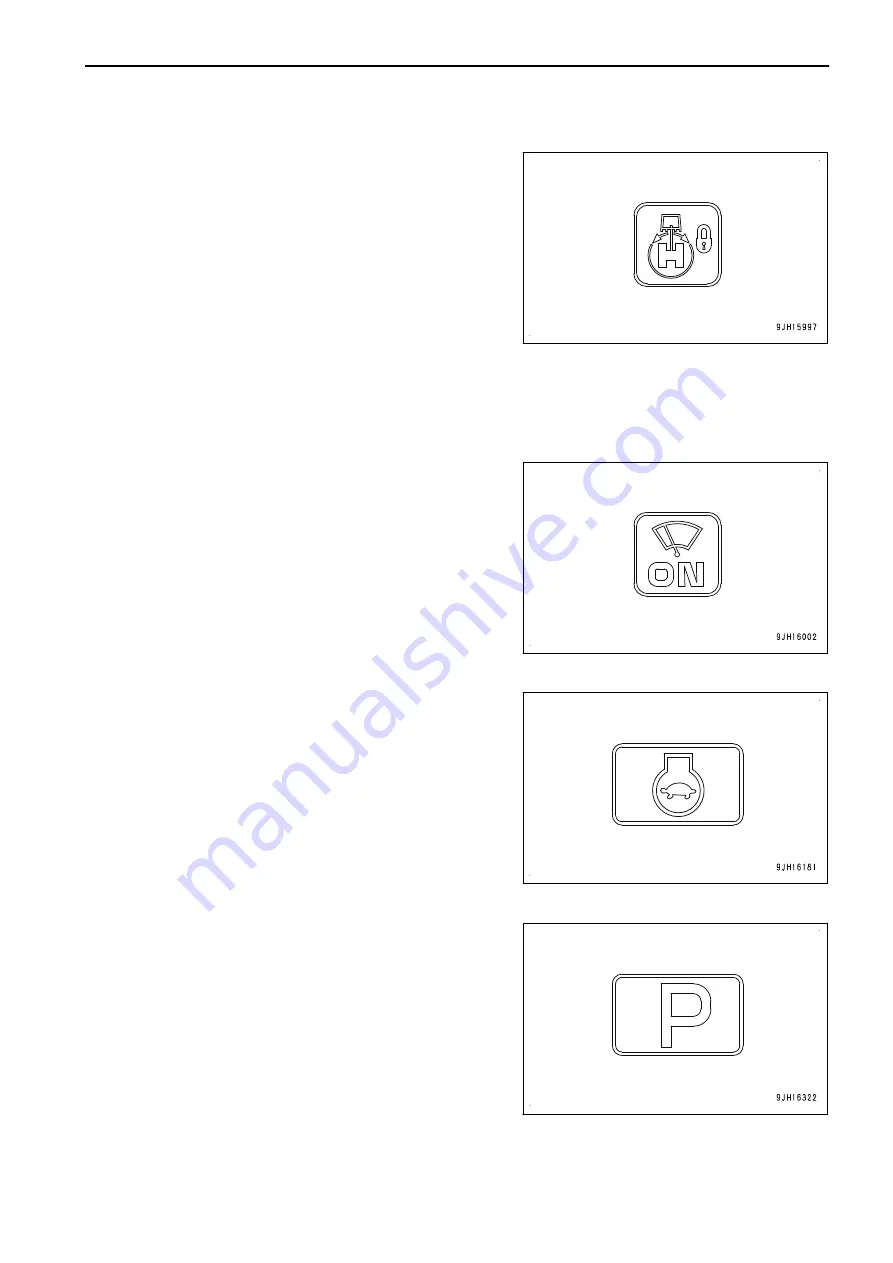
SWING LOCK PILOT LAMP
Swing lock pilot lamp informs that the swing lock is being actu-
ated.
Lights up: The swing lock is being actuated.
When the swing lock switch is turned ON (LOCK), this lamp
lights up.
When the swing parking brake cancel switch is turned to “Can-
cel”position, this lamp flashes.
For the positions of the swing lock switch and swing parking
brake cancel switch, see “CONTROLS AND GAUGES NAMES
(3-5)”.
REMARK
The swing motor is equipped with a disc brake that mechanically stops the rotation. When the swing lock pilot
lamp is lit, the brake remains applied.
WIPER PILOT LAMP
The wiper pilot lamp shows the operating state of the wind-
shield wiper.
The operation of the wiper switch is indicated by the pilot lamp
as follows.
When ON lights up: Windshield wiper operates continuously
When INT lights up: Windshield wiper operates intermittently
When nothing lights up: Wiper stops
For the position of the windshield wiper switch, see “MACHINE
MONITOR EQUIPMENT NAME”.
AUTO-DECELERATION PILOT LAMP
The auto-deceleration pilot lamp shows the setting of the auto-
deceleration either ON or OFF.
The pilot lamp display when the auto-deceleration switch is op-
erated is as follows.
Auto-deceleration pilot lamp lights up: Auto-deceleration ON
Auto-deceleration pilot lamp goes out: Auto-deceleration OFF
For the position of the auto-deceleration switch, see “MA-
CHINE MONITOR EQUIPMENT NAME”.
WORKING MODE DISPLAY
The working mode display shows the setting of the working
mode.
The working mode set with the working mode selector switch is
shown as follows.
P: P mode (for heavy-load operations)
E: E mode (for operations with emphasis on fuel consumption)
L: L mode (for fine control operations and lifting operations)
B: B mode ( for breaker operations) (For machines ready for in-
stallation of attachments)
ATT/P: ATT/P mode (for operations of 2-way attachments like
crusher, etc.)
OPERATION
EXPLANATION OF COMPONENTS
3-33
Summary of Contents for PC210-11
Page 2: ......
Page 24: ......
Page 74: ......
Page 352: ......
Page 431: ...SPECIFICATIONS 5 1 ...
Page 435: ...PC210LC 11 PC210NLC 11 SPECIFICATIONS SPECIFICATIONS 5 5 ...
Page 436: ...PC230NHD 11 SPECIFICATIONS SPECIFICATIONS 5 6 ...
Page 459: ...PC230NHD 11 2 Piece Boom ATTACHMENTS AND OPTIONS 2 PIECE BOOM 6 23 ...
Page 470: ... Not including tail swing SUPER LONG FRONT BOOM AND ARM ATTACHMENTS AND OPTIONS 6 34 ...
Page 505: ...REPLACEMENT PARTS 7 1 ...
Page 521: ......