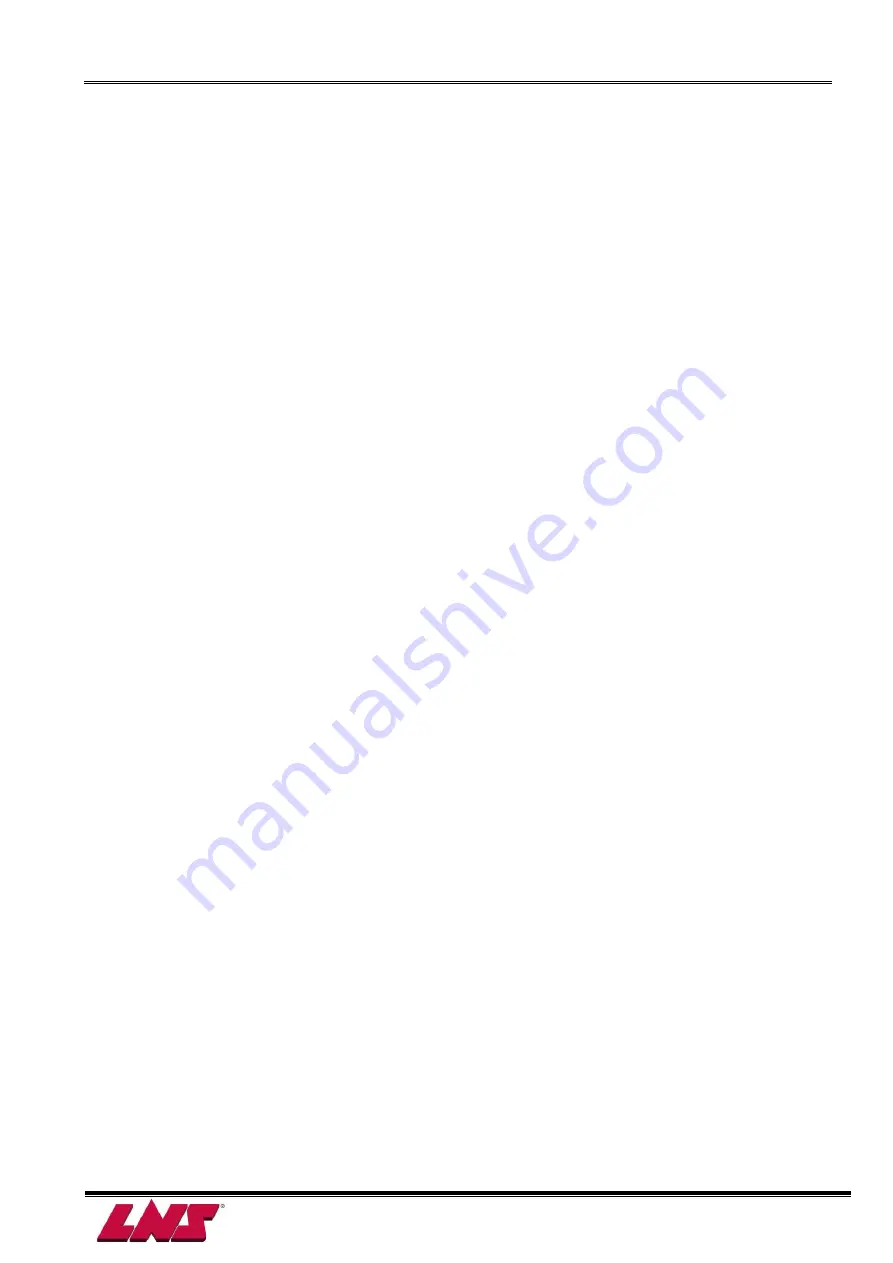
Chapter 1 BASIC NOTIONS
1 - 3
GT 112-E
1.3 SAFETY INSTRUCTIONS
Do not handle the equipment without having knowledge of the safety instructions and the
instructions for use. Safety instructions for the bar feeder, as well as the CNC lathe, must
be strictly observed. We disclaim all responsibility for possible accidents or property
damage caused by not following our safety instructions.
Non-qualified personnel, children, and people under the influence of alcohol or medication
should not handle the equipment.
Loose garments, long hair and jewelry can be dangerous.
Do not remove any covers while the bar feeder or the machine is under electrical power.
Do not conduct any maintenance operations during the automatic cycle.
Do not grasp moving or rotating objects, or nearby elements.
If certain safety shields or safety covers are removed to conduct maintenance, they must
be reinstalled as soon as the maintenance work is completed.
No servicing should be carried out on the interface or inside the electrical cabinet while the
bar feeder or the lathe is under electrical power.
It is strictly prohibited to jump wire or remove circuit breakers, main switches, and
especially safety switches.
To avoid any harm to people, or damage to components, use only the indicated points for
lifting and moving the bar feeder system. No one should be near the handing load, or within
the operating range of the overhead hoist/crane, forklift, or any other means used for lifting
and transportation. Do not knock the bar feeder while moving it as this could damage it.
Do not move the bar feeder while it is electrically powered on.
Please use the bar feeder in a clean environment.
Please do not use the bar feeder with extreme heat or in a high humidity environment.
The working area surrounded the bar feeders should always be clear of objects and well lit.
The presence of oil on the ground could cause falls; it is important to maintain the floor
cleaning on a regular basis.
Do not place the machine in a damp area and make sure that water or oil does not come
into contact with the electrical equipment.
Do not open the clamping device (collet or chuck) of the lathe manually when the bar
feeder is in AUTOMATIC mode (interface).
Each time the diameter is changed, also adapt spindle reduction tube. The use of spindle
reduction tubes is highly recommended for machining bars with diameters smaller than the
maximum capacity of the spindle.
There is no battery inside the PLC. Do not attempt to recharge it.
For the use and maintenance of the bar feeder, use only parts provided by or
recommended by LNS.
If it is necessary to move the bar feeder after it has been originally installed, do not reinstall
it before first contacting our representative.
The rotating bar stock should never protrude the rear of the lathe spindle.
We disclaim all responsibility for possible accidents or property damage when safety device
is removed.
Summary of Contents for GT 112-E
Page 7: ...1 4 Chapter 1 BASIC NOTIONS GT 112 E...
Page 10: ...Chapter 2 TECHNICAL DATA 2 3 GT 112 E 2 4 FLOOR PLAN LtoRF Bar Feeder...
Page 11: ...2 4 Chapter 2 TECHNICAL DATA GT 112 E RtoLF Bar Feeder...
Page 13: ...2 6 Chapter 2 TECHNICAL DATA GT 112 E...
Page 21: ...3 8 Chapter 3 SETTING INTO OPERATION GT 112 E...
Page 32: ...Chapter 4 ELECTRICS 4 11 GT 112 E 4 4 PLC I O Circuit diagram XM1 25 A001G...
Page 33: ...4 12 Chapter 4 ELECTRICS GT 112 E 4 5 DIAGRAMS 4 5 1 AC circuit Circuit diagram XM1 25 A001G...
Page 34: ...Chapter 4 ELECTRICS 4 13 GT 112 E 4 5 2 Emergency stop circuit Circuit diagram XM1 25 A001G...
Page 35: ...4 14 Chapter 4 ELECTRICS GT 112 E Circuit diagram XM1 25 A001G...
Page 36: ...Chapter 4 ELECTRICS 4 15 GT 112 E Circuit diagram XM1 25 A001G Option...
Page 38: ...Chapter 4 ELECTRICS 4 17 GT 112 E Interface diagram BXA00001...
Page 48: ...Chapter 5 PNEUMATICS 5 7 GT 112 E 5 5 PNEUMATIC DIAGRAMS Pneumatic diagrams XM1 27 P003A...
Page 49: ...5 8 Chapter 5 PNEUMATICS GT 112 E Pneumatic diagrams XM1 27 P003A...
Page 50: ...Chapter 5 PNEUMATICS 5 9 GT 112 E Pneumatic diagrams XM1 27 P003A...
Page 51: ...5 10 Chapter 5 PNEUMATICS GT 112 E...
Page 75: ...7 20 Chapter 7 GENERAL DESCRIPTION GT 112 E...
Page 110: ...Chapter 8 OPERATION 8 35 GT 112 E 1 Start loading signal A3 2 Push signal A4...
Page 111: ...8 36 Chapter 8 OPERATION GT 112 E...
Page 114: ...Chapter 8 OPERATION 8 39 GT 112 E...
Page 150: ...9 36 Chapter 9 TROUBLE SHOOTING GUIDE GT 112 E...
Page 153: ...Chapter 10 APPENDICES 10 3 GT 112 E APPENDIX C ADDRESS LNS LNS Japan www lns japan com...
Page 154: ...10 4 Chapter 10 APPENDICES GT 112 E...
Page 155: ...XM1 00 A501B GT 112 E A 1...