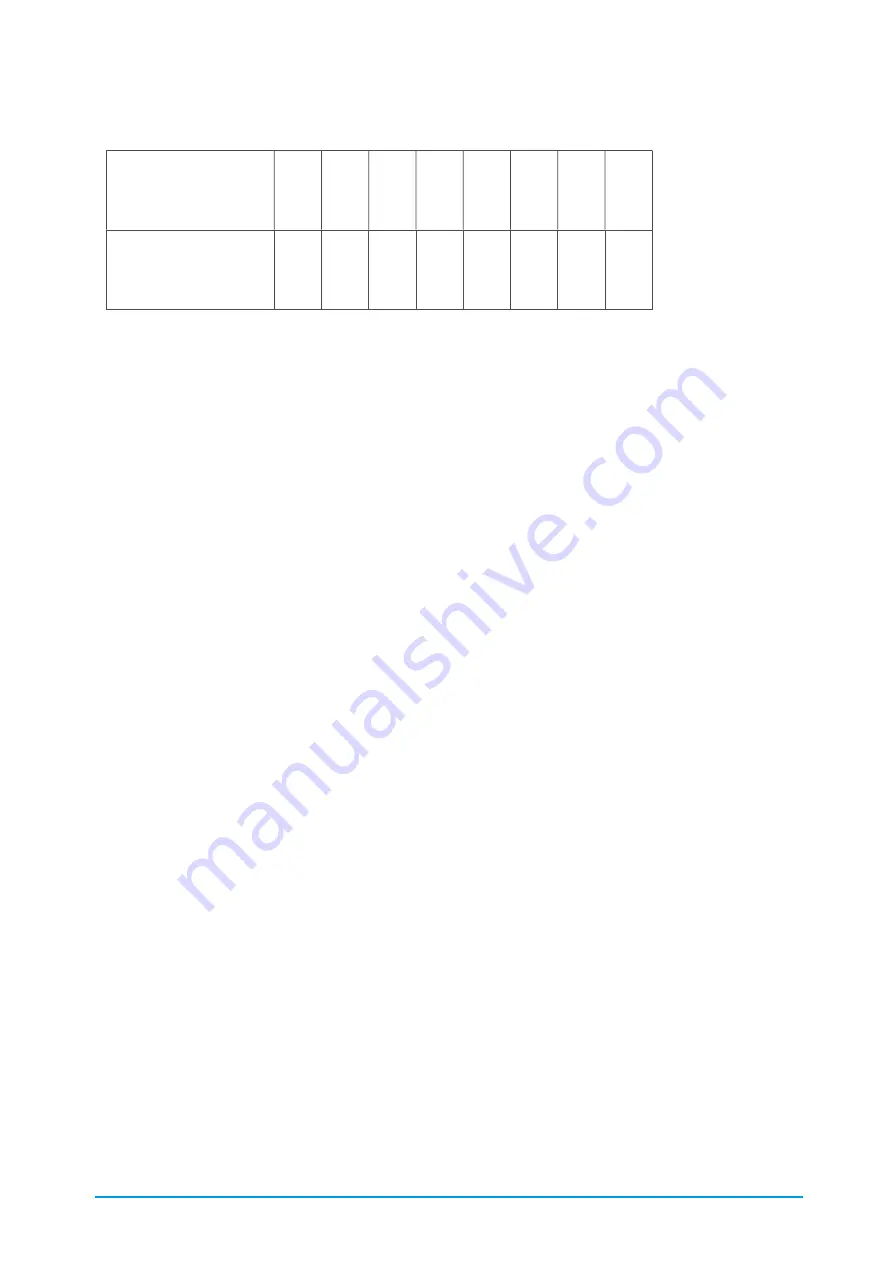
46 / 97
83000102.Ko
Table 11: Minimum volume of the installation room with regard to maximum refrigerant concentration in
case of a leakage if installed indoors
cBoxX chiller
40
60
70
80 100 120 160 180
Minimum volume of the
installation room (in m³)
14
16
20
20
20
40
40
55
6.2.3.
Ambient temperature
The chiller is cooled by the ambient air and the lower the temperature of this cooling air the more
economically the chiller works. Direct sunshine or exhaust air from other machines heats up the surrounding
air and must be taken into account when installing the chiller. Preference is for a shaded installation. The
maximum ambient temperature is given in the technical data.
At ambient temperatures < -25 °C install pipe trace heating (on site by customer).
To prevent frost damage, never switch off or disconnect the chiller from the power supply at ambient
temperatures < -25°C. If necessary, set the chiller to standby mode.
6.2.4.
Effect of surrounding air flow
The chiller emits heat to the surrounding area, the machine also draws in cooling air. The machine controls
the quantity of cooling air automatically via the speed of the fan. Air currents surrounding the machine, such
as the wind, can affect this control and endanger operation of the machine. If a constant direction of an air
current is known at the installation site, this should not be directed at the air intake side of the chiller.
6.2.5.
Minimum clearances
The minimum clearances around the machine are made up of service clearances and clearances to ensure
optimum air supply. On the one hand accessibility must be ensured from all sides, in addition, an
unhindered, sufficient quantity of cooling air must be able to be drawn in and blown out upwards. If the
minimum clearances are not complied with there is a risk of an air short-circuit between the air intake and
discharge side
.