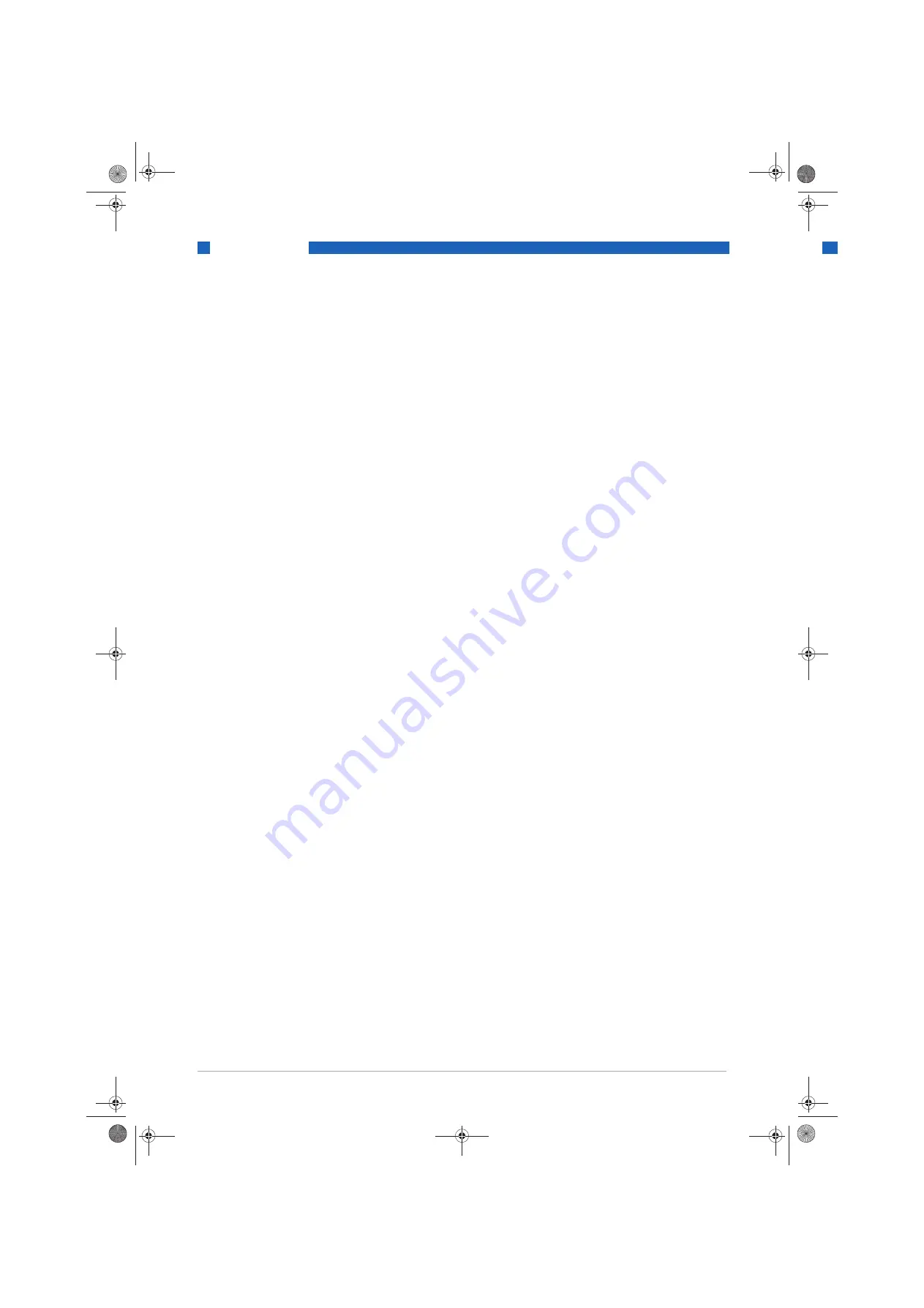
CONTENTS
4
www.krohne.com
01/2008 • 4000172301 - HB OPTIFLEX 1300 R02 en
OPTIFLEX 1300 C
3.8.4
Installation recommendations for non-metallic tanks and pits............................. 45
3.8.5
How to attach the weather protection to the instrument ....................................... 46
3.8.6
How to open the weather protection ....................................................................... 47
3.9 Electromagnetic compatibility........................................................................... 48
4 Electrical
connections ................................................................. 49
4.1 Safety instructions ............................................................................................. 49
4.2 Electrical installation: outputs 1 and 2.............................................................. 50
4.3 Electrical connection for current output ........................................................... 51
4.3.1
Non-Ex ..................................................................................................................... 51
4.3.2
Ex i............................................................................................................................ 51
4.3.3
Ex d........................................................................................................................... 52
4.4 Protection category............................................................................................ 53
4.5 Networks ............................................................................................................ 54
4.5.1
General information ................................................................................................ 54
4.5.2
Point-to-point networks .......................................................................................... 54
4.5.3
Multi-drop networks................................................................................................ 55
5 Start-up ....................................................................................... 56
5.1 Start-up checklist .............................................................................................. 56
5.2 Operating concept.............................................................................................. 56
5.3 Digital display screen......................................................................................... 57
5.3.1
Local display screen layout ..................................................................................... 57
5.3.2
Push-button functions............................................................................................. 57
5.3.3
Help screens............................................................................................................ 57
5.3.4
How to start the instrument .................................................................................... 58
5.4 Remote communication with PACTware™........................................................ 58
5.5 Remote communication with the AMS™ Device Manager ................................ 59
6 Operation ..................................................................................... 60
6.1 User modes ........................................................................................................ 60
6.2 Operator mode ................................................................................................... 60
6.3 Supervisor mode ................................................................................................ 62
6.3.1
General notes .......................................................................................................... 62
6.3.2
How to get access to the supervisor mode ............................................................. 63
6.3.3
Menu overview ......................................................................................................... 64
6.3.4
Push-button functions............................................................................................. 65
6.3.5
Function description................................................................................................ 68
6.4 Further information on instrument configuration ............................................ 85
6.4.1
Quick Links .............................................................................................................. 85
6.4.2
Protection of the instrument settings ..................................................................... 86
6.4.3
Network configuration............................................................................................. 86
6.4.4
Linearisation ............................................................................................................ 87
HB_OPTIFLEX1300_EN_D4_080428.book Page 4 Tuesday, April 29, 2008 2:47 PM