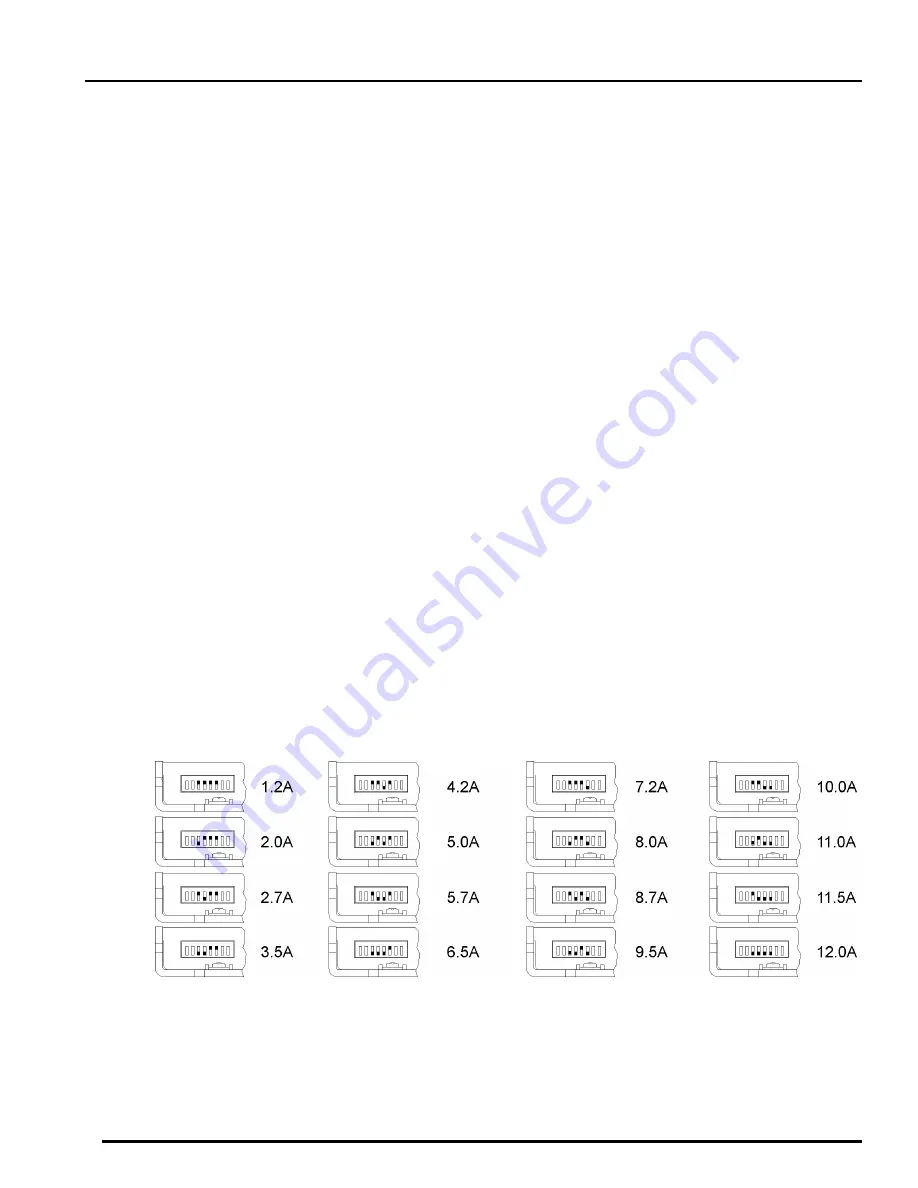
Logosol Absolute Positioning Servo Drive LS-173AP
Doc # 712173008 / Rev. 1.06, 05/09/2002
Logosol, Inc.
••
1155 Tasman Drive
••
Sunnyvale, CA 94089 Tel: (408) 744-0974
••
www.logosolinc.com 19
(ClockWise) by hand and check if the motor position is increasing. If motor position is not
changing or it is decreasing, check encoder connection. Set the Drive in PWM mode. Start the
motor with PWM for example 5 (this value might be enough or not depending on motor used)
Set PWM to –5. If the phasing is correct the motor shaft should rotate CW (CCW) smoothly
without any jerks. Otherwise try different motor leads connection. There are only six
combinations and it is recommended to try all of them. Usually only one works fine. If you find
more than one, try to run the motor at higher speed. Set the Drive in velocity mode and start
the motor in CW direction. If the motor runs away, directions of motor and encoder are
opposite. To change the motor direction exchange S1 with S3 and AC1 with AC2. To change
the encoder direction exchange A and B phase wires.
Safety Features
To protect both the user device and the controller, LS-173AP is equipped with various safety
features.
STP IN – Stop Input
For normal operation STP IN signal must be “low”. If it is “high” it will disable the Power Driver
and set status byte bit 3 (Power_on) to zero.
Undervoltage/Overvoltage Protection
LS-173AP is protected against power supply under/overvoltage. In case the power supply is
below 12V hardware reset is generated. More then 91V will disable the Power Driver and set
status byte bit 3 (Power_on) to zero.
Overcurrent Protection
A protection circuit monitors the output current of the motor and limit to a value set by
dipswitch. If the motor is overloaded for less than 200 ms, the output current is limited to the
selected level. Power Driver will be disabled if the motor is overloaded for more then 200 ms.
Use the table to set CL (current limit):
Overcurrent DIP Switch Settings