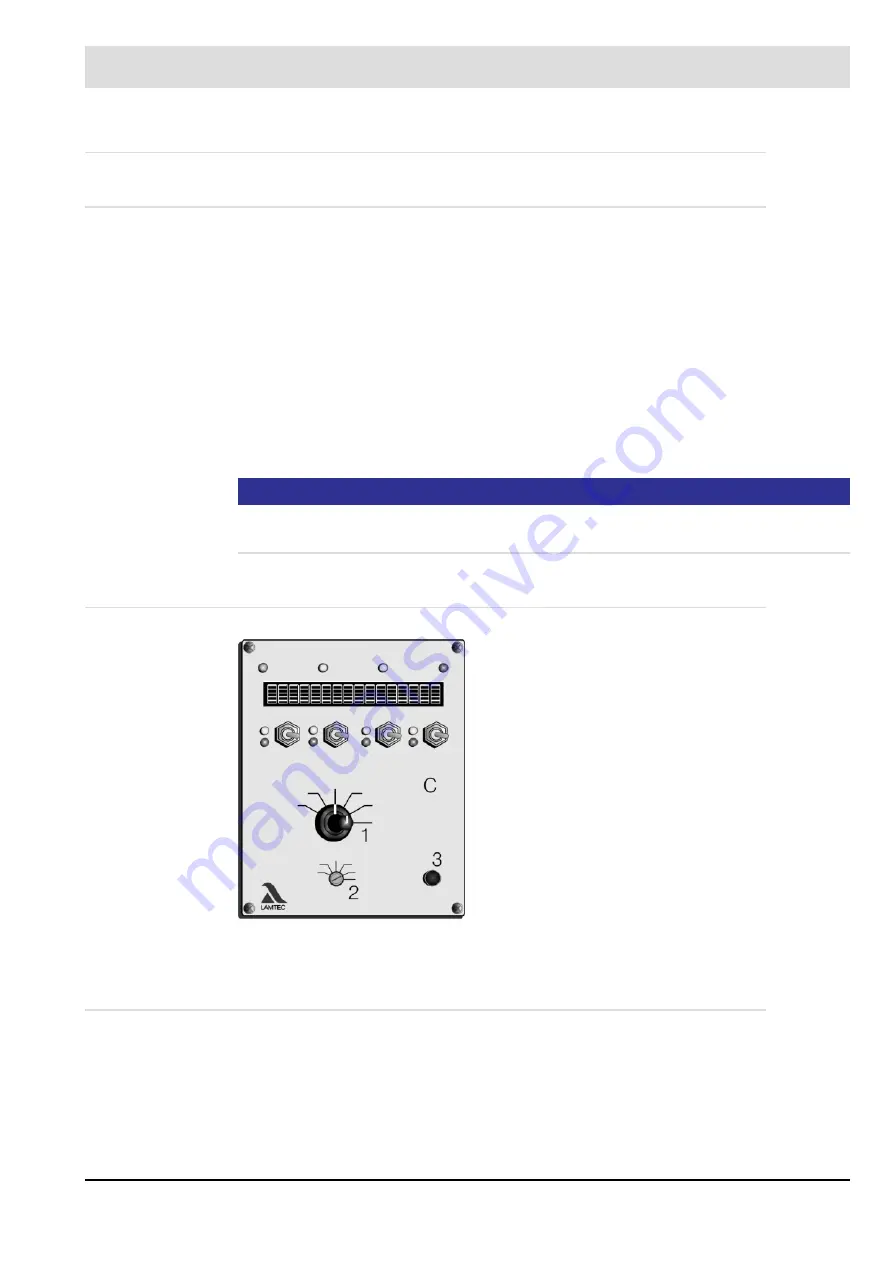
64
6
Commissioning
6.7.4
Correctional Range
6.7.4.1 Correction Range Settings
Use parameter 517 to adjust the correction range from 0 to 999.
NOTICE
The correction range (P517) is set to 0 (factory setting) and it must be set during commission-
ing. Otherwise, it could lead to faults during the probe dynamic test.
6.7.4.2 Calling up the Set Correction Mode
The correction should be taken into account during later programming. The correction should
be able to take effect before the VMS reaches actuator stop.
6.7.4.3 Edit Correction Range
In order to change the correction range, a parameter change must be made. This parameter
is accessible through customer access level (level 1).
Proceed as described in parameter settings.
The values for the correction range are saved in parameter P 517 and P 597.
Example:
Ccorrection mode P 437 for O
2
trim is +60/-40
CO control is +50/-50.
Correction range P 517 is 100 (digit).
This means:
The adjusting range of the setpoint which can be modified in correc-
tion mode should be b60 (digit) and -40 (digit).
E.g. With a current setpoint of 200 digit, the modifiable by correction
adjusting range lies between 260 digit (excess air) and 160 digit (air
deficiency).
Recommendation: You should chose the correction mode and the correction range in
that way, that the correction effect on the O
2
value is -2 to 3 vol.% O
2
.
Turn selector switch (1) to STATUS
Press ENTER (3)
The display shows the selected correction range
If both correction inputs operate on one channel, the
sums are shown (e.g. 15
points).
Press ENTER (3) again, or
Turn selector switch (1) back
return to normal display
Summary of Contents for VMS 4
Page 2: ......
Page 119: ...118 10 Appendix...
Page 129: ...128 10 Appendix Fig 10 9 Ger t 4 Ger t 5 with output regulator...
Page 141: ...140 10 Appendix 10 14 Declaration of Conformity...
Page 142: ...141 10 Appendix...
Page 143: ...142 10 Appendix 10 15 Protocol Example...
Page 144: ...143 10 Appendix 10 16 O2 Setpoint Curves...
Page 145: ...144 10 Appendix...