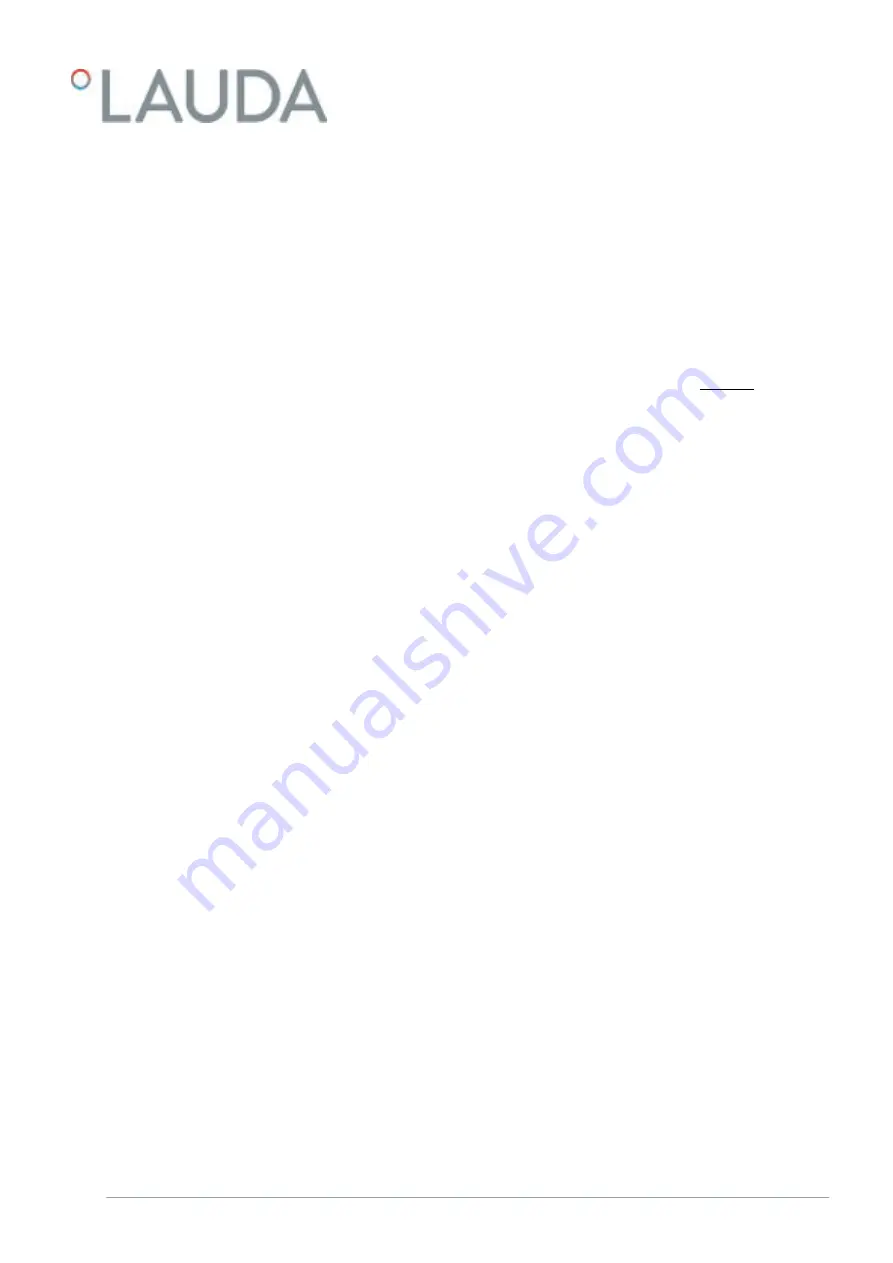
3.
Enter the value.
4.
Confirm the new value with the [Enter key].
The new value has been accepted.
6.4.4 Activate control variable
If the device is to be controlled to the internal control variable or an external
control variable, you must set it accordingly. When setting, the old control
variable with its set values is automatically deactivated. Only one control
variable can be actively selected.
List of the possible control variables
n
[Intern Pt1000]
n
[Extern Pt100]
n
[Extern analog]
n
[Extern serial]
n
[Extern USB]
n
[Extern Ethernet]
n
[Extern EtherCAT]
n
[Extern Pt100-2]
Personnel:
n
Operating personnel
1.
Press the Enter key to open the menu.
2.
Select the menu items
Setup
Control
Contr. Variable
.
The active control variable is marked with a checkmark.
3.
Scroll to another control variable and select it with the Enter key.
The new control variable is valid with immediate effect.
V4
Integral process thermostats with flow control unit
89 / 171