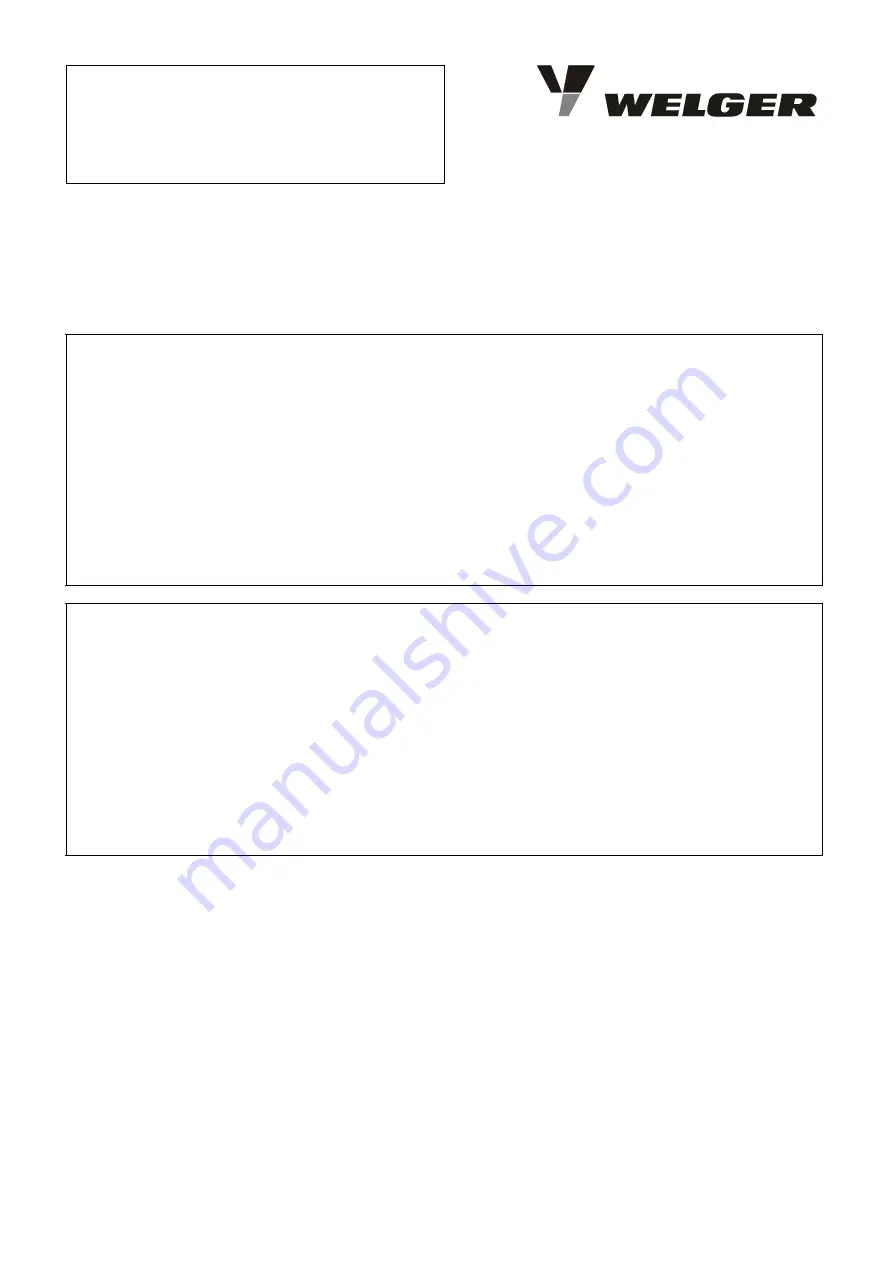
Send back to:
Lely International N.V.
TSS (Technical Service Support)
Postfach 1965
D-38289 Wolfenbüttel
M
Complete this form on delivery of the machine and
return it within 4 weeks
.
Possible guarantee requests cannot be handled before this document has not been sent back.
Customer
Name:
..................................................................................
Postcode/place:
..................................................................................
Phone:
..................................................................................
Street:
...................................................................................
Land/State:
...................................................................................
eMail:
...................................................................................
Marketing partner/Importer
Name:
..................................................................................
Postcode/place:
..................................................................................
Phone:
..................................................................................
Street:
...................................................................................
Land/State:
...................................................................................
eMail:
...................................................................................
..............................
.............................................................
Date
Signature Customer Service
Summary of Contents for RPC 445 TORNADO
Page 2: ......
Page 125: ...MAINTENANCE BALER LELY WELGER y RPC 445 Tornado 117 Figure 101...
Page 131: ...MAINTENANCE BALER LELY WELGER y RPC 445 Tornado 123 10 23 2 Control electronics SG 2 A B...
Page 132: ...MAINTENANCE BALER 124 LELY WELGER y RPC 445 Tornado 10 23 3 Control electronics SG 3 A B...
Page 144: ......