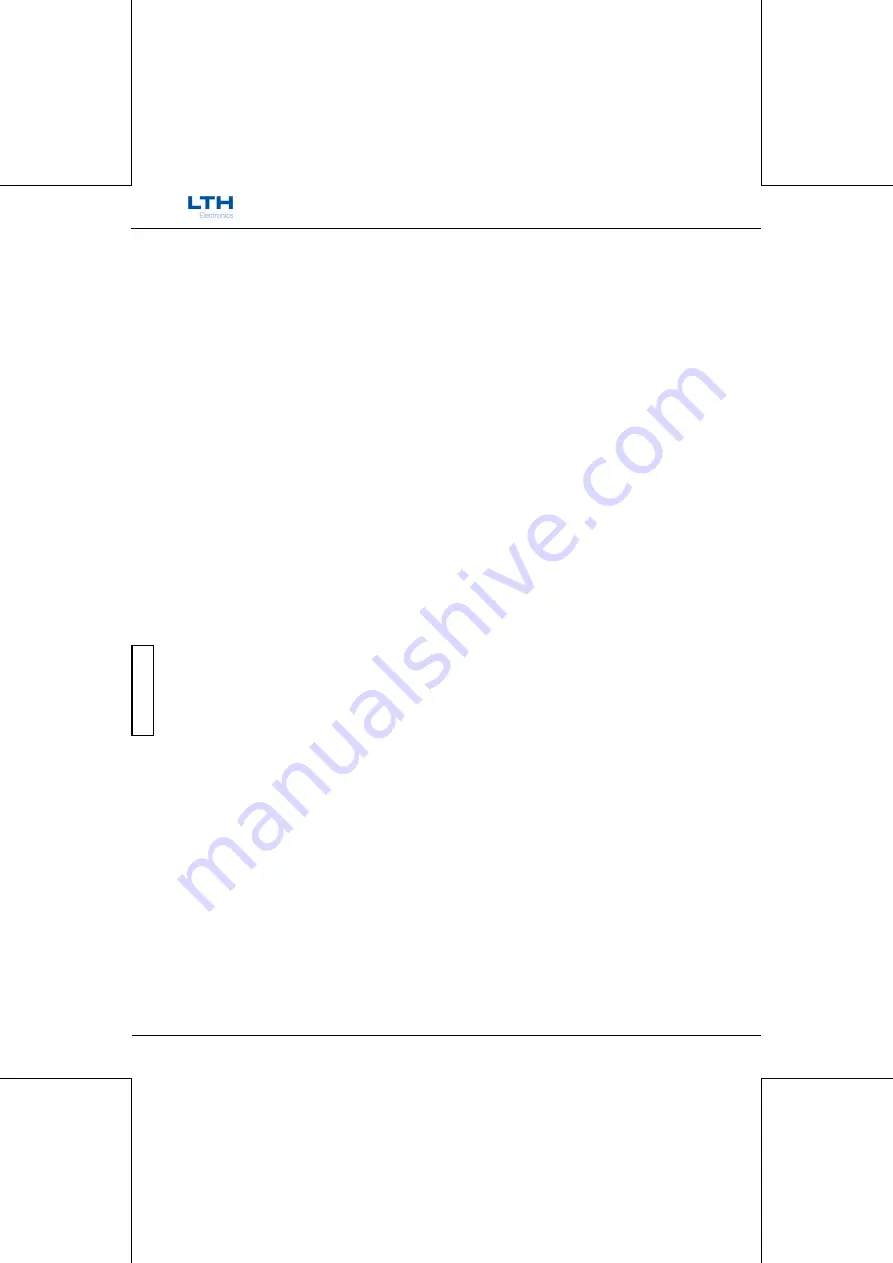
Appendix H
- 254 -
MTD75 Operation Guide
Appe
ndix H
The Redox Sensor Is Not Functioning Correctly
Check that the sensor not broken or cracked.
Check the reference probe KCl (where applicable) for leakage or contamination.
Ensure all probe protective caps have been removed.
Check that any junction boxes used are correctly connected.
Check that a suitable high impedance, low noise cable has been used.
Check for damaged or broken cables.
Check for damp, grease, or liquids near connectors, junction boxes, or terminations.
Where extension cables have been used, try connecting the sensor directly to the instrument.
The Electrodeless Conductivity Sensor Reading Is Constantly Over-range or Under-range
Ensure that the sensor and temperature inputs are correctly connected (See page 42) and that the
sensor is not faulty or damaged.
Check that the correct sensor type or cell constant has been entered within the Channel Setup
menu (See page 101).
Check the temperature compensation state (See page 101) If the compensation is set to “Manual”
check that the fixed temperature is at the correct level. If the compensation is “Automatic” check
that the temperature reading on the main display is correct.
Check that the sensor is “seeing” a representative sample, trapped air will give a low reading.
Ensure the input is correctly connected and the sensor is not faulty or damaged.
Check the sensor and its cable for possible short circuits. Consider the fact that the conductivity may
be higher than the range of the instrument.
Check the Pt1000 RTD temperature sensor connections.
Check that any in-line junction boxes and extension cables have been fitted and wired up correctly.
The Electrodeless Conductivity Sensor Reading Is Incorrect
Low reading due to incomplete immersion.
There may be some trapped matter within the sensor bore.
High conductivity readings caused by a short circuit or leakage of liquid contamination into the
sensor moulding.
Low conductivity can be caused by accumulation of trapped air or gas coming out of solution.
Check that no "air traps" exist in the sensor installation.
High conductivity readings caused by leakage of solution into the sensor. This usually indicates that
the sensor material has been fractured and the sensor must be replaced.
First check that the temperature resistance is correct, otherwise the temperature compensation
circuit will cause false or erratic readings. Temporarily switching out the temperature compensation
can help to show if this is the cause of the problem.
If another electrodeless sensor is available, this can be used to determine whether the fault lies with
the instrument or the sensor.
Check that the sensor cable is not damaged or broken and that the outer screen does not make
contact with any other terminals or metal work.
Check that the sensor cable is sufficiently distant from power cables or electrical noise sources.
Check that the correct sensor type has been installed.
Check that the correct range has been selected.
Check that the correct sensor loop resistor calibration value (500Ω) has been used.
Check that the calibration procedure has been followed precisely.
Check that the temperature compensation has been set up as required.
Check that the sensor cable does not exceed the maximum specified length (sensor 5m + extension
95m).
Summary of Contents for MTD75
Page 1: ...MTD75 Cooling Tower Controller Operation Guide ...
Page 2: ......
Page 5: ...Preface MTD75 Operation Guide 3 Declaration of Conformity ...
Page 6: ...Preface 4 MTD75 Operation Guide ...
Page 12: ...Introduction 10 MTD75 Operation Guide Introduction MXD75 Termination Overview ...
Page 29: ...Installation MTD75 Operation Guide 27 Installation Horizontal Mounting Vertical Mounting ...
Page 30: ...Installation 28 MTD75 Operation Guide Installation Blank ...
Page 72: ...Biocide A 70 MTD75 Operation Guide Biocide A BLANK ...
Page 74: ...Biocide B 72 MTD75 Operation Guide Biocide B BLANK ...
Page 88: ...Inhibitor 86 MTD75 Operation Guide Inhibitor BLANK ...
Page 98: ...pH Control 96 MTD75 Operation Guide pH Control BLANK ...
Page 100: ...Alarm Relay 98 MTD75 Operation Guide Alarm Relay BLANK ...
Page 108: ...Electrodeless Conductivity Setup 106 MTD75 Operation Guide ECS Setup BLANK ...
Page 112: ...pH Input Setup 110 MTD75 Operation Guide pH Setup BLANK ...
Page 118: ...Redox Calibration 116 MTD75 Operation Guide Redox Calibration BLANK ...
Page 140: ...pH Calibration 138 MTD75 Operation Guide pH Calibration BLANK ...
Page 142: ...Calibration Reset 140 MTD75 Operation Guide Calibration Reset BLANK ...
Page 148: ...Current Outputs 146 MTD75 Operation Guide Current Outputs BLANK ...
Page 152: ...Digital Inputs 150 MTD75 Operation Guide Digital Inputs BLANK ...
Page 158: ...Configuration 156 MTD75 Operation Guide Configuration BLANK ...
Page 160: ...Update Software 158 MTD75 Operation Guide Update Software BLANK ...
Page 164: ...Save Restore Reset 162 MTD75 Operation Guide Save Restore Reset BLANK ...
Page 166: ...Error Messages 164 MTD75 Operation Guide Error Messages BLANK ...
Page 172: ...Modbus RS485 170 MTD75 Operation Guide Modbus RS485 BLANK ...
Page 184: ...Data Logging 182 MTD75 Operation Guide Data Logging BLANK ...
Page 246: ...Appendix F 244 MTD75 Operation Guide Appendix F Blank ...
Page 254: ...Appendix G 252 MTD75 Operation Guide Appendix G BLANK ...
Page 260: ...Notes 258 MTD75 Operation Guide ...
Page 261: ...Notes MTD75 Operation Guide 259 ...
Page 265: ......