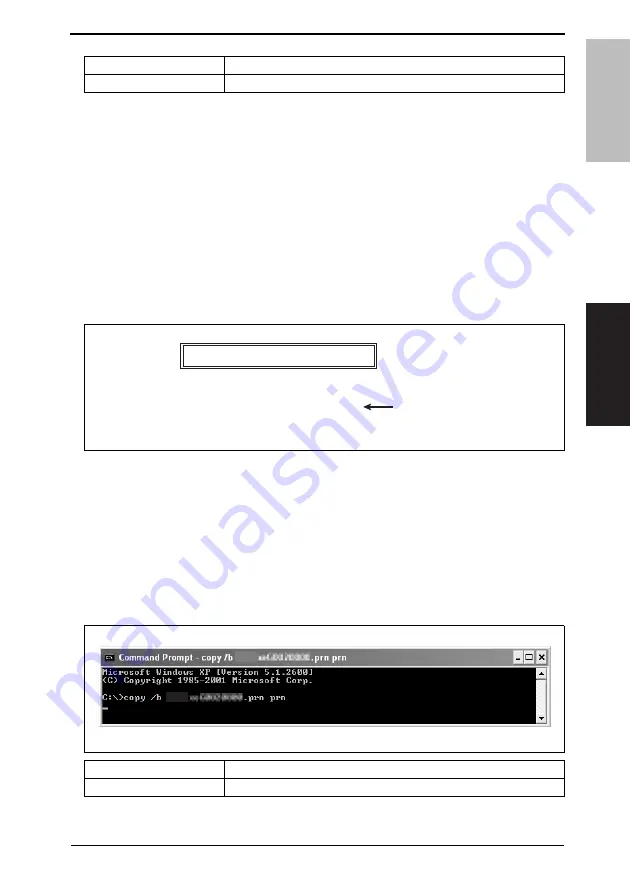
Field Service Ver. 1.0 May 2006
5. Firmware upgrade
31
magicolor 7450
Maintenance
6.
Wait until all of the data is sent.
While the data is being sent, [FIRMWARE UPDATE] and [PROCESSING] are alter-
nately displayed on the screen.
NOTE
• NEVER turn the printer Power Switch OFF and ON while data is being sent.
7.
After the data has finished being sent, the message [REBOOTING] appears in the con-
trol panel message display and the printer restarts.
8.
After the printer has restarted, check that a [READY] message is displayed.
9.
From the Menu, select [PRINT MENU]
→
[CONFIGURATION PG] and execute the
function. Then, check that the firmware [2] has been upgraded.
B. How to upgrade using the Parallel Interface
1.
Connect the machine to the PC using a parallel cable.
NOTE
• Check that printing is available through the parallel cable.
2.
Copy the firmware data and upgrading program to any directory on the PC.
3.
Start the Command Prompt and go to the directory in which the firmware data is
stored.
4.
Execute the following command to start the transfer of the firmware data to the printer.
(The screen shown below indicates that the firmware data resides on the C drive.)
Data to be upgraded
Command
FW upgraded data
> lpr -S XXX.XXX.XXX.XXX -P lp -o l 4039**********.prn
XXX.XXX.XXX.XXX : IP address of the machine
******
: File name of FW upgrade data
[2]
4039F2C519DA
PRINTER INFORMATION
DATE
TIME
CONTROLLER F/W
ENGINE F/W
BOOT F/W
TOTAL PAGE COUNT
SERIAL NUMBER
MM.DD.YYYY
HH.MM
403930G0120000(US)
403950F0150000(US)
403999G0110000
7
******
Data to be upgraded
Command
FW upgraded data
> copy /b 4039**********.prn prn
******: File name of FW upgrade data
4039F2E522DA
㪋㪇㪊㪐
㪋㪇㪊㪐
Summary of Contents for magicolor 7450
Page 1: ...SERVICE MANUAL 2006 05 2006 05 Ver 1 0 Ver 1 0 FIELD SERVICE magicolor 7450 magicolor 7450 ...
Page 3: ...ii Blank Page ...
Page 26: ...SERVICE MANUAL 2006 05 Ver 1 0 FIELD SERVICE Main Unit magicolor 7450 magicolor 7450 ...
Page 43: ...2 Product specifications Field Service Ver 1 0 May 2006 6 magicolor 7450 General Blank Page ...
Page 288: ...SERVICE MANUAL 2006 05 Ver 1 0 FIELD SERVICE Lower Feeder Unit ...
Page 317: ...3 Other Field Service Ver 1 0 May 2006 26 Lower Feeder Unit Maintenance Blank Page ...
Page 328: ...SERVICE MANUAL 2006 05 Ver 1 0 FIELD SERVICE Duplex Option ...
Page 333: ...1 Product specifications Field Service Ver 1 0 May 2006 2 Duplex Option General Blank Page ...
Page 345: ...6 Jam Display Field Service Ver 1 0 May 2006 14 Duplex Option Troubleshooting Blank Page ...