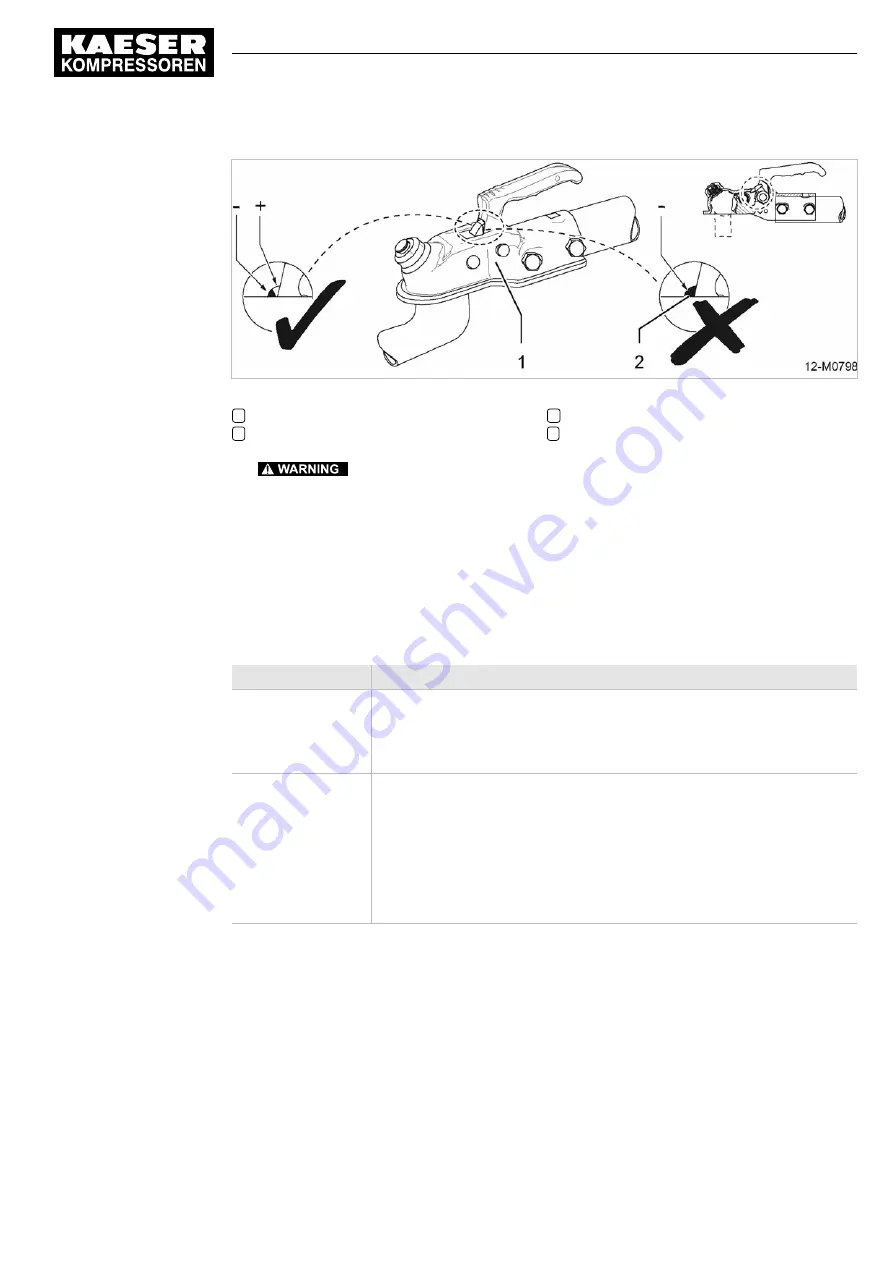
Fig. 95 Wear alert, ball coupling (ALKO-EU)
1
Ball coupling
2
Wear indicator
+
Green zone (OK)
–
Red zone (wear tolerance exceeded)
1.
Danger of accident from worn coupling!
The machine may detach from the towing vehicle.
➤ Do not tow the machine.
➤ Have the ball coupling and ball hitch checked.
➤ Replace worn parts.
2. Couple-up the machine and tow slowly and carefully for about 0.5 miles.
The action of towing sets the coupling mechanism to maximum closure and gives a true read‐
ing on the wear indicator.
3. Interpret the wear indicator as follows:
Wear indicator
Meaning
Green zone showing ■ Coupling in new condition.
■ Towing vehicle ball hitch wear within acceptable limits.
➤ No action necessary.
Red zone showing
■ Ball hitch wear at acceptable limit, ball coupling unworn.
■ Ball hitch in new condition; ball coupling showing increased wear.
■ Both ball and coupling showing increased wear.
■ Ball coupling damaged.
➤ Have the ball coupling and ball hitch checked by a specialist workshop.
➤ Replace worn parts.
Tab. 98 Ball coupling wear indicator
Coupling machine with ball coupling (US version):
To couple up the compressor, lower the open coupling onto the ball hitch of the towing vehicle so
that it clicks into place.
12 Decommissioning, Storage and Transport
12.2 Transport
No.: 9_6999 23 USE
Operator Manual Screw Compressor
M100
233
Option rd/ro/rs
Summary of Contents for M100
Page 2: ...Original instructions KKW M100 2 03 en Z1 SBA MOBILAIR 20150112 161243...
Page 8: ...Contents vi Operator Manual Screw Compressor M100 No 9_6999 23 USE...
Page 276: ...13 Annex 13 4 Wiring diagrams 264 Operator Manual Screw Compressor M100 No 9_6999 23 USE...
Page 277: ...13 Annex 13 4 Wiring diagrams No 9_6999 23 USE Operator Manual Screw Compressor M100 265...
Page 278: ...13 Annex 13 4 Wiring diagrams 266 Operator Manual Screw Compressor M100 No 9_6999 23 USE...
Page 279: ...13 Annex 13 4 Wiring diagrams No 9_6999 23 USE Operator Manual Screw Compressor M100 267...
Page 280: ...13 Annex 13 4 Wiring diagrams 268 Operator Manual Screw Compressor M100 No 9_6999 23 USE...
Page 281: ...13 Annex 13 4 Wiring diagrams No 9_6999 23 USE Operator Manual Screw Compressor M100 269...
Page 282: ...13 Annex 13 4 Wiring diagrams 270 Operator Manual Screw Compressor M100 No 9_6999 23 USE...
Page 283: ...13 Annex 13 4 Wiring diagrams No 9_6999 23 USE Operator Manual Screw Compressor M100 271...
Page 284: ...13 Annex 13 4 Wiring diagrams 272 Operator Manual Screw Compressor M100 No 9_6999 23 USE...
Page 285: ...13 Annex 13 4 Wiring diagrams No 9_6999 23 USE Operator Manual Screw Compressor M100 273...
Page 286: ...13 Annex 13 4 Wiring diagrams 274 Operator Manual Screw Compressor M100 No 9_6999 23 USE...
Page 287: ...13 Annex 13 4 Wiring diagrams No 9_6999 23 USE Operator Manual Screw Compressor M100 275...
Page 288: ...13 Annex 13 4 Wiring diagrams 276 Operator Manual Screw Compressor M100 No 9_6999 23 USE...
Page 290: ...13 Annex 13 4 Wiring diagrams 278 Operator Manual Screw Compressor M100 No 9_6999 23 USE...
Page 291: ...13 Annex 13 4 Wiring diagrams No 9_6999 23 USE Operator Manual Screw Compressor M100 279...
Page 292: ...13 Annex 13 4 Wiring diagrams 280 Operator Manual Screw Compressor M100 No 9_6999 23 USE...
Page 293: ...13 Annex 13 4 Wiring diagrams No 9_6999 23 USE Operator Manual Screw Compressor M100 281...
Page 294: ...13 Annex 13 4 Wiring diagrams 282 Operator Manual Screw Compressor M100 No 9_6999 23 USE...
Page 295: ...13 Annex 13 4 Wiring diagrams No 9_6999 23 USE Operator Manual Screw Compressor M100 283...
Page 296: ...13 Annex 13 4 Wiring diagrams 284 Operator Manual Screw Compressor M100 No 9_6999 23 USE...
Page 298: ...13 Annex 13 4 Wiring diagrams 286 Operator Manual Screw Compressor M100 No 9_6999 23 USE...
Page 299: ...13 Annex 13 4 Wiring diagrams No 9_6999 23 USE Operator Manual Screw Compressor M100 287...
Page 300: ...13 Annex 13 4 Wiring diagrams 288 Operator Manual Screw Compressor M100 No 9_6999 23 USE...
Page 301: ...13 Annex 13 4 Wiring diagrams No 9_6999 23 USE Operator Manual Screw Compressor M100 289...
Page 303: ...13 Annex 13 4 Wiring diagrams No 9_6999 23 USE Operator Manual Screw Compressor M100 291...
Page 304: ...13 Annex 13 4 Wiring diagrams 292 Operator Manual Screw Compressor M100 No 9_6999 23 USE...
Page 305: ...13 Annex 13 4 Wiring diagrams No 9_6999 23 USE Operator Manual Screw Compressor M100 293...
Page 306: ...13 Annex 13 4 Wiring diagrams 294 Operator Manual Screw Compressor M100 No 9_6999 23 USE...
Page 307: ...13 Annex 13 4 Wiring diagrams No 9_6999 23 USE Operator Manual Screw Compressor M100 295...
Page 308: ...13 Annex 13 4 Wiring diagrams 296 Operator Manual Screw Compressor M100 No 9_6999 23 USE...
Page 309: ...13 Annex 13 4 Wiring diagrams No 9_6999 23 USE Operator Manual Screw Compressor M100 297...
Page 310: ...13 Annex 13 4 Wiring diagrams 298 Operator Manual Screw Compressor M100 No 9_6999 23 USE...
Page 312: ...13 Annex 13 4 Wiring diagrams 300 Operator Manual Screw Compressor M100 No 9_6999 23 USE...
Page 313: ...13 Annex 13 4 Wiring diagrams No 9_6999 23 USE Operator Manual Screw Compressor M100 301...
Page 314: ...13 Annex 13 4 Wiring diagrams 302 Operator Manual Screw Compressor M100 No 9_6999 23 USE...
Page 315: ...13 Annex 13 4 Wiring diagrams No 9_6999 23 USE Operator Manual Screw Compressor M100 303...
Page 316: ...13 Annex 13 4 Wiring diagrams 304 Operator Manual Screw Compressor M100 No 9_6999 23 USE...
Page 317: ...13 Annex 13 4 Wiring diagrams No 9_6999 23 USE Operator Manual Screw Compressor M100 305...
Page 318: ...13 Annex 13 4 Wiring diagrams 306 Operator Manual Screw Compressor M100 No 9_6999 23 USE...
Page 319: ...13 Annex 13 4 Wiring diagrams No 9_6999 23 USE Operator Manual Screw Compressor M100 307...
Page 321: ...13 Annex 13 4 Wiring diagrams No 9_6999 23 USE Operator Manual Screw Compressor M100 309...
Page 322: ...13 Annex 13 4 Wiring diagrams 310 Operator Manual Screw Compressor M100 No 9_6999 23 USE...
Page 323: ...13 Annex 13 4 Wiring diagrams No 9_6999 23 USE Operator Manual Screw Compressor M100 311...
Page 324: ...13 Annex 13 4 Wiring diagrams 312 Operator Manual Screw Compressor M100 No 9_6999 23 USE...
Page 325: ...13 Annex 13 4 Wiring diagrams No 9_6999 23 USE Operator Manual Screw Compressor M100 313...
Page 326: ...13 Annex 13 4 Wiring diagrams 314 Operator Manual Screw Compressor M100 No 9_6999 23 USE...
Page 327: ...13 Annex 13 4 Wiring diagrams No 9_6999 23 USE Operator Manual Screw Compressor M100 315...
Page 328: ...13 Annex 13 4 Wiring diagrams 316 Operator Manual Screw Compressor M100 No 9_6999 23 USE...
Page 330: ...13 Annex 13 4 Wiring diagrams 318 Operator Manual Screw Compressor M100 No 9_6999 23 USE...
Page 331: ...13 Annex 13 4 Wiring diagrams No 9_6999 23 USE Operator Manual Screw Compressor M100 319...
Page 332: ...13 Annex 13 4 Wiring diagrams 320 Operator Manual Screw Compressor M100 No 9_6999 23 USE...
Page 333: ...13 Annex 13 4 Wiring diagrams No 9_6999 23 USE Operator Manual Screw Compressor M100 321...
Page 334: ...13 Annex 13 4 Wiring diagrams 322 Operator Manual Screw Compressor M100 No 9_6999 23 USE...
Page 335: ...13 Annex 13 4 Wiring diagrams No 9_6999 23 USE Operator Manual Screw Compressor M100 323...
Page 336: ...13 Annex 13 4 Wiring diagrams 324 Operator Manual Screw Compressor M100 No 9_6999 23 USE...
Page 337: ...13 Annex 13 4 Wiring diagrams No 9_6999 23 USE Operator Manual Screw Compressor M100 325...