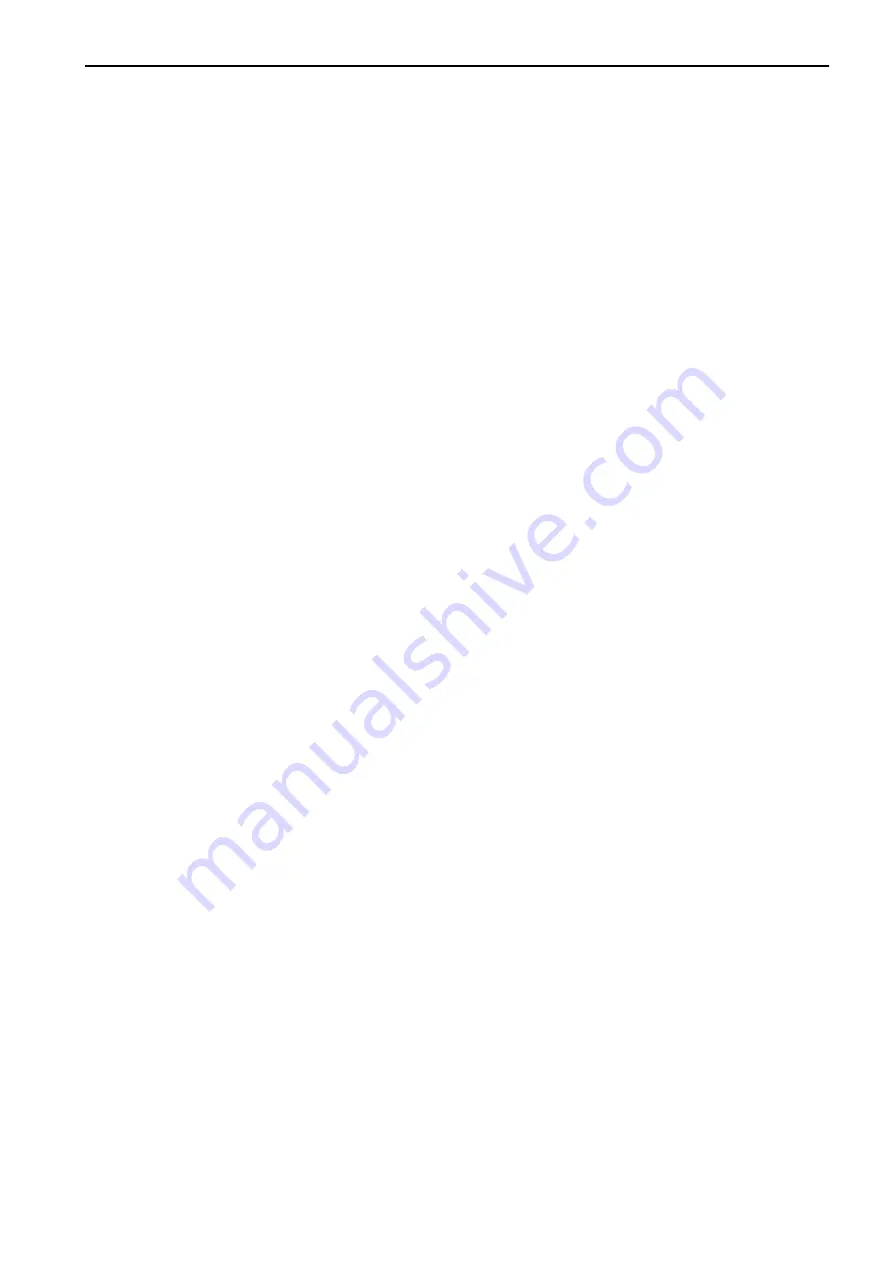
TABLE OF CONTENTS
FOREWORD.................................................................................................................................................... 1-1
READ THIS MANUAL ............................................................................................................................... 1-2
SAFETY INFORMATION .......................................................................................................................... 1-3
INTRODUCTION ...................................................................................................................................... 1-4
MAIN USE OF MACHINE .................................................................................................................. 1-4
DIRECTIONS OF MACHINE.............................................................................................................. 1-4
PROTECTIVE STRUCTURES........................................................................................................... 1-4
PRODUCT INFORMATION....................................................................................................................... 1-5
LOCATION OF PRODUCT IDENTIFICATION NUMBER (PIN)/MACHINE SERIAL NO. PLATE ........ 1-5
LOCATION OF ENGINE NUMBER PLATE ........................................................................................ 1-5
SERVICE METER LOCATION ........................................................................................................... 1-6
YOUR MACHINE SERIAL NUMBERS AND DISTRIBUTOR.............................................................. 1-6
SAFETY........................................................................................................................................................... 2-1
SAFETY LABELS ..................................................................................................................................... 2-2
LOCATION OF SAFETY LABELS...................................................................................................... 2-3
CONTENTS OF SAFETY LABELS .................................................................................................... 2-6
GENERAL PRECAUTIONS COMMON TO OPERATION AND MAINTENANCE .................................... 2-13
PRECAUTIONS BEFORE STARTING OPERATION........................................................................ 2-13
PREPARATIONS FOR SAFE OPERATION ..................................................................................... 2-14
PRECAUTIONS TO PREVENT FIRE............................................................................................... 2-16
PRECAUTIONS WHEN GETTING ON OR OFF MACHINE............................................................. 2-18
DO NOT GET CAUGHT IN WORK EQUIPMENT ............................................................................ 2-19
PRECAUTIONS RELATED TO PROTECTIVE STRUCTURES........................................................ 2-20
PROTECTION AGAINST FALLING, FLYING OR INTRUDING OBJECTS....................................... 2-21
UNAUTHORIZED MODIFICATION .................................................................................................. 2-21
PRECAUTIONS RELATED TO ATTACHMENTS AND OPTIONS .................................................... 2-21
PRECAUTIONS RELATED TO CAB GLASS ................................................................................... 2-21
PRECAUTIONS WHEN RUNNING ENGINE INSIDE BUILDING ..................................................... 2-22
PRECAUTIONS FOR OPERATION ........................................................................................................ 2-23
PRECAUTIONS FOR JOBSITE ....................................................................................................... 2-23
START ENGINE............................................................................................................................... 2-26
PRECAUTIONS FOR OPERATION ................................................................................................. 2-28
PRECAUTIONS FOR TRANSPORTATION...................................................................................... 2-36
TOWING AND BEING TOWED........................................................................................................ 2-37
LIFTING OPERATION BY USING BUCKET WITH HOOK ............................................................... 2-38
PRECAUTIONS FOR MAINTENANCE ................................................................................................... 2-39
PRECAUTIONS BEFORE STARTING INSPECTION AND MAINTENANCE ................................... 2-39
PRECAUTIONS FOR CHECK AND MAINTENANCE ...................................................................... 2-43
OPERATION .................................................................................................................................................... 3-1
GENERAL VIEW....................................................................................................................................... 3-2
MACHINE EQUIPMENT NAME ......................................................................................................... 3-2
CONTROLS AND GAUGES NAMES................................................................................................. 3-4
OTHER EQUIPMENT NAME ............................................................................................................. 3-7
EXPLANATION OF COMPONENTS ......................................................................................................... 3-9
EXPLANATION OF MACHINE MONITOR EQUIPMENT ................................................................... 3-9
SWITCHES...................................................................................................................................... 3-77
CONTROL LEVERS AND PEDALS ................................................................................................. 3-86
OTHER EQUIPMENT ...................................................................................................................... 3-94
MACHINE OPERATIONS AND CONTROLS ........................................................................................ 3-131
CHECKS AND ADJUSTMENT BEFORE STARTING ENGINE ...................................................... 3-131
METHOD FOR STARTING ENGINE.............................................................................................. 3-158
METHOD FOR OPERATIONS AND CHECKS AFTER STARTING ENGINE ................................. 3-161
METHOD FOR STOPPING ENGINE ............................................................................................. 3-169
METHOD FOR STARTING MACHINE (TRAVEL FORWARD AND REVERSE) AND STOPPING MA-
CHINE ........................................................................................................................................ 3-170
FOREWORD
TABLE OF CONTENTS
1-7
Summary of Contents for PC45MR-30403
Page 61: ......
Page 64: ...14 Engine rear cover 15 Cooling cover 16 Battery 17 KDPF OPERATION GENERAL VIEW 3 3...
Page 411: ......
Page 412: ...SPECIFICATIONS 5 1...
Page 417: ......
Page 459: ......
Page 460: ...REPLACEMENT PARTS 7 1...