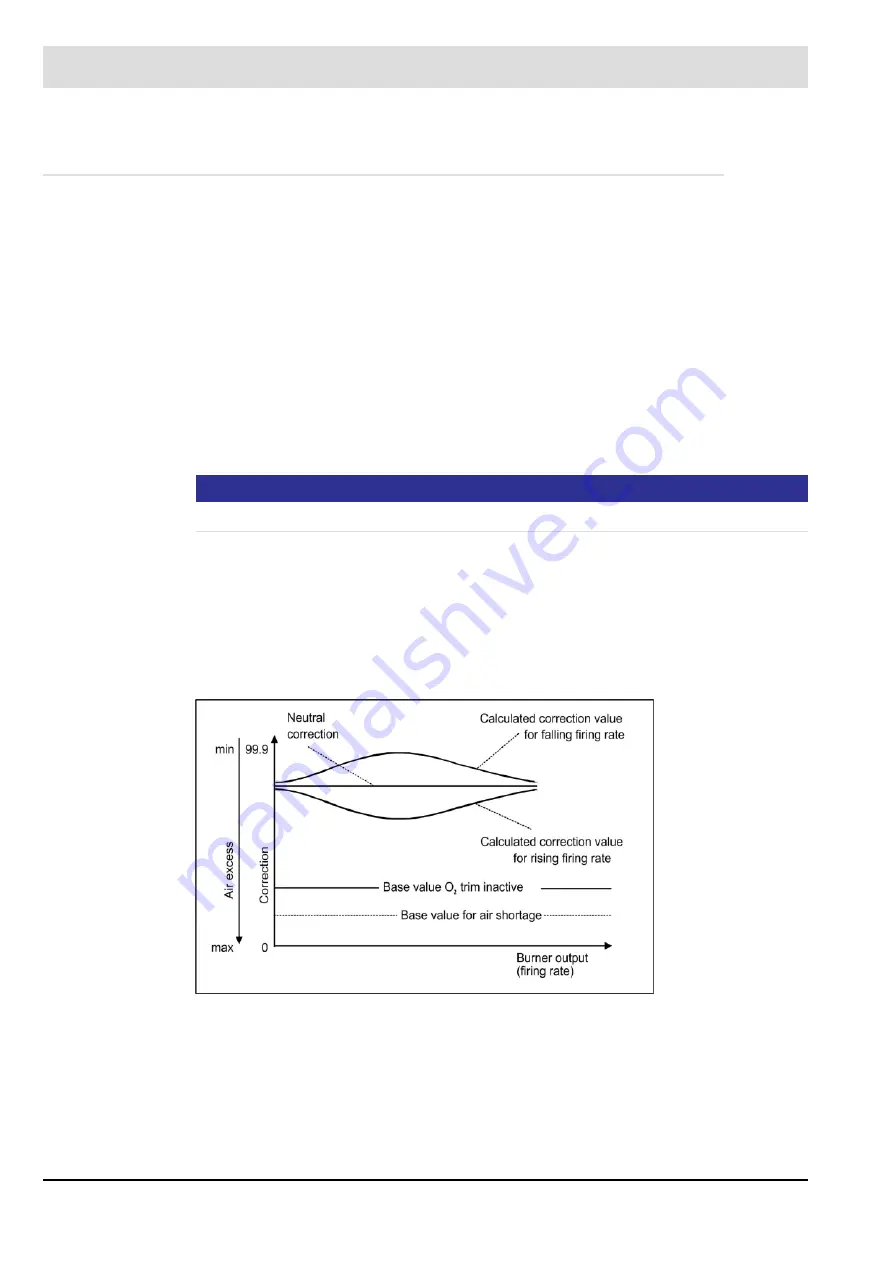
47
6
Commissioning
6.6.1.7 Correction Output Monitoring
The controlling strategies employed were specially developed and optimised for the circum-
stances prevailing in combustion facilities:
- Frequent output changes
- long lag time
During burner start-up, the O
2
controller remains on standby until it is ensured that plausible
O
2
measured values are being displayed. Factory setting 90 seconds after ignition -
this is adjustable via parameter (P 904).
During standby and ignition mode, the value for deactivated control would be given
(see
Fig. 6-1 Correction output monitoring
).
It is calculated automatically from the range set.
Ignition takes place with the neutral value.
The neutral value depends on the selected correction mode; e.g. at -50% to +50%, the output
correction value (neutral value) is 500, whilst at -30% to +70% it is 300.
NOTICE
The natural value correspond to the basic settings of the VMS
without control
In the case of fuel/curve switching during operation, the neutral value is output during the
switch-over. An air advance can be set to the neutral value by parameters 702 to 704.
O
2
trim is reactivated, with a time delay, once the switch-over is completed. Factory setting
30 seconds, adjustable via parameter (P 903).
Various control strategies are available.
In the event of a fault, ’O
2
trim base value deactivated’ or ’Base value for air shortage’ is out-
put, depending on the cause.
Fig. 6-1 Correction output monitoring
Summary of Contents for VMS 4
Page 2: ......
Page 119: ...118 10 Appendix...
Page 129: ...128 10 Appendix Fig 10 9 Ger t 4 Ger t 5 with output regulator...
Page 141: ...140 10 Appendix 10 14 Declaration of Conformity...
Page 142: ...141 10 Appendix...
Page 143: ...142 10 Appendix 10 15 Protocol Example...
Page 144: ...143 10 Appendix 10 16 O2 Setpoint Curves...
Page 145: ...144 10 Appendix...