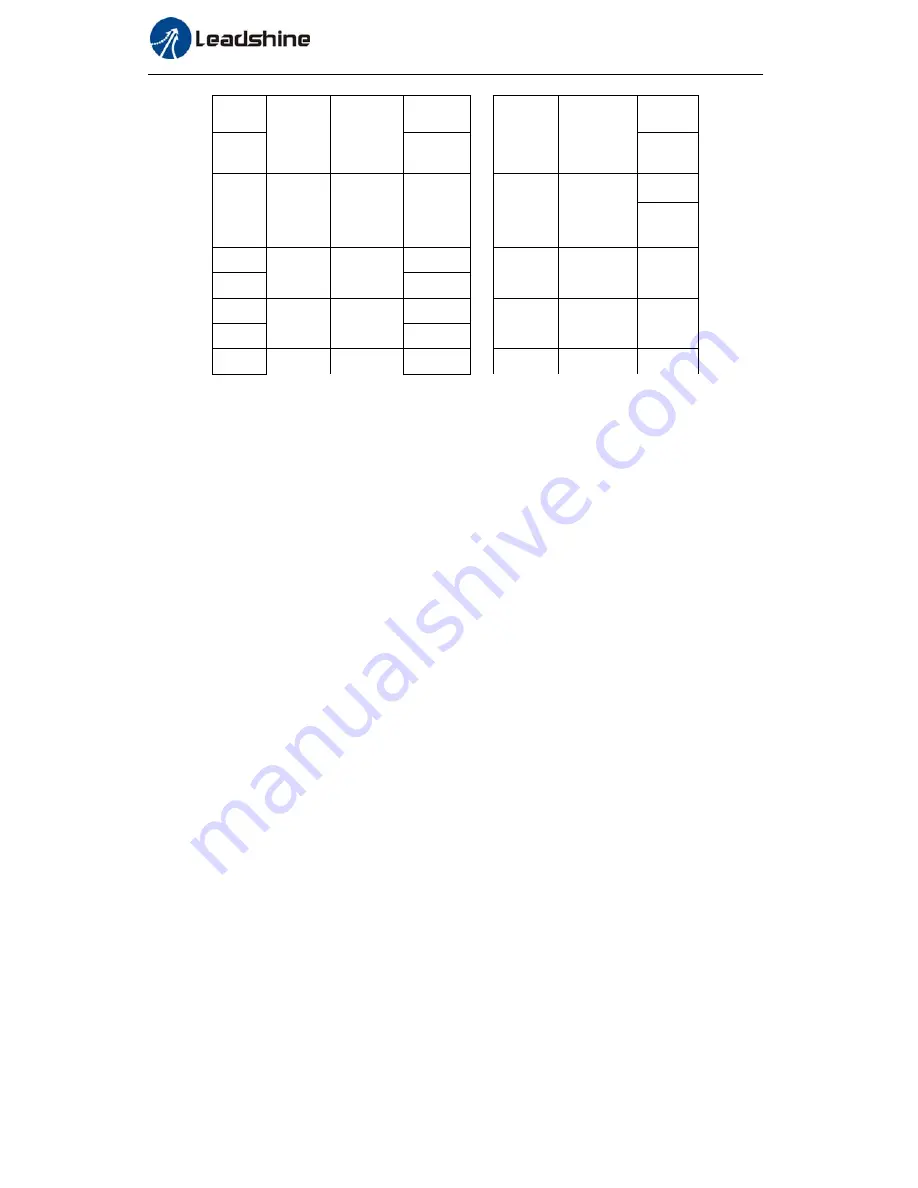
77
User
Manual
for
ELD2
Servo
5
NUM1
Data
quantity
Word
Hi
NUM
Actually
written
data
quantity
Hi
6
Lo
Lo
7
NUM2
Data
quantity
Byte
2
X
NUM1
CRC
check code
Lo
Hi
8
DATA1
DATA1
Hi
9
Lo
10
DATA2
DATA2
Hi
11
Lo
12
CRC
check
d
Lo
62 00
first address mapped to Pr9.00
00 08
8 consecutive operating addresses from 62 00 to 62 07
,
mapped to Pr9.00~Pr9.07
10
Hexadecimal data of the number of data
,
8 register
,
each address data is divided into high
and low bits
,
8*2=16
00 01
data written down to the first addresses of 6200 mapped to Pr9.00
Motion Model
,
Absolute positioning mode
00 01 86 A0
data written down to the second and third addresses of 6201 mapped to Pr9.01
;
6202
mapped to Pr9.02
Hexadecimal data of position=100000plus. All positions in PR mode are in units of
10000P/r
,
therefore, 00 01 86 A0 represents ten turns of motor rotation
01 F4
data written down to the fourth addresses of 6203 mapped to Pr9.03
Hexadecimal data of Speed=500r/min
00 64
data written down to the five addresses of 6204 mapped to Pr9.04
Hexadecimal data of acceleration time=100ms
00 64
data written down to the six addresses of 6205 mapped to Pr9.05
Hexadecimal data of deceleration time=100ms
00 00
data written down to the seven addresses of 6206 mapped to Pr9.06
Hexadecimal data of the delay time=0ms
00 10
data written down to the eight addresses of 6207 mapped to Pr9.07
,
to trigger the action
,
Immediately trigger method
(
1P
,
Immediately trigger path-P
,
The sample Pr9.00~9.07 is
the positioning related data of path-0
)
67 B3
the CRC verification code, do not have to directly input, click the corresponding send area
verification button automatically generated
The final analysis is as follows: speed is 500r/min, acceleration and deceleration time is 100ms, and
the position of absolute positioning is 10 rotation
11 10 62 00 00 08 10 00 01
00 00 00 00
01 F4 00 64 00 64 00 00 00 10 3B 73
The final analysis was performed at a speed of 500r/min, acceleration and deceleration time of 100ms,
and the position of absolute positioning 0 rotation was taken
Homing
:
11 06 60 02 00 21 F4 82
(
Back to origin high-speed, low-speed, and back to zero mode can
be set in the eighth set of parameters, using default values this time
)
Caution
:
In Pr mode, the origin induction switch is connected to the driver, which is different from the
impulse control. Limited by conditions, only the current position can be demonstrated to the
customer
:
Write 0x021
,
The current location manually set to zero.
。
The frame format function is
:
11
slave ID 17
06
function code
,
write single data