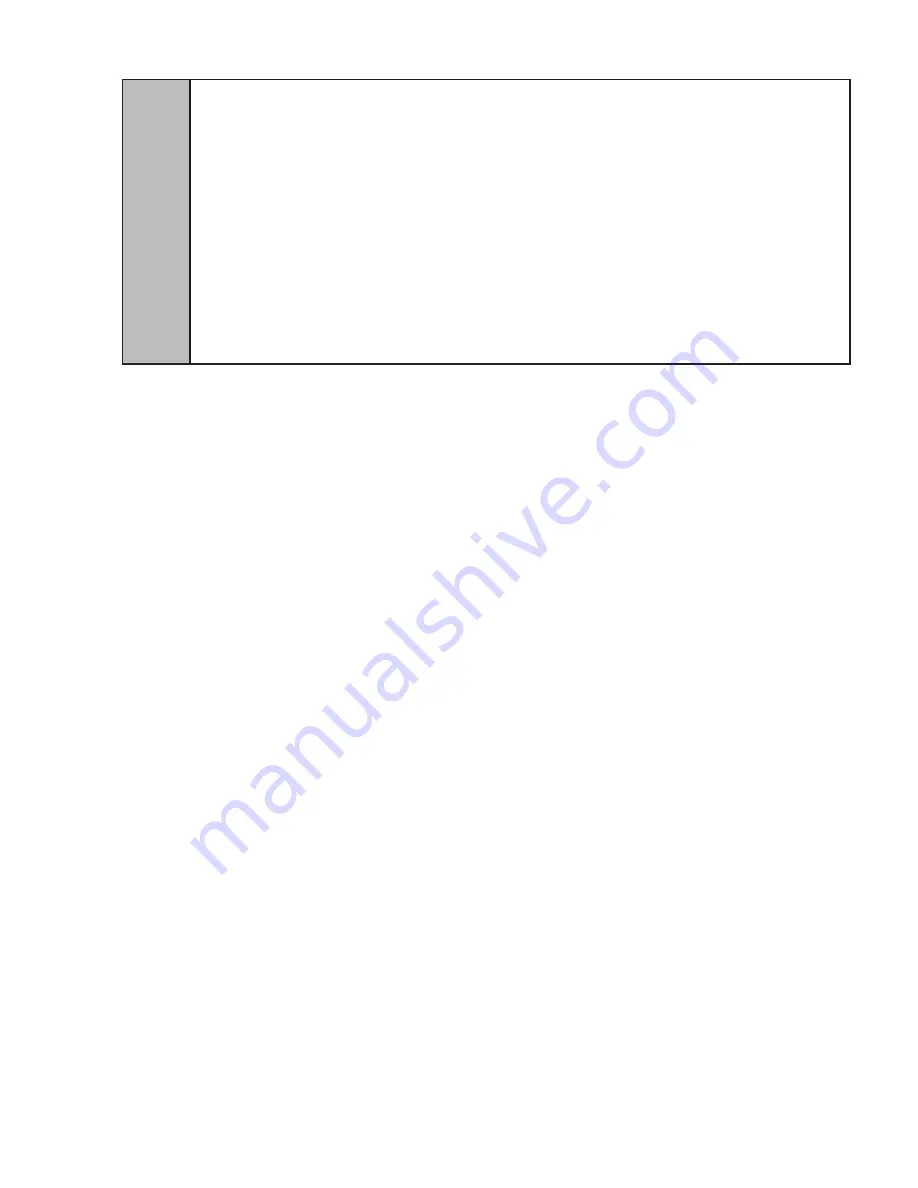
1.12 CONNECTING BAG-IN-BOX (BIB) SYRUP SUPPLY TO UNITS WITH BUILT-IN SYRUP PUMPS
A. Remove the protective caps from the syrup pump inlets and connect syrup inlet tube
assemblies furnished in the installation kit to the syrup pumps. Lubricate o-rings before
installation using an FDA approved lubricant or clean water. Be careful not to cut o-rings when
installing in pump.
B. Mark syrup tube assemblies at BIB hose connector end with product ID tape.
C. Route the syrup supply tubes from the unit through hole in counter to the BIB syrup supply.
D. Dip hose connectors in a cup of warm, clean water.
E. Attach the BIB hose connectors to the appropriate syrup flavor.
1.13 CONNECTING TO BAG-IN-BOX (BIB) SYRUP SUPPLY TO REMOTE SYRUP PUMPS
A. To connect CO2 regulator assembly to the CO2 cylinder, see Section 1.11, Steps A - C.
B. Place the remote BIB syrup supply and pumps in a convenient location.
C. Attach the syrup supply tubes to the dispenser’s syrup inlet fittings (located behind the splash
plate) using a 21/32 inch (17.0 mm) Oetiker clamp for each syrup flavor.
D. Route the syrup supply tubes to the remote syrup pumps.
E. Complete installation of the remote syrup pump system following the manufacturer’s
instructions.
1.14 CONNECTING TO REMOTE PRESSURIZED SYRUP SUPPLY (FIGAL)
A. To connect CO2 regulator assembly to the CO2 cylinder, see Section 1.11, Steps A - C.
B. Place the five gallon (figal) syrup containers and the CO2 cylinder and regulator set in a
convenient
location.
C. Attach the syrup supply tube assembly to the dispenser’s syrup inlet fittings (located behind the
splash plate) using a 21/32 inch (17.0 mm) Oetiker clamp for each syrup flavor.
D. Route the syrup supply tubes to the figal syrup containers and attach them to the appropriate
syrup
flavor.
1.15 PURGING THE CARBONATION SYSTEM
A. Set the adjustable back blocks to deliver carbonated water (see Section 1.20).
B. The relief valve for the built-in carbonator is located on the right hand side of the unit’s
carbonator deck. Lift the yellow lever on the top of the relief valve until water flows from the
holes in the relief valve. Then release the relief valve.
C. Reconnect the control box to the carbonator pump.
D. Back off on the CO2 regulator pressure adjusting screw all the way. Open the CO2 cylinder
handle slowly. Turn the CO2 pressure regulator up slowly to 75 PSIG (0.510 MPA).
E. Activate a dispensing valve until water and syrup are flowing steadily from the valve.
F. Repeat procedure “D” for each valve.
G. Check all of the unit’s syrup, water and CO2 connections for leaks and repair if necessary.
NOTE:
To check for CO2 leaks, close the valve on the CO2 tank and observe for five (5)
minutes if the pressure to the system drops. Open the cylinder valve after check.
H. Replace the unit’s bonnet, splash plate and cup rest.
!
WARNING
THE SYRUP INLET TUBE ASSEMBLIES (SHIPPED WITH THE INSTALLATION KIT) ARE EIGHT (8) FEET
(2.4 M) LONG. THESE LINES CAN BE EXTENDED UP TO A MAXIMUM OF 12 FEET (3.7 M). THE MAXIMUM HEIGHT
OF THE PUMPS ABOVE THE LOWEST BIB PACKAGE SHOULD NOT EXCEED EIGHT (8) FEET (2.4 M). IF EITHER
THE HEIGHT OF PUMPS OR LENGTH OF INLET LINE LIMITATIONS IS EXCEEDED, REMOTE SYRUP PUMPS OR
PRESSURIZED SYRUP CONTAINERS SHOULD BE USED.
ADVERTENCIA
LOS CONJUNTOS DE TUBERÍA DE ENTRADA DE SYRUP (SUMINISTRADOS CON EL KIT DE
INSTALACIÓN) TIENEN OCHO (8) PIES (2,4 M) DE LARGO. ESTAS LÍNEAS SE PUEDEN EXTENDER HASTA UN
MÁXIMO DE 12 PIES (3,7 M). LA ALTURA MÁXIMA DE LAS BOMBAS POR ENCIMA DEL PAQUETE BIB MÁS BAJO
NO DEBE SUPERAR LOS OCHO (8) PIES (2,4 M). SI SE SUPERAN LAS LIMITACIONES EN CUANTO A LA ALTURA
DE LAS BOMBAS O EL LARGO DE LA LÍNEA DE ENTRADA, HAY QUE USAR CONTENEDORES DE SYRUP
PRESIONIZADOS O BOMBAS DE SYRUP REMOTAS.
AVERTISSEMENT
LES GROUPES DE TUBE D’ENTRÉE DE SIROP (EXPÉDIÉES AVEC LA TROUSSE
D’INSTALLATION) SONT HUIT (8) PIEDS (2,4 M) DE LONG. CES LIGNES PEUVENT ÊTRE PROLONGÉES JUSQU’À
UN MAXIMUM DE 12 PIEDS (3,7 M). LA HAUTEUR MAXIMUM DES POMPES AU-DESSUS DU SAC DE CONCENTRÉ
LE PLUS BAS NE DOIT PAS DÉ PASSER HUIT (8) PIEDS (2,4 M). SI LA HAUTEUR DES POMPES OU LA LIMITE DE
LONGUEUR DE LA CONDUITE D’ENTRÉE EST DÉPASSÉE, DES POMPES DE SIROP À DISTANCE OU DES
CONTENEURS DE SIROP PRESSURISÉS DOIVENT ÊTRE UTILISÉS.
13
Summary of Contents for 9000 series
Page 33: ...NOTES 33...