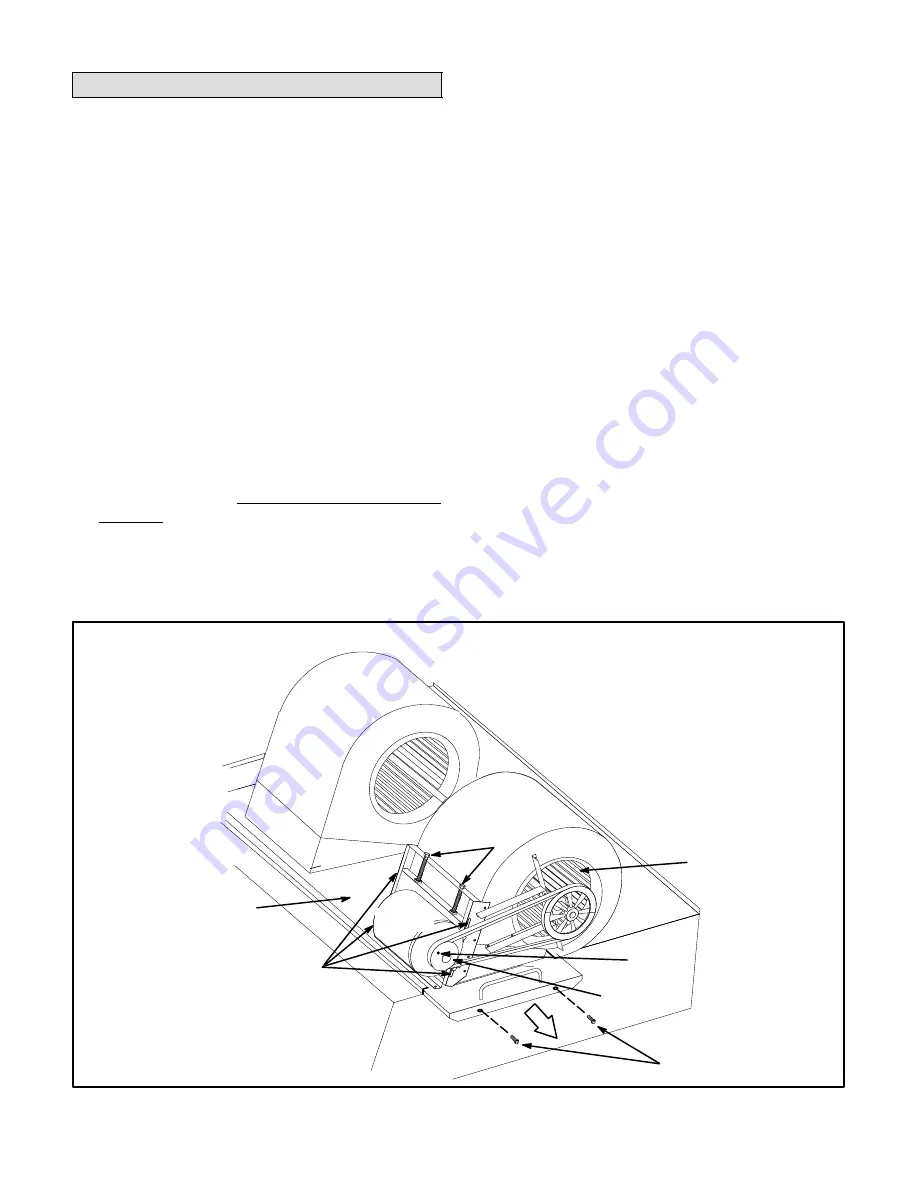
Page 8
506393−01 11/2010
Blower Operation And Adjustments
A−Three Phase Scroll Compressor Voltage Phasing
Three phase scroll compressors must be phased
sequentially to ensure correct compressor and blower
rotation and operation. Compressor and blower are wired
in phase at the factory. Power wires are color−coded as
follows: line 1−red, line 2−yellow, line 3−blue.
1− Observe suction and discharge pressures and
blower rotation on unit start−up.
2− Suction pressure must drop, discharge pressure
must rise, and blower rotation must match rotation
marking.
If pressure differential is not observed or blower rotation is
not correct:
3− Disconnect all remote electrical power supplies.
4− Reverse any two field−installed wires connected to
the line side of TB2. Do not reverse wires at blower
contactor.
5− Make sure the connections are tight.
Discharge and suction pressures should operate at
their normal start-up ranges.
B−Blower Operation
Initiate blower demand at thermostat according to
instructions provided with thermostat. Unit will cycle on
thermostat demand. The following steps apply to
applications using a typical electro−mechanical
thermostat.
1− Set thermostat or temperature control device fan
switch to
AUTO
or
ON.
With fan switch in
ON
position,
blower will operate continuously. With fan switch in
AUTO
position, the blower will cycle with demand.
2− Blower and entire unit will be off when thermostat or
temperature control device system switch is in
OFF
position.
C−Blower Access
The blower assembly is secured to a sliding base which
allows the entire assembly to be pulled out of the unit. See
figure 5.
1− Remove the clamp which secures the blower wiring
to the blower motor base.
2− Remove and retain screws on either side of sliding
base. Pull base toward outside of unit. When pulling
the base out further than 12" (305mm), disconnect
wiring to K3 blower contactor T1, T2, and T3. Pull
wiring toward blower to allow enough slack to slide
the base out further.
BLOWER ASSEMBLY
TO INCREASE BELT TENSION
1− Loosen four screws securing blower motor to
sliding base.
2− Turn adjusting screw to the left, or counter-
clockwise, to move the motor downward and
tighten the belt.
3− Tighten four screws.
TO INCREASE CFM
LOOSEN ALLEN SCREW &
TURN PULLEY CLOCKWISE
TO DECREASE CFM
TURN PULLEY
COUNTERCLOCKWISE
FIGURE 5
BLOWER
WHEEL
BLOWER
MOTOR
PULLEY
ALLEN
SCREW
BLOWER ASSEMBLY
SLIDING BASE
BELT TENSION
ADJUSTING
SCREWS
LOOSEN (4) SCREWS TO
ADJUST BELT TENSION
REMOVE SCREWS TO
SLIDE BLOWER
ASSEMBLY OUT OF UNIT