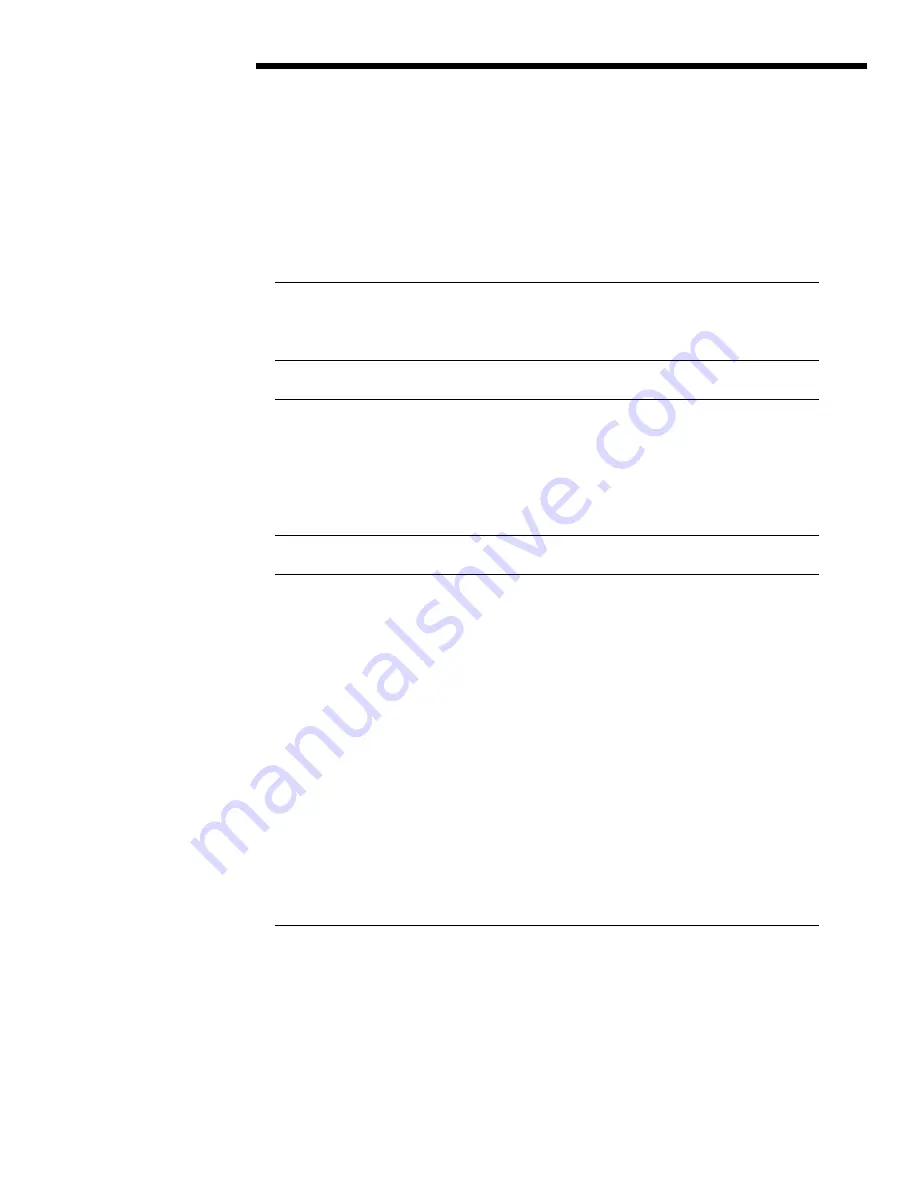
LMAIM1501
LY Installation and Maintenance for LY 1001, LY 2001 and LY 3001
iii
Table of Contents
1 Introduction
1-1
1.1 Purpose
1-1
1.2 User Safety
1-1
2 Product Capabilities and Features
2-1
3 Initial Inspection and Storage Instructions
3-1
3.1 Product Identification
3-1
3.2 Inspection and Recording
3-1
3.3 Storage Procedures
3-2
3.3.1 Short-Term Storage (less than 1 year)
3-2
3.3.2 Long-Term Storage (1 to 5 years)
3-2
4 Unit Weights
4-1
5 Installation Instructions
5-1
5.1 Safety Precautions
5-1
5.2 Initial Actuator Preparation
5-1
5.3 Installation Overview
5-2
5.4 Torque Switch Settings
5-6
5.5 Rewiring the Torque Switch for Non-Standard Drive Sleeve Rotation
5-6
5.6 Limit Switch and Mechanical Stop Settings
5-7
5.7 Setting the Limit Switches
5-7
5.7.1 Setting the CLOSED Limit Switch
5-7
5.7.2 Setting the OPEN Limit Switch
5-9
5.8 Mechanical Stops
5-10
5.8.1 Setting the CLOSED Mechanical Stop on the LY 1001
5-10
5.8.2 Setting the CLOSED Mechanical Stop on the LY 2001/3001
5-10
5.8.3 Setting the OPEN Mechanical Stop on the LY 1001
5-11
5.8.4 Setting the OPEN Mechanical Stop on the LY 2001/3001
5-11
5.9 Setting the MDPI (Mechanical Dial Position Indicator)
5-12
5.9.1 Setting the Potentiometer
5-13
6 Operation
6-1
6.1 Typical LY 1001 Operation
6-1
6.2 Verify Correct Motor Rotation (Phasing) and OPEN/CLOSE Pushbutton Operation6-1
6.2.1 Three-Phase Motor
6-1
6.2.2 Single-Phase Motor
6-5
6.2.3 DC Motor
6-8
6.3 Electrical Startup
6-8
6.4 Manual Operation
6-8
6.5 Motor Operation
6-9
Flow Control Division
Limitorque Actuation Systems