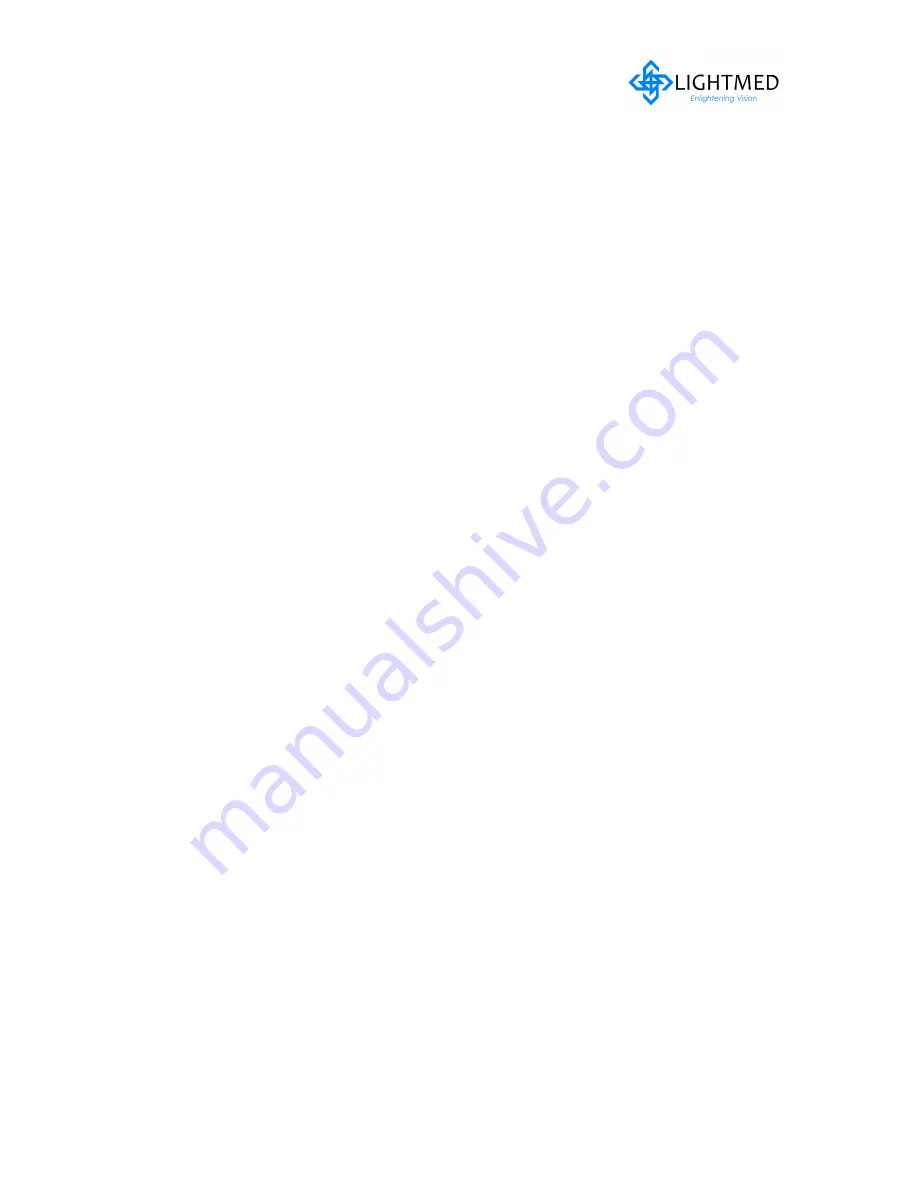
Multi-Wavelength Pattern Scanning System - LightLas 532 / 670 - Service Manual
Page 24
Rev. No 01
4.4
Preparation
Multi-Wavelength Pattern Scanning System - LightLas 532 / 670 is an integrated laser
photocoagulation system where is also equipped with enhance, faster, and more
precise laser scanning patterns and micro pulse features.
The system will deliver predetermined patterns and controlling laser emission light
through a single footswitch depression. The aiming beam will display the
predetermined pattern which allows clinician or physician to aim for the appropriate
treatment location.
All the packaging items should be checked accordingly and unpacked carefully from
their cartons and carry case. Always inspect for any transportation damage and
general condition and report any discrepancy or disclaim to freight courier if there is
damage.
System components
Multi-Wavelength Pattern Scanning System - LightLas 532 / 670 consists of the
following functional units:
Multi-Wavelength Pattern Scanning System - LightLas 532 / 670 system table top
and motorized stand
LDU system (Slit lamp / LIO / Endoprobes)
LCD touch screen panel integrated with computer windows platform system
Footswitch
Accessories
Summary of Contents for TruScan 532
Page 1: ...Service Manual Multi Wavelength Pattern Scanning System LightLas 532 670 ...
Page 4: ...Multi Wavelength Pattern Scanning System LightLas 532 670 Service Manual Page 4 Rev No 01 ...
Page 112: ...Multi Wavelength Pattern Scanning System LightLas 532 670 Service Manual Page 112 Rev No 01 ...
Page 113: ...Multi Wavelength Pattern Scanning System LightLas 532 670 Service Manual Page 113 Rev No 01 ...
Page 114: ...Multi Wavelength Pattern Scanning System LightLas 532 670 Service Manual Page 114 Rev No 01 ...
Page 115: ...Multi Wavelength Pattern Scanning System LightLas 532 670 Service Manual Page 115 Rev No 01 ...
Page 116: ...Multi Wavelength Pattern Scanning System LightLas 532 670 Service Manual Page 116 Rev No 01 ...
Page 117: ...Multi Wavelength Pattern Scanning System LightLas 532 670 Service Manual Page 117 Rev No 01 ...
Page 127: ...Multi Wavelength Pattern Scanning System LightLas 532 670 Service Manual Page 127 Rev No 01 ...
Page 128: ...Multi Wavelength Pattern Scanning System LightLas 532 670 Service Manual Page 128 Rev No 01 ...
Page 129: ...Multi Wavelength Pattern Scanning System LightLas 532 670 Service Manual Page 129 Rev No 01 ...
Page 131: ...Multi Wavelength Pattern Scanning System LightLas 532 670 Service Manual Page 131 Rev No 01 ...
Page 140: ...Multi Wavelength Pattern Scanning System LightLas 532 670 Service Manual Page 140 Rev No 01 ...