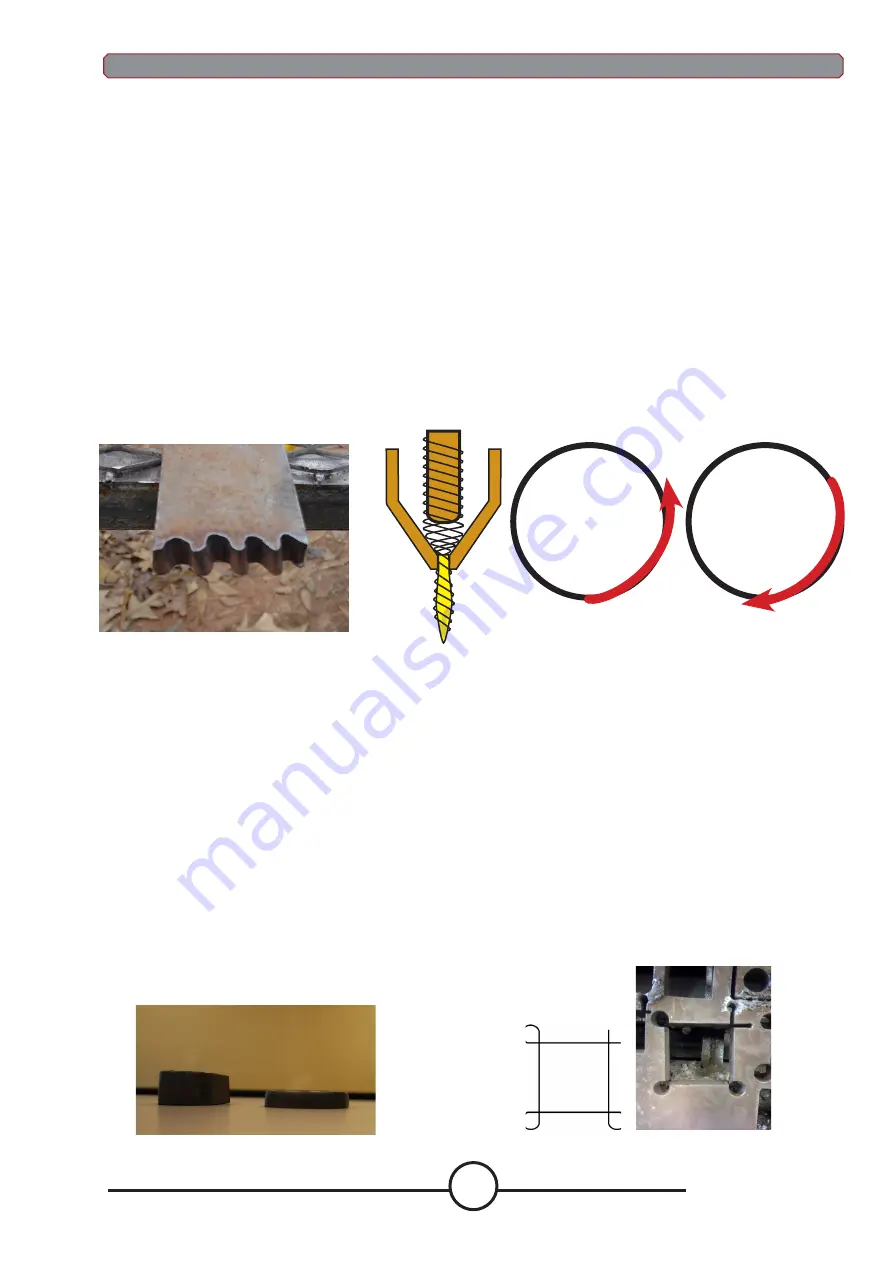
45
User’s guide
Bevel base
•
Bevelled edges are caused by the motion of the plasma gas as it is emitted from the nozzle. The
phenomenon is unavoidable with plasma cutting. A high-definition plasma cutter produces less bevel
than a standard cutter.
•
Torch height, air pressure, air quality, cut direction, and consumable condition all influence bevel.
•
In plasma arcs used for cutting, the gas forms into a vortex. As a result, the arc has a direction of
rotation, which causes one side of the cut to have more bevel than the other side. To reduce the bevel
on the part, the appropriate direction of travel must be used.
•
The direction of cuts are referred to as “conventional” and “climb”. In a conventional cut, the torch
turns anticlockwise on outside cuts and clockwise on inside cuts. A climb cut is the opposite, and is the
cut that delivers the best bevel.
•
Basically, the best bevel is to the right of the direction of travel.
Conventional
Climb
•
Corners may show more bevel than normal cuts. That happens when the machine slows down for
the direction change. In some cases, a lower amperage allows slower travel speeds and reduces the
slowdown bevel at corners.
•
Sharp corners can be achieved by cutting a larger shape that puts the slow down and acceleration
of the machine into a scrap area. This cut is used more often on thicker materials, where the corner
bevel increases significantly.
•
Replace consumables regularly to reduce bevel. A worn tip or one with dross buildup can redirect
air flow causing random bevel and varying cut quality. Always check the consumables when
troubleshooting bevel.
•
One of the easiest ways to reduce bevel is by cutting at the proper speed and height for the material
and amperage.
•
Air that is at constant pressure and clean and dry also decreases bevel.
Bevelled edge
Corner loops