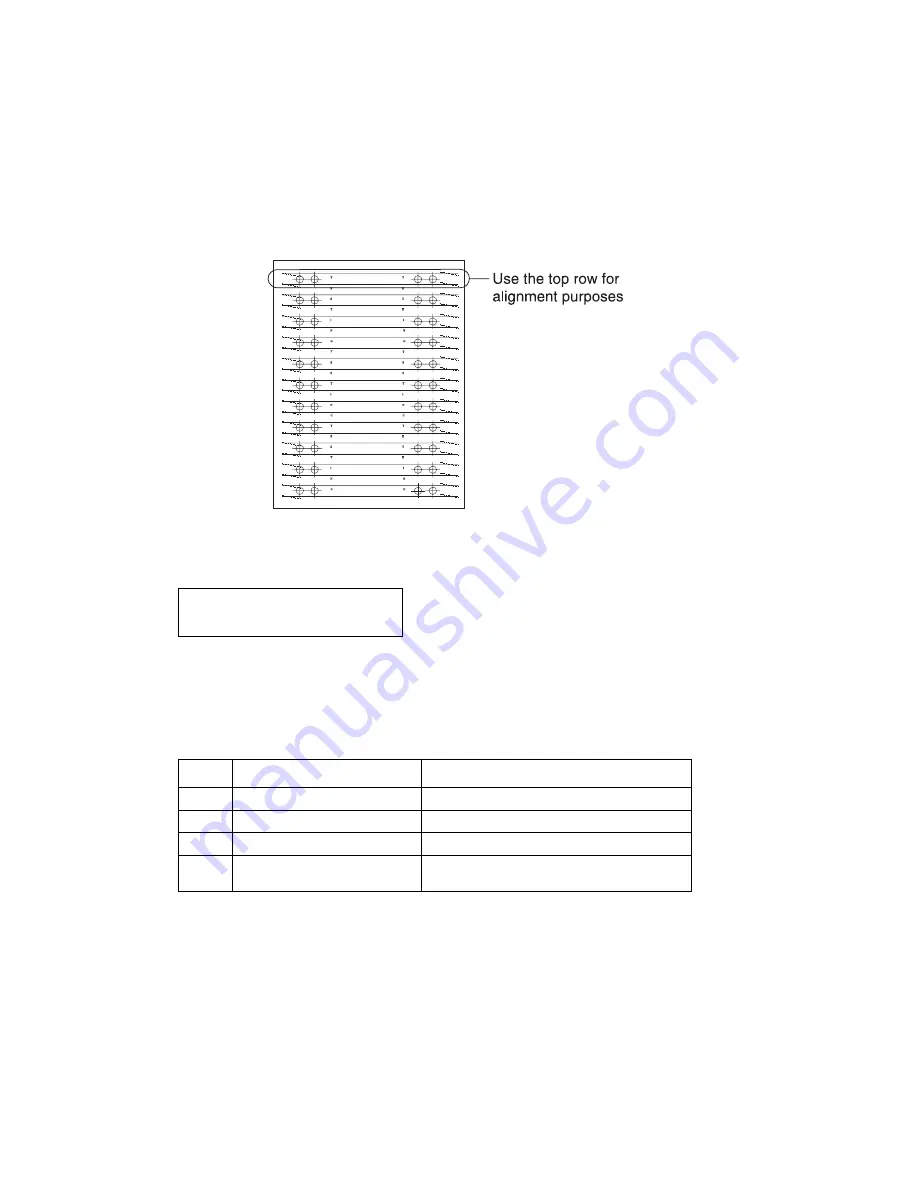
4-58
Service Manual
5060-00
x
Electronic color alignment
Note:
Use of a loupe or magnifying glass (4x or higher) may make observation of the alignment targets easier.
1.
Press
Menu
until
Alignment
displays and press
Select
.
2.
Select
Alignment Test
from the Alignment menu.
Three sheets print for cyan, magenta, and yellow. Each is compared to black alignment.
For example, one of the sheets shows cyan printed over a black target. Align the cyan over the black.
Repeat for each of the colors cyan, magenta, and yellow.
Examples of the alignment pages are available in Appendix B. See
“Printhead alignment test pages—
magenta (one of three)” on appendix page B-9
.
3.
To align cyan, press
Menu
until
Cyan
is displayed, press
Select
. Four alignment settings are displayed.
•
Menu
changes the values.
•
Select
saves the new value chosen and moves to the next margin setting.
•
Press
Go
to print the individual color Alignment Page after adjusting the targets and saving the
change (
Select
).
•
The range of values differs for the various margin offsets.
T= Top
L= Left
R= Right
Z= Theta
Value
Description
Range
T
Top Margin Offset
-128 to +127
L
Left Margin Offset
-300 to +300
R
Right Margin Offset
-300 to +300
Z
Theta Offset (Skew
compensation)
-16 to +16
Summary of Contents for 5060-00x
Page 14: ...xiv Service Manual 5060 00x...
Page 15: ...Laser notice xv 5060 00x...
Page 16: ...xvi Service Manual 5060 00x...
Page 34: ...1 14 Service Manual 5060 00x...
Page 115: ...Diagnostic information 2 81 5060 00x Printer configuration diagrams for 24x paper jams...
Page 237: ...Repair information 4 19 5060 00x 9 Remove the MPF swing arm assembly E E...
Page 312: ...4 94 Service Manual 5060 00x...
Page 313: ...Connector locations 5 1 5060 00x 5 Connector locations Locations Printer boards...
Page 315: ...Connector locations 5 3 5060 00x Printer sensors...
Page 316: ...5 4 Service Manual 5060 00x Cartridge contact assembly pin locations...
Page 317: ...Connector locations 5 5 5060 00x Engine board cabling...
Page 318: ...5 6 Service Manual 5060 00x RIP board cabling...
Page 344: ...5 32 Service Manual 5060 00x HCOF system board...
Page 350: ...7 2 Service Manual 5060 00x Assembly 1 Covers...
Page 352: ...7 4 Service Manual 5060 00x Assembly 1 1 Covers...
Page 354: ...7 6 Service Manual 5060 00x Assembly 2 Cartridge mounting...
Page 356: ...7 8 Service Manual 5060 00x Assembly 3 Fuser...
Page 358: ...7 10 Service Manual 5060 00x Assembly 3 1 Fuser web oiler 1 2 3...
Page 368: ...7 20 Service Manual 5060 00x Assembly 12 Multipurpose feeder MPF...
Page 370: ...7 22 Service Manual 5060 00x Assembly 13 500 sheet integrated tray...
Page 374: ...7 26 Service Manual 5060 00x Assembly 16 ITU drive assembly 2 4 1 5 3 5...
Page 376: ...7 28 Service Manual 5060 00x Assembly 17 ITU loading...
Page 380: ...7 32 Service Manual 5060 00x Assembly 20 Cartridge drive assembly...
Page 382: ...7 34 Service Manual 5060 00x Assembly 21 Electronics...
Page 384: ...7 36 Service Manual 5060 00x Assembly 21 1 Electronics...
Page 388: ...7 40 Service Manual 5060 00x Assembly 21 4 Electronics...
Page 390: ...7 42 Service Manual 5060 00x Assembly 22 Electronic cabling engine board...
Page 392: ...7 44 Service Manual 5060 00x Assembly 23 Electronic cabling RIP board...
Page 396: ...7 48 Service Manual 5060 00x Assembly 26 Output expander...
Page 398: ...7 50 Service Manual 5060 00x Assembly 26 1 Output expander...
Page 400: ...7 52 Service Manual 5060 00x Assembly 27 5 bin mailbox...
Page 402: ...7 54 Service Manual 5060 00x Assembly 27 1 5 bin mailbox...
Page 404: ...7 56 Service Manual 5060 00x Assembly 28 500 sheet drawer option...
Page 406: ...7 58 Service Manual 5060 00x Assembly 28 1 500 sheet tray option...
Page 408: ...7 60 Service Manual 5060 00x Assembly 29 Duplex option...
Page 410: ...7 62 Service Manual 5060 00x Assembly 29 1 Duplex option...
Page 412: ...7 64 Service Manual 5060 00x Assembly 30 High capacity input tray HCIT...
Page 414: ...7 66 Service Manual 5060 00x Assembly 30 1 High capacity input tray HCIT...
Page 416: ...7 68 Service Manual 5060 00x Assembly 31 High capacity output finisher HCOF...
Page 418: ...7 70 Service Manual 5060 00x Assembly 31 1 High capacity output finisher...
Page 420: ...7 72 Service Manual 5060 00x Assembly 31 2 High capacity output finisher...
Page 422: ...Service Manual 5060 0xx Assembly 32 High capacity output finisher cables...
Page 426: ...7 78 Service Manual 5060 00x...
Page 456: ...A 30 Service Manual 5060 00x...
Page 458: ...B 2 Service Manual 5060 00x Print Menus Page two of two...
Page 460: ...B 4 Service Manual 5060 00x Print Quality Pages Page 1 total of five...
Page 461: ...Appendix B Print quality samples B 5 5060 00x Print Quality Pages Page 2 total of five...
Page 462: ...B 6 Service Manual 5060 00x Print Quality Pages Page 3 total of five...
Page 463: ...Appendix B Print quality samples B 7 5060 00x Print Quality Pages Page 4 total of five...
Page 464: ...B 8 Service Manual 5060 00x Registration Quick Test...
Page 466: ...B 10 Service Manual 5060 00x Printhead alignment test page yellow two of three...
Page 468: ...B 12 Service Manual 5060 00x Print Line Len page...
Page 487: ......
Page 488: ......
Page 489: ......
Page 490: ......