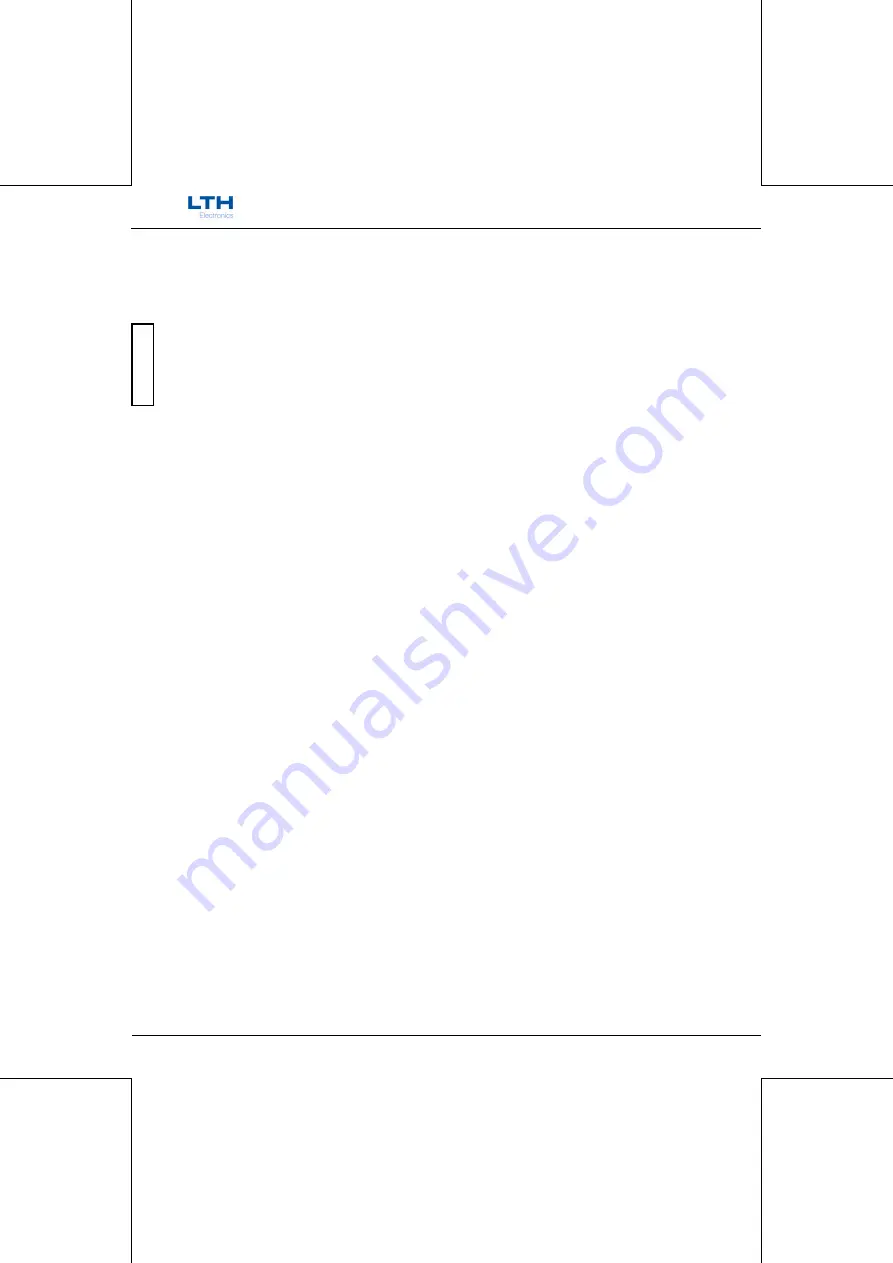
Installation
- 18 -
MTD75 Operation Guide
Ins
tallation
Noise suppression
In common with other electronic circuitry, the controller may be affected by high level,
short duration noise spikes arising from electromagnetic interference (EMI) or radio
frequency interference (RFI). To minimise the possibility of such problems occurring, the
following recommendations should be followed when installing the controller in an
environment where such interference could potentially occur.
The following noise generating sources can affect the controller through capacitive or
inductive coupling.
Relay coils
Solenoids
AC power wires, particularly at or above 100V AC
Current carrying cables
Thyristor field exciters
Radio frequency transmissions
Contactors
Motor starters
Business and industrial machines
Power tools
High intensity discharge lights
Silicon control rectifiers that are phase angle fired
The controller is designed with a high degree of noise rejection built in to minimise the
potential for interference from these sources, but it is recommended that you apply the
following wiring practices as an added precaution. Cables transmitting low level signals
should not be routed near contactors, motors, generators, radio transmitters, or wires
carrying large currents.
If noise sources are so severe that the controller’s operation is impaired, or even halted, the
following external modifications should be made, as appropriate:
Fit arc suppressors across active relay or contactor contacts in the vicinity.
Run signal cables inside steel tubing as much as is practical.
Use the internal relays to switch external slave relays or contactors when switching
heavy or reactive loads.
Fit an in-line mains filter close to the power terminals of the controller.
In cases of very high background RF and HF noise environments, LTH can supply a
length of proprietary RF suppressing mains cable.
Summary of Contents for MTD75
Page 1: ...MTD75 Cooling Tower Controller Operation Guide ...
Page 2: ......
Page 5: ...Preface MTD75 Operation Guide 3 Declaration of Conformity ...
Page 6: ...Preface 4 MTD75 Operation Guide ...
Page 12: ...Introduction 10 MTD75 Operation Guide Introduction MXD75 Termination Overview ...
Page 29: ...Installation MTD75 Operation Guide 27 Installation Horizontal Mounting Vertical Mounting ...
Page 30: ...Installation 28 MTD75 Operation Guide Installation Blank ...
Page 72: ...Biocide A 70 MTD75 Operation Guide Biocide A BLANK ...
Page 74: ...Biocide B 72 MTD75 Operation Guide Biocide B BLANK ...
Page 88: ...Inhibitor 86 MTD75 Operation Guide Inhibitor BLANK ...
Page 98: ...pH Control 96 MTD75 Operation Guide pH Control BLANK ...
Page 100: ...Alarm Relay 98 MTD75 Operation Guide Alarm Relay BLANK ...
Page 108: ...Electrodeless Conductivity Setup 106 MTD75 Operation Guide ECS Setup BLANK ...
Page 112: ...pH Input Setup 110 MTD75 Operation Guide pH Setup BLANK ...
Page 118: ...Redox Calibration 116 MTD75 Operation Guide Redox Calibration BLANK ...
Page 140: ...pH Calibration 138 MTD75 Operation Guide pH Calibration BLANK ...
Page 142: ...Calibration Reset 140 MTD75 Operation Guide Calibration Reset BLANK ...
Page 148: ...Current Outputs 146 MTD75 Operation Guide Current Outputs BLANK ...
Page 152: ...Digital Inputs 150 MTD75 Operation Guide Digital Inputs BLANK ...
Page 158: ...Configuration 156 MTD75 Operation Guide Configuration BLANK ...
Page 160: ...Update Software 158 MTD75 Operation Guide Update Software BLANK ...
Page 164: ...Save Restore Reset 162 MTD75 Operation Guide Save Restore Reset BLANK ...
Page 166: ...Error Messages 164 MTD75 Operation Guide Error Messages BLANK ...
Page 172: ...Modbus RS485 170 MTD75 Operation Guide Modbus RS485 BLANK ...
Page 184: ...Data Logging 182 MTD75 Operation Guide Data Logging BLANK ...
Page 246: ...Appendix F 244 MTD75 Operation Guide Appendix F Blank ...
Page 254: ...Appendix G 252 MTD75 Operation Guide Appendix G BLANK ...
Page 260: ...Notes 258 MTD75 Operation Guide ...
Page 261: ...Notes MTD75 Operation Guide 259 ...
Page 265: ......