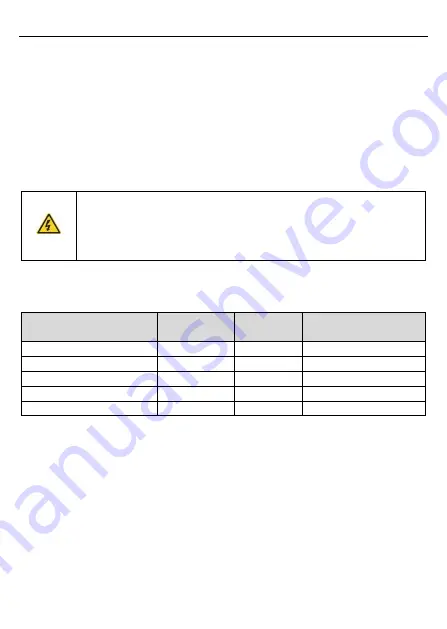
Ecowatt
®
Drive K120 series
Optional peripheral accessories
-157-
between the control cable and the power cable is 90 degrees.
If the inside of the motor is wet, the insulation resistance will decrease. If you think
there is moisture inside the motor, dry the motor and re-measure it.
C.4
Breaker and electromagnetic contactor
You need to add a fuse to prevent overload.
You need to configure a manually manipulated molded case circuit breaker (MCCB)
between the AC power supply and VFD. The breaker must be locked in the open state to
facilitate installation and inspection. The capacity of the breaker needs to be 1.5 to 2
times the rated current of the VFD.
According to the working principle and structure of breakers, if the
manufacturer's regulation is not followed, hot ionized gases may
escape from the breaker enclosure when a short-circuit occurs. To
ensure safe use, exercise extra caution when installing and placing
the breaker. Follow the manufacturer's instructions.
To ensure safety, you can configure an electromagnetic contactor on the input side to
control the switch-on and switch-off of the main circuit power, so that the input power
supply of the VFD can be effectively cut off when a system fault occurs.
VFD model
Fuse
(A)
Breaker
(A)
Contactor rated
current (A)
K120-0R4G-2
10
10
9
K120-0R7G-2
16
16
12
K120-1R5G-2
25
25
25
K120-2R2G-2
50
40
32
K120-004G-2
63
63
50
C.5
Reactors
When the voltage of the grid is high, the transient large current that flows into the
input power circuit may damage rectifier components. You need to configure an AC
reactor on the input side, which can also improve the current adjustment coefficient on
the input side.
When the distance between the VFD and motor is longer than 50 m, the parasitic
capacitance between the long cable and ground may cause large leakage current, and
overcurrent protection of the VFD may be frequently triggered. To prevent this from
happening and avoid damage to the motor insulator, compensation must be made by
adding an output reactor. If the distance between the VFD and motor is 50 m to 100 m,
select the reactor according to the following table. If the distance is longer than 100 m,
Summary of Contents for Ecowatt Drive K120 Series
Page 1: ......
Page 170: ...Ecowatt Drive K120 series Optional peripheral accessories 163 PB External braking resistor VFD...
Page 172: ......
Page 173: ......