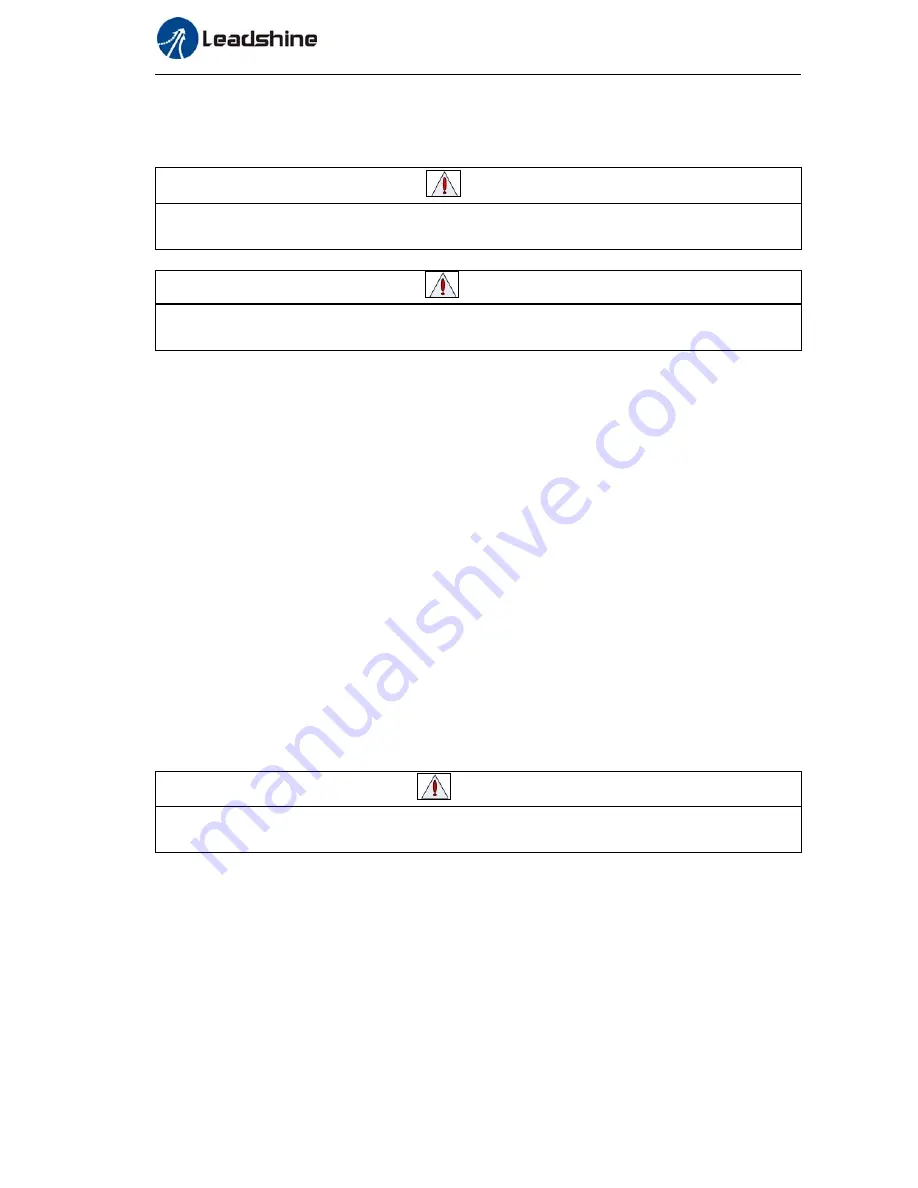
11
User
Manual
for
ELD2
Servo
Chapter 3 Wiring
Warning
The workers of participation in wiring or checking must possess sufficient ability do this job.
The wiring and check must be going with power off after five minutes.
Caution
Ground the earth terminal of the motor and driver without fail.
The wiring should be connected after servo driver and servo motor installed correctly
3.1 Wiring
3.1.1 Wire Gauge
(1)Power supply terminal TB
●
Diameter: Vdc , GND, PE, U, V, W terminals diameter
≥
1.5mm
2
(AWG14-16)
●
Grounding: The grounding wire should be as thick as possible, drive servo motor the PE terminal point
ground, ground resistance <100
Ω
.
●
Use noise filter to remove external noise from the power lines and reduce an effect of the noise generated
by the servo driver.
●
Install fuse (NFB) promptly to cut off the external power supply if driver error occurs.
(2) The control signal CN1 feedback signal CN2
●
Diameter: shielded cable (twisting shield cable is better), the diameter
≥
0.12mm
2
(AWG24-26), the
shield should be connected to FG terminal.
●
Length of line: cable length should be as short as possible and control CN1 cable is no more than 3
meters, the CN2 cable length of the feedback signal is no more than 20 meters.
●
Wiring: be away from the wiring of power line, to prevent interference input.
●
Install a surge absorbing element for the relevant inductive element (coil),: DC coil should be in parallel
connection with freewheeling diode reversely; AC coil should be in parallel connection with RC snubber
circuit.
Attention
Match the colors of the motor lead wires to those of the corresponding motor output terminals (U.V.W)
Never start nor stop the servo motor with this magnetic contactor.