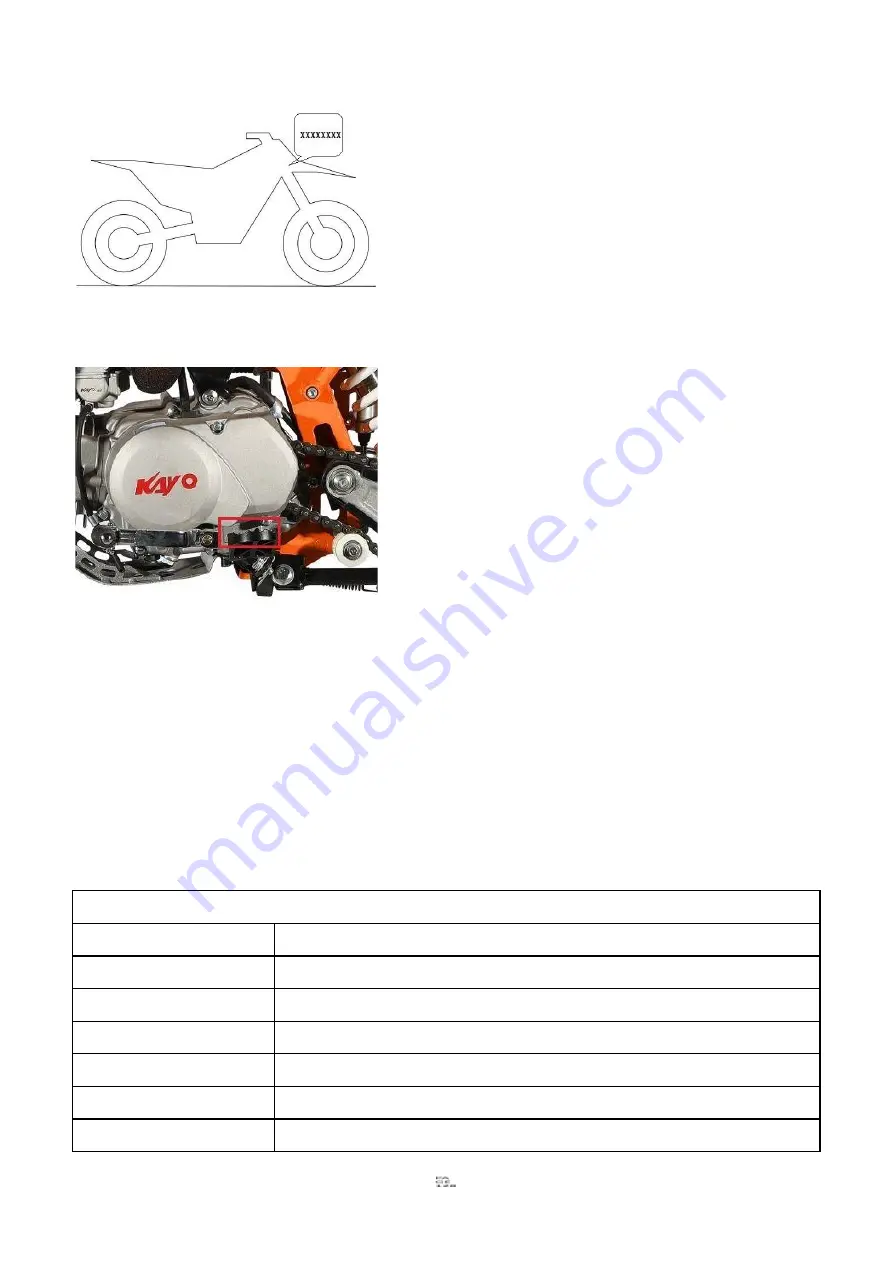
VIN Number of 21 TD125 is carved on the frame of head pipe.
Engine Number
Engine Number of 21 TD125 is carved on the engine crankcase
body behind gear lever.
Specification
TD125 size and quality parameters
Length*Width*Height (mm)
1600*750*990
Wheelbase (mm)
1125
Weight (kg)
65
Tyre size
Front 60/100-14; Rear 80/100-12
Seat height (mm)
750
Ground clearance (mm)
265
Fuel tank capacity (L)
3.5
Summary of Contents for TD125
Page 1: ...KAYO MOTO TD125 SERVICE MANUAL www kayomoto com...
Page 24: ...h e c k t h e c a r b u r e t o r i d l e s p e e d R e p l a c e t h e a i r lt e r C h e c...
Page 28: ...i n g s f o r c r a c k s l e a k s a n d i n c o r r e c t w i r i n g C h e c k c l u t c h...
Page 32: ...h a i n s h a n d l e s e t c a n d c h e c k f o r s m o o t h o p e r a o n C h e c k c h a...
Page 34: ...c h a i n g u i d e a n d c h a i n c o v e r C h e c k s p o k e t e n s i o n C h e c k t...
Page 35: ...h e r i m C h e c k f o r r i m e d g e r u n o u t C h e c k if t h e r i m b e a r i n g i s...
Page 40: ...s y s t e m s e t u p C h e c k t h e c o m p r e s s i o n a n d r e b o u n d o f t h e...