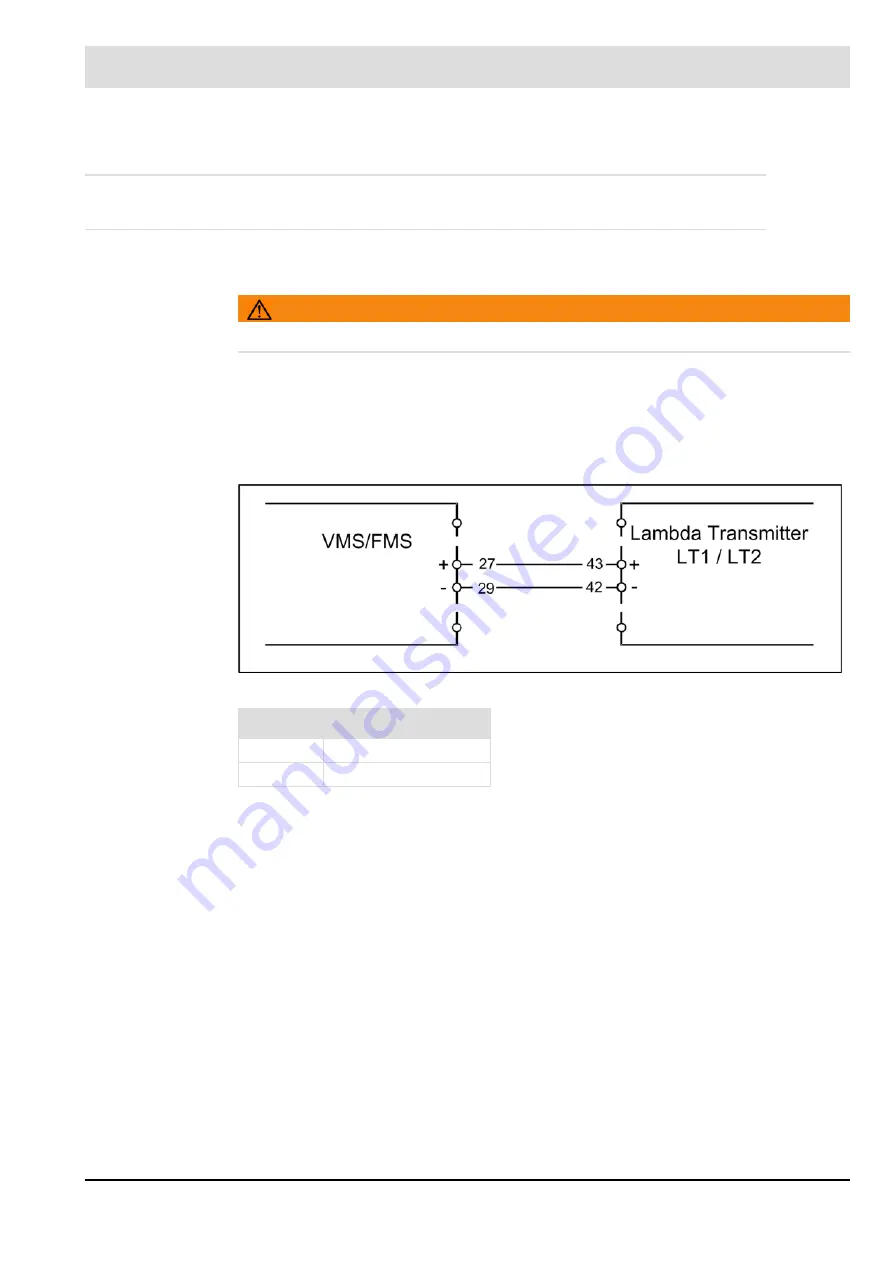
50
6
Commissioning
6.6.3
Connecting the O
2
Measurement Device
6.6.3.1 Via Analogue Interface
The default for the measured O
2
value is set via standard signal 0/4...20 mA to the VMS cor-
rection input 1.
WARNING!
Only O
2
meters whose t
90
response time is < 15 sec may be connected.
Release of the analogue interface is only possible at the factory (type 663R0030).In case of
doubt, please contact LAMTEC.
Range compensation via parameters P 919 and P 920
Factory setting: 4 ... 20 mA
0 ... 25,0 vol. % O
2
0 mA when O
2
measurement is at fault
Fig. 6-2 Electric connection VMS O
2
measurement device
Terminal
Description
27/29
Correction input 1
42/43
Analogue output 1
*
*
floating type 657R0051
Summary of Contents for VMS 4
Page 2: ......
Page 119: ...118 10 Appendix...
Page 129: ...128 10 Appendix Fig 10 9 Ger t 4 Ger t 5 with output regulator...
Page 141: ...140 10 Appendix 10 14 Declaration of Conformity...
Page 142: ...141 10 Appendix...
Page 143: ...142 10 Appendix 10 15 Protocol Example...
Page 144: ...143 10 Appendix 10 16 O2 Setpoint Curves...
Page 145: ...144 10 Appendix...