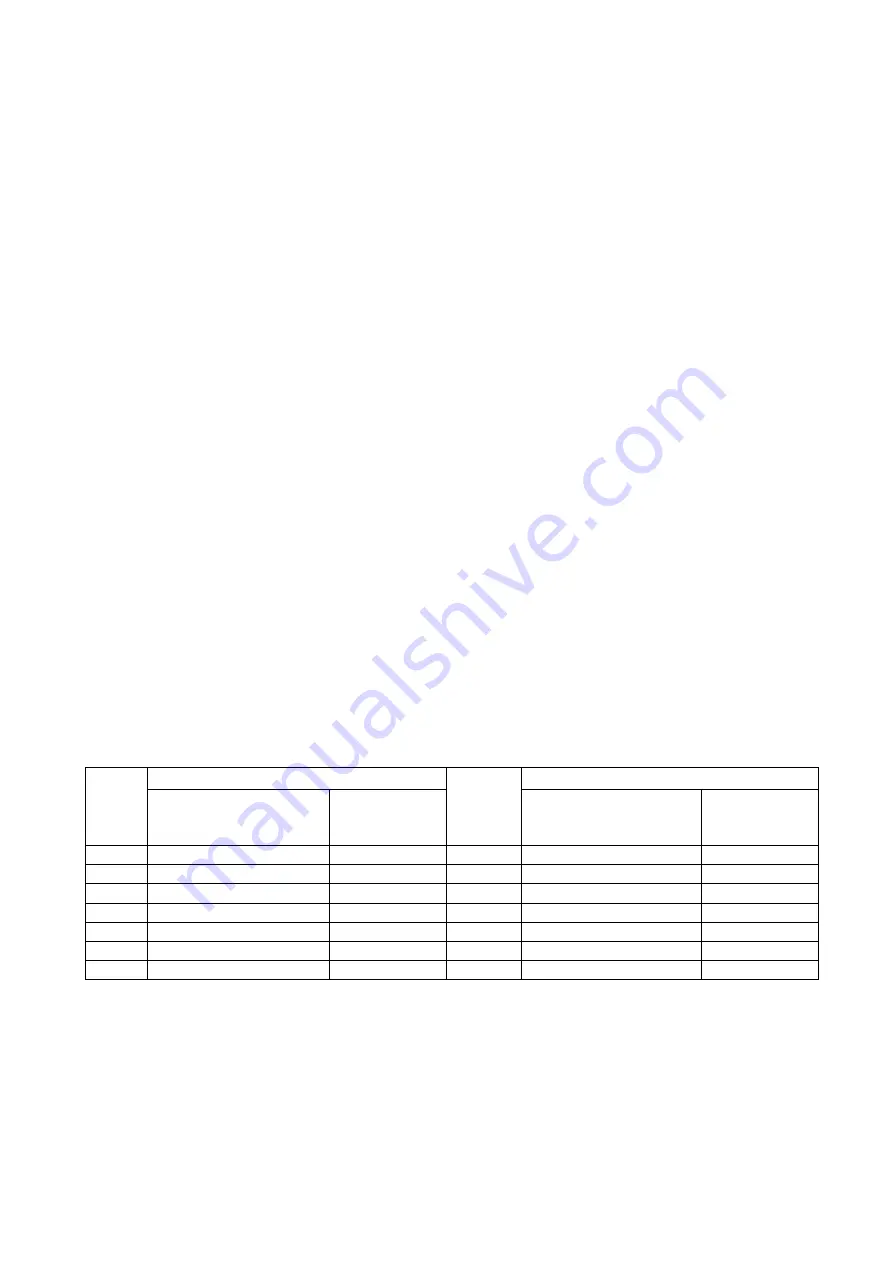
24
5. MOTORS SERIES 5 AND 7AT (ATP, ATPV, ABT, ABTP, ABTPV, ATL, ABTL), EXPLOSION
PROTECTED WITH TYPE OF PROTECTION “EXPLOSION-PROOF-d” and PROTECTION BY
ENCLOSURES“t”
For these motor series, together with these instructions, the “manufacturer‘s declaration” is also
issued as a proof that control and testing were performed and that motors are manufactured
according to the certified documentation:
-motors must be installed and used in accordance with adequate regulations for explosion protection
regarding the dangerous zones classification, areas of use and explosive groups of inflammable
materials or in accordance with the motor nameplate and ex-protection nameplate data. Motors with
Ex-protection “d/db” can be supplied via static frequency converter in conditions according to IEC
60034-25. In such cases motors must have built-in thermal-protection in stator winding. For these
motors along with the “Manufacturer’s statement”, “Appendix to the Manufacturer’s statement” is also
issued, defining regulation range and required torque/power reduction depending on the operating
conditions. In case of uncertainties, contact the manufacturer.
Connections must be made using cable entries, which comply with applicable standards. The cable
entry must be made without modifying the specific characteristics of the protection type as indicated in
the IEC 60079-1 standard for “d” motors (flameproof protection) and the IEC 60079-7 standard for Ex
d e motors (increased safety protection).
When the cable entry is made using a cable gland, the type of cable gland must be selected correctly
in relation to the type of plant and the type of cable. The cable gland must be tightened fully until the
seal rings ensure the necessary pressure:
- to prevent transmission of mechanical stress to the motor terminals
- to ensure the mechanical protection (degree) of the terminal box.
Cable entries for Ex d terminal boxes must consist of Ex d cable glands certified according to the IEC
60079-0, IEC 60079-1 Standards and the EX Directive (2014/34/EU). Furthermore, they must have a
minimum of IP55 protection class. For Ex db eb terminal boxes, Ex e cable glands certified according
to EX generation IEC 60079-0 and IEC 60079-7 standards must be used. Furthermore, they must
have a minimum of IP55 protection class.
Overload protection in the control box (on installations), should be adjusted according to the HRN
IEC 60079-14 norm,
All motors must be equipped with appropriate cable glands in accordance with requirements of
corresponding norms. For cable gland with cylindrical threading, protection against unfastening is
achieved by nut on the inside of the housing, (counter-nut), or appropriate filling (i.e. LOCTITE
243). Motors are shipped form the factory without the filling, and responsibility for securing the
gland against unfastening, lays on authorized personnel when installing the motor.
Cable entry is designed with Mxx x1,5 cable glands like in table:
IEC
motor
size
Series 5AT / 7AT
IEC
motor
size
Series 5AT / 7AT
Number of glands x
gland size
Diametar of
cabele
M
mm)
Number of glands x
gland size
Diametar of
cabele
M(mm)
160
1 x M32x1,5 + plug
18 - 25
71
1 x M20x1,5
6 – 12
180
1 x M40x1,5 + plug
22 - 32
80
1 x M20x1,5
6 – 12
200
2 x M40x1,5
22 - 32
90
1 x M20x1,5
6 – 12
225
2 x M50x1,5
29 - 38
100
1 x M25x1,5
13 – 18
250
2 x M50x1,5
29 - 38
112
1 x M25x1,5
13 – 18
280
2 x M50x1,5
29 - 38
132
1 x M32x1,5 + plug
18 – 25
315
2 x M63x1,5
34 - 44
In case the motor is equiped with heaters or thermal protection, the connection box is equipped with
the M20x1.5 cable glands. The special version of the connection box with different screwed- threads
is listed on the name plate on the terminal box.
On motors delivered with threaded holes for attaching cable glands and thread protecting closed
plastic plugs manufactured according to regulations, an authorized contractor is obliged to install
certified cable glands into these holes or, if there are any extra holes, close them with certified
plugs according to regulations. In addition, while performing connecting; the motors have to be
connected with isolated terminals.
In case of assembly and disassembly of motors, existing mechanical protection has to be provided
(use of sealing agents on contact surfaces, coating of screw joints with fillers, grease fulfilments in
bearings, greasing of shaft seals...)