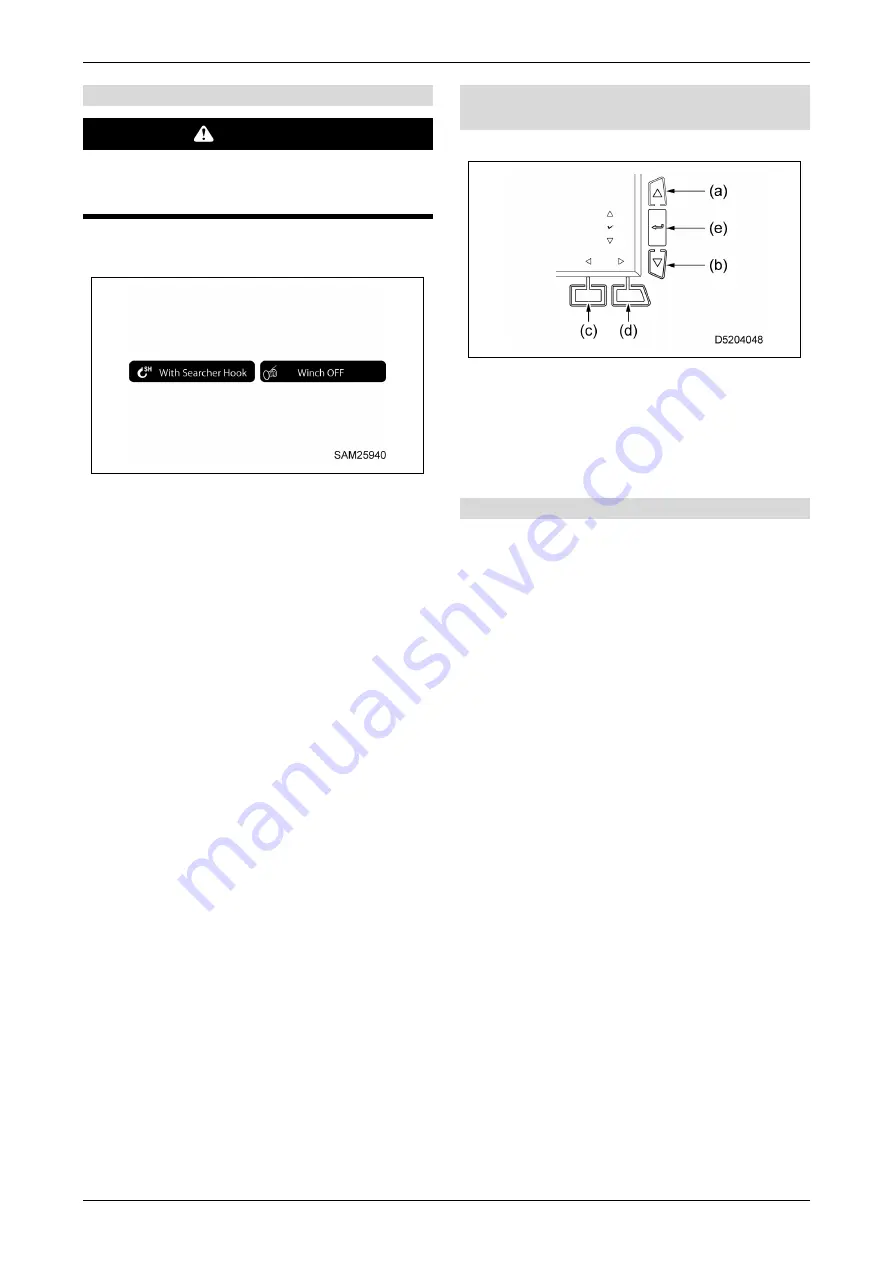
M A E D A
Crawler Crane
4.2 MONITOR
5/2020 CC1908S-1
4-13
[13] Searcher Hook Setting
WARNING
With or without searcher hook setting must be
matched to the actual condition. The wrong
settings can cause a serious accident.
By touching these buttons With/Without Searcher
Hook and Winch ON/OFF can be switched.
[ With/Without Searcher Hook ]
Touch to switch between With or Without
Searcher Hook.
• With Searcher Hook:
Select this when searcher hook is mounted.
This switches to searcher hook mode.
• Without Searcher Hook:
Select this when searcher hook is not
mounted.
Switch this when mounting or removing the
searcher hook. When the setting is changed,
the moment limiter display will change and
the rated total load will change.
[ Winch ON/OFF ]
Touch to switch the Winch ON or OFF.
• OFF
:Winch does not work even when winch is
operated.
• ON
:
The winch works as usual.
This is not available when the main hook is
used or without the searcher hook attached.
[14] Pop-up selector switches
(User Settings screen)
Press to operate the pop-up functions.
(a) Up
(b) Down
(c) Left
(d) Right
(e) Select/enter
[15] Home switch
Press to return to the previous screen.
Press and hold to return to the home screen.
Summary of Contents for CC1908S-1
Page 2: ......
Page 10: ...CONTENTS M A E D A Crawler Crane viii 5 2020 CC1908S 1 This Page Intentionally Left Blank...
Page 11: ...INTRODUCTION...
Page 19: ...Chapter 2 SAFETY...
Page 45: ...SPECIFICATIONS...
Page 48: ...3 2 DIMENSIONAL DRAWINGS M A E D A Crawler Crane 3 4 5 2020 CC1908S 1 DIMENSIONAL DRAWINGS...
Page 49: ...M A E D A Crawler Crane 3 2 DIMENSIONAL DRAWINGS 5 2020 CC1908S 1 3 5...
Page 50: ...3 2 DIMENSIONAL DRAWINGS M A E D A Crawler Crane 3 6 5 2020 CC1908S 1...
Page 51: ...M A E D A Crawler Crane 3 2 DIMENSIONAL DRAWINGS 5 2020 CC1908S 1 3 7...
Page 63: ...M A E D A Crawler Crane 3 4 WORKING RADIUS LIFTING HEIGHT DIAGRAMS 5 2020 CC1908S 1 3 19...
Page 64: ...3 4 WORKING RADIUS LIFTING HEIGHT DIAGRAMS M A E D A Crawler Crane 3 20 5 2020 CC1908S 1...
Page 65: ...M A E D A Crawler Crane 3 4 WORKING RADIUS LIFTING HEIGHT DIAGRAMS 5 2020 CC1908S 1 3 21...
Page 67: ...PARTS AND CONTROLS...
Page 117: ...OPERATION...
Page 209: ...MAINTENANCE AND INSPECTION...
Page 259: ...M A E D A Crawler Crane 6 17 PERIODIC MAINTENANCE 5 2020 CC1908S 1 6 51 1 2 3 7 6 5 4...
Page 326: ......