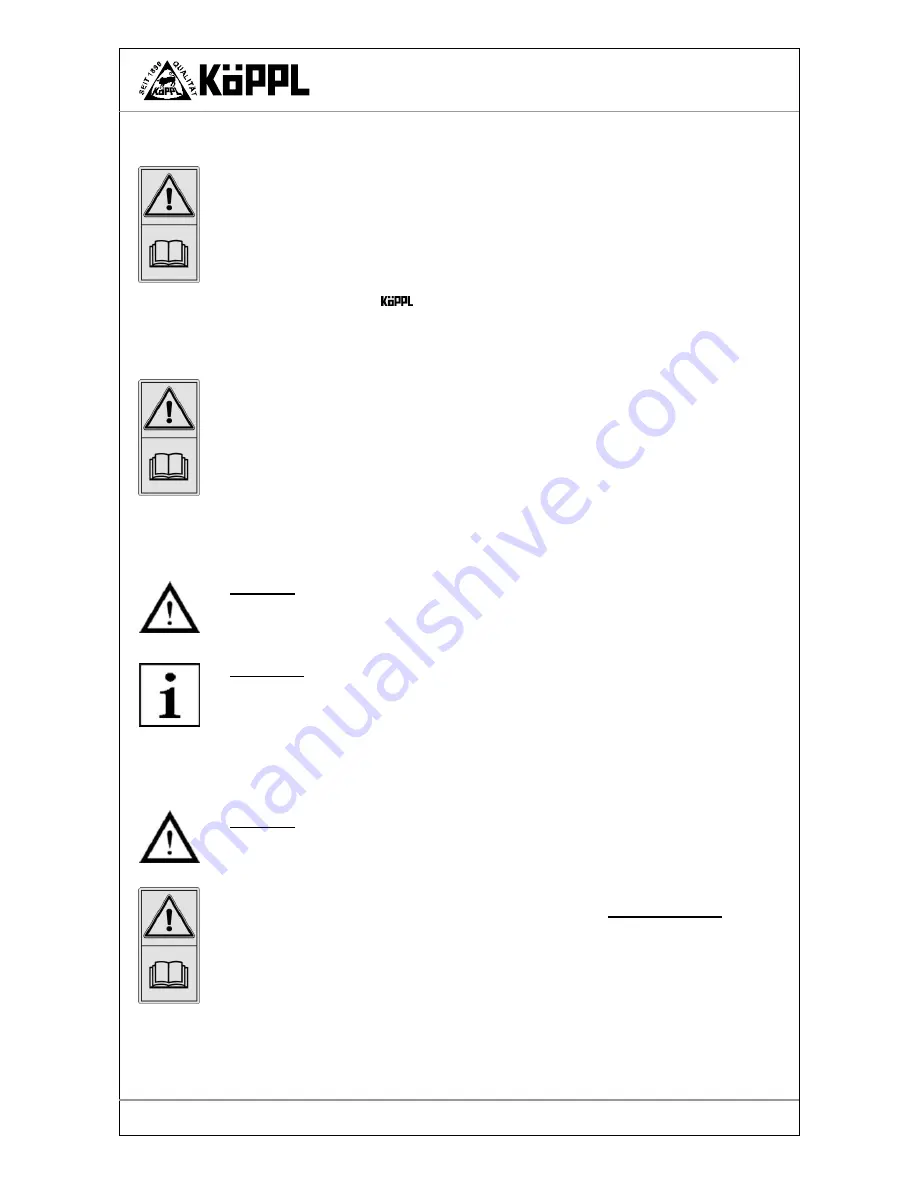
Page 16
Version 02-2010
Compakt-Comfort-2
Operation
Operation
In order to avoid damage to the machine and life-threatening injuries when putting the
machine into operation, it is essential to pay attention to the following points:
You must have read and understood
•
Chapter 1 ‘General safety instructions’
•
the engine manufacturer’s operating manual
•
the operating manual for each attached device
You may not operate the
2-wheel tractor before having done so.
1.
Commissioning
The following items must be checked before putting into operation for the first time:
•
Check the engine oil level (refer to the engine manufacturer’s operating manual).
•
Check the gearbox and hydraulic oil levels.
•
Check all safety devices.
•
Check the fuel level in the fuel tank.
•
Check that all screws, bolts and controls on the basic unit and attached devices are tight.
•
Remove all tools and foreign parts from the machine.
•
Adjust the steering shaft to the operator’s body size and in accordance with the purpose of
use.
Warning!
Exhaust gases contain carbon monoxide!
They are highly toxic if inhaled and can lead to death.
Important!
During the first 20 hours of operation (the running-in period) the engine should not be
operated up to its performance limit.
After about 10 hours of operation, check that all screws, bolts and controls on the basic
machine and attached devices are tight.
2.
Starting
Warning!
If the traction and device drive is engaged, you could be run over, causing serious injuries.
The traction and device drive must be disengaged when starting the engine.
Do not stand with your feet near the attached working device.
Please observe the following instructions when starting the tractor:
Turn the engine switch to the ON position and start the engine without depressing the
clutch/safety stop lever (see fig. 02, page 12). The twist-grip must always be in the 0
position. In the case of Easy-Drive the green LED on the rocker switch must light up when
the engine is running.
Follow the respective engine manufacturer’s operating manual when starting the engine –
start it according to the engine manufacturer’s operating manual. Once the engine is running,
bring the throttle lever to the middle position and allow the engine to warm up for a short time.
At temperatures under + 5° C you must allow the hydraulic drive to warm up for approx. 3
minutes at a low engine speed so that the oil can reach operating temperature and the drive can
function without problems. The twist-grip must thereby be in the 0 position and the clutch/safety
stop lever must be depressed, otherwise the oil pump will not run and the oil cannot warm up.