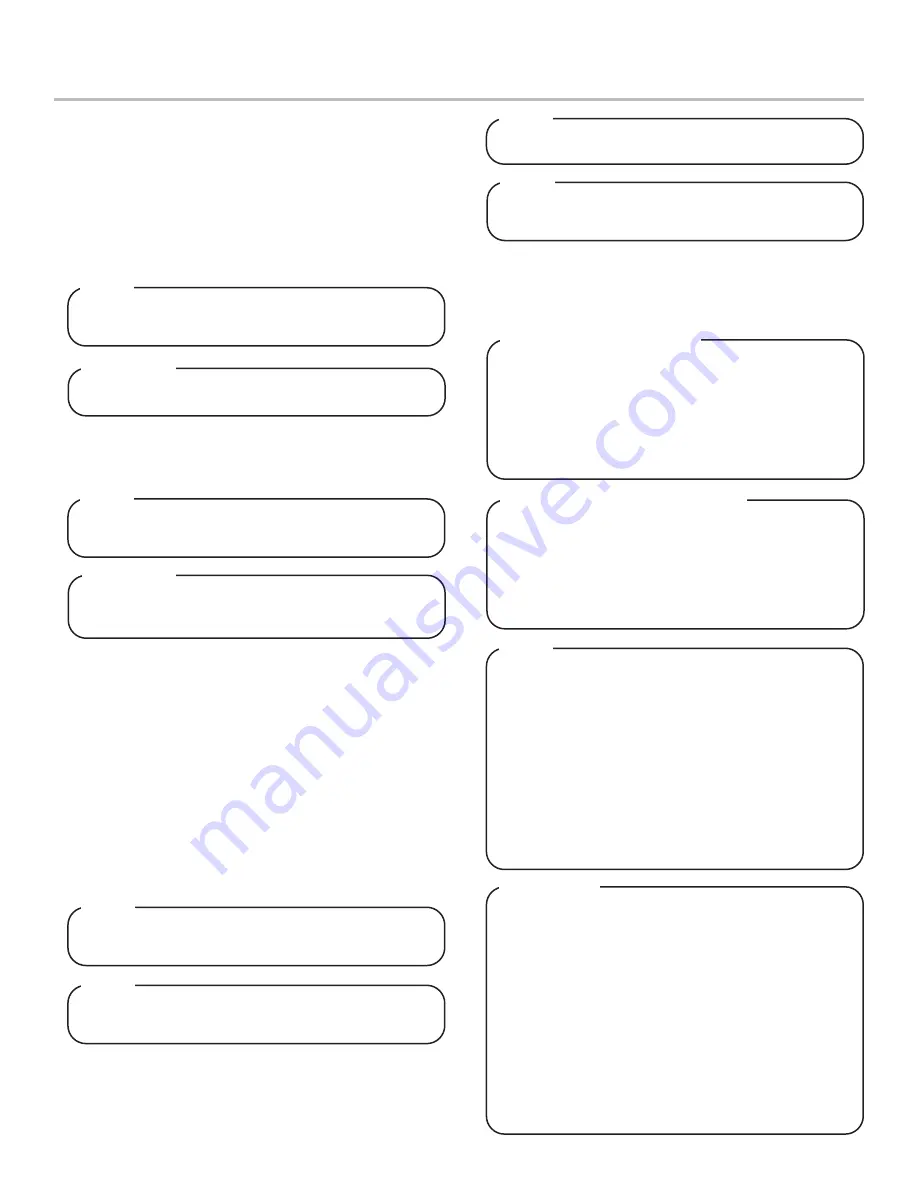
4
INSTALLATION
Unpack the Dispenser
1.
Set shipping carton upright on the floor then cut package
banding straps and remove.
2. Open top of carton and remove interior packaging.
3.
Lift carton up and off of the unit.
4. Remove plywood shipping base from unit by moving unit so
that one side is off the counter top or table allowing access
to screws on the bottom of the plywood shipping base.
If unit is to be transported, it is advisable to leave the
unit secured to the plywood shipping base.
NOTE
Inspect unit for concealed damage. If evident, notify
delivering carrier and file a claim against the same.
NOTE
5. Remove accessory kit and loose parts from ice compartment.
6. Clean ice chute and ice bin using cleaning instruction on
page 20.
Selecting/Preparing Counter Location
1. Select a level, well ventilated location that is in close
proximity to a properly grounded electrical outlet, within five
(5) feet (1.5 m) of a drain, a water supply that meets the
requirements shown in the Specifications section found on
page 3, and away from direct sunlight or overhead lighting.
2.
Sufficient clearance must be provided, if an ice maker is not
installed, to allow filling ice compartment from a five gallon
bucket (a minimum of 16 inches is recommended).
3. The selected location should be able to support the weight of
the dispenser, ice and possibly an icemaker being installed
after counter cut out is made. Total weight (with icemaker) for
this unit could exceed 800 pounds (363.6kg).
Lancer does
NOT
recommend the use of shaved or
flake ice in the dispenser.
NOTE
4. Unit may be installed directly on counter-top. Once installed
directly on the counter, unit must be sealed to the count-
er-top with an FDA approved sealant.
5. Select a location for the remote pump deck, syrup pumps,
CO
2
tank, syrup containers, and water filter (recommended).
6. Cut out required opening for the water, syrup, and CO
2
lines
in the designated dispenser location.
In order to facilitate proper dispenser drainage, ensure
that the dispenser is level, front to back and side to
side. Place a level on the top of the rear edge of the
dispenser. The bubble must settle between the level
lines. Repeat this procedure for the remaining three
sides. Level unit if necessary. For optimum perfor-
mance place the unit at a 0° tilt. The maximum tilt is 5°.
Leveling the Dispenser:
NSF listed units must be sealed to the counter.
NOTE
To ensure that beverage service is accessible to all
customers, Lancer recommends that counter height
and equipment selection be planned carefully. The
2010 ADA Standards for Accessible Design states that
the maximum reach height from the floor should be no
more than 48” if touch point is less than 10” from the
front of the counter, or a maximum of 46” if the touch
point is more than 10” and less than 27” from the front
of the counter. For more information about the
customer’s legal requirements for the accessibility of
installed equipment, refer to 2010 ADA Standards for
Accessible Design - http://www.ada.gov.
NOTE
Si l’appareil doit être transporté, il est conseillé de le lais-
ser fixé sur la base d’expédition en contreplaqué.
REMARQUE
Inspectez l’appareil pour déceler des dommages cachés.
Si l’appareil est endommagé, avisez le transporteur et
soumettez-lui une réclamation.
REMARQUE
Lancer recommande de ne
PAS
utiliser de glace pilée ou
de glace en écailles avec le distributeur.
NOTE
Toute unité homologuée NSF doit être scellée sur le
comptoir.
NOTE
Afin de faciliter une vidange complète, assurez-vous que
l’appareil est de niveau sur les axes avant arrière et gauche
droit. Placez un niveau sur le bord arrière de la distribu-
trice. La bulle doit se situer entre les deux lignes. Répétez
la procédure sur les trois autres côtés. Ajustez le niveau de
l’appareil si nécessaire. Pour un résultat maximal, réglez
l’inclinaison à 0°. L’inclinaison maximale est de 5°.
Mise à niveau de la distributrice
Pour s’assurer que le service de boissons est acces-
sible à tous les clients, Lancer recommande que la
hauteur du comptoir et le choix de l’équipement soient
soigneusement planifiés. Les normes ADA 2010 pour
la conception accessible stipulent que la hauteur de
portée maximale depuis le sol ne doit pas dépasser 48
pouces si le point de contact est à moins de 10 pouces
de l’avant du comptoir, ou un maximum de 46 pouces
si le point de contact est plus à 10 ”et à moins de 27”
de l’avant du comptoir. Pour plus d’informations sur les
exigences légales du client concernant l’accessibilité
des équipements installés, reportez-vous aux normes
ADA 2010 pour la conception accessible -
http://www.ada.gov.
REMARQUE