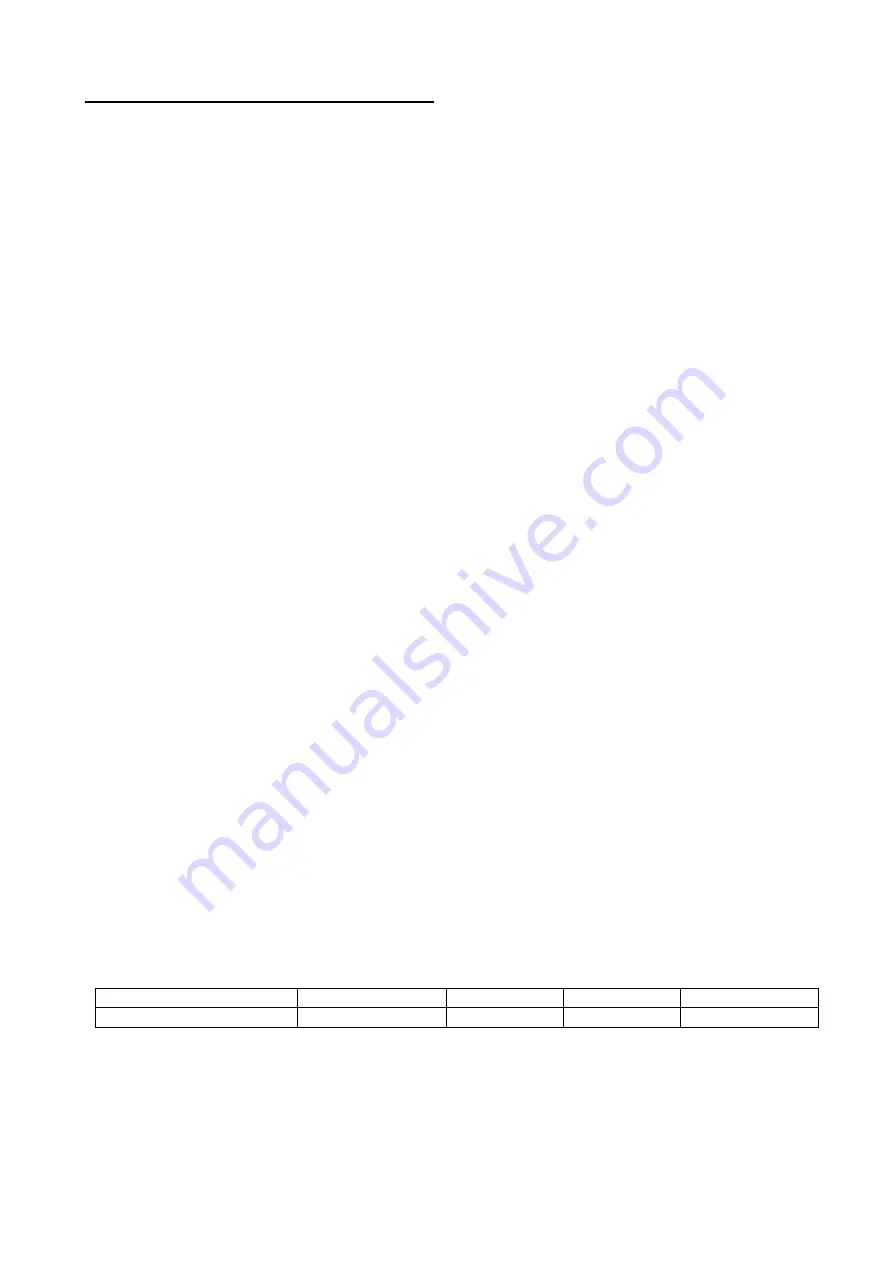
25
Specificities regarding the X-mark certificate
With regard to the specificities concerning the use limitations, installation and maintenance of Ex-
motors form the production range and inability to list them all here, we ask kindly the user and the
personnel authorized for installing the equipment to study the Manufacturer’s statement where all
limitations for the motor are stated.
Repair of these motors must be conducted by manufacturer KON
Č
AR - MES d.d. or listed authorized
repair services. In Republic of Croatia these are the ones listed in Registry of repairman under
technical supervision of Ex-Agency DZNMRH. In foreign countries these are repairman in compliance
with local regulations.
Without special written permission from the manufacturer for any action that has or may have
influence on anti-explosion protection of the motor (during warranty period or after), the liability lies on
the one carrying out the procedure, especially :
- when procedures are carried out on protective systems of Ex-protection “d/db” motors. During such
procedures it’s necessary to request instructions (and dimensions) from KON
Č
AR – MES d.d.
because air gaps are smaller than ones allowed by IEC 60079-0,-1 norm.
- The supply cables of motors for the ambient temperature of + 60°C shall be suitable for an operating
temperature equal or greater than 85°C, for ambient tempe80°C supply cable shall be suitable
for an operating temperature equal or greater than 105°C.
- The screws used for fastening of the parts of motor enclosure size 7AT90-180, 7AT280, 7AT315
shall have a yield stress higher than 800 N/mm
2
.
- The screws used for fastening of the parts of motor enclosure size 200, 225 and 250 shall have a
yield stress higher than 1200 N/mm
2
for the assembly with shield and 800 N/mm
2
for the assembly
with terminal box.
- The screws used for fastening of the parts of motor enclosure size 7ATL90-315 shall have a yield
stress higher than 700 N/mm
2
.
- The motor provided with the cables permanently connected, shall have these cables protected
against the risk of damage due to mechanical stresses. The end connections shall be made according
to one of the types of protection indicated in the IEC 60079-0 standards according to the installation
rules in force in site of installation.
-Motor is built in compliance with IEC 60034-25, so it is capable to work with power supply from
frequency converter ( 2p=2; 5 to 87 Hz and 2p=4, 6, 8; 5 to 100 Hz). According to IEC 60034-11 for
motor winding there are according to temperature class ( T4) 3xPTC-130°C or ( T3)150°C ± 5°C
sensors. Characteristics of thermal sensors are in compliance with DIN 44081/44082. Speed
regulation range is defined by the data stated on motor name plate, and given torque reduction
diagram defines or torque and power. Frequency converter used for this drive must be in compliance
with IEC 60034-25 for protection of over voltage and from voltage gradient change. Protection from
short-circuit of any kind (to phase, to earth) must be provided inside frequency converter device.
If repairs are not executed by KON
Č
AR-MES, they must be carried out at workshops which have the
necessary equipment and with adequate technical expertise concerning the motor protection types. If
repair work has to be performed on parts that influence the flameproof protection characteristics the
motor construction data must not be changed (for example: dimensions of joints, windings
characteristics, etc.) and the repaired parts must be tested.
Flameproof motors must be protected against overloads with automatic power supply disconnection
by using a countdown protection device or by using a device to control the temperature directly by
means of temperature sensors inserted in the windings. It is necessary to ensure that the motor
ventilation is not impaired by obstacles positioned in the surrounding area when flameproof motors
are installed. The terminal box of the motor must always be closed before starting the motor.
For Ex d type terminal box: lightly re-grease machined flamepath surfaces, fit terminal box lid and
tighten the fixing bolts to torques as indicated below:
Screw size:
M6
M8
M10
M12
Torque:
10 Nm
23 Nm
35 Nm
80 Nm
(Screws of steel class: 8.8)
For Ex e type terminal box: inspect the sealing gasket is not damaged, wipe clean the mating
surfaces between the gasket and terminal box and tighten the fixing bolts until the gasket is fully
pressed ensuring a tight seal.
The inspections and maintenance of flameproof motors shall be executed in compliance with the
criteria of the IEC 60079-25 standard. The electrical connection terminals must be tightened fully to
avoid high contact resistances and consequential overheating.