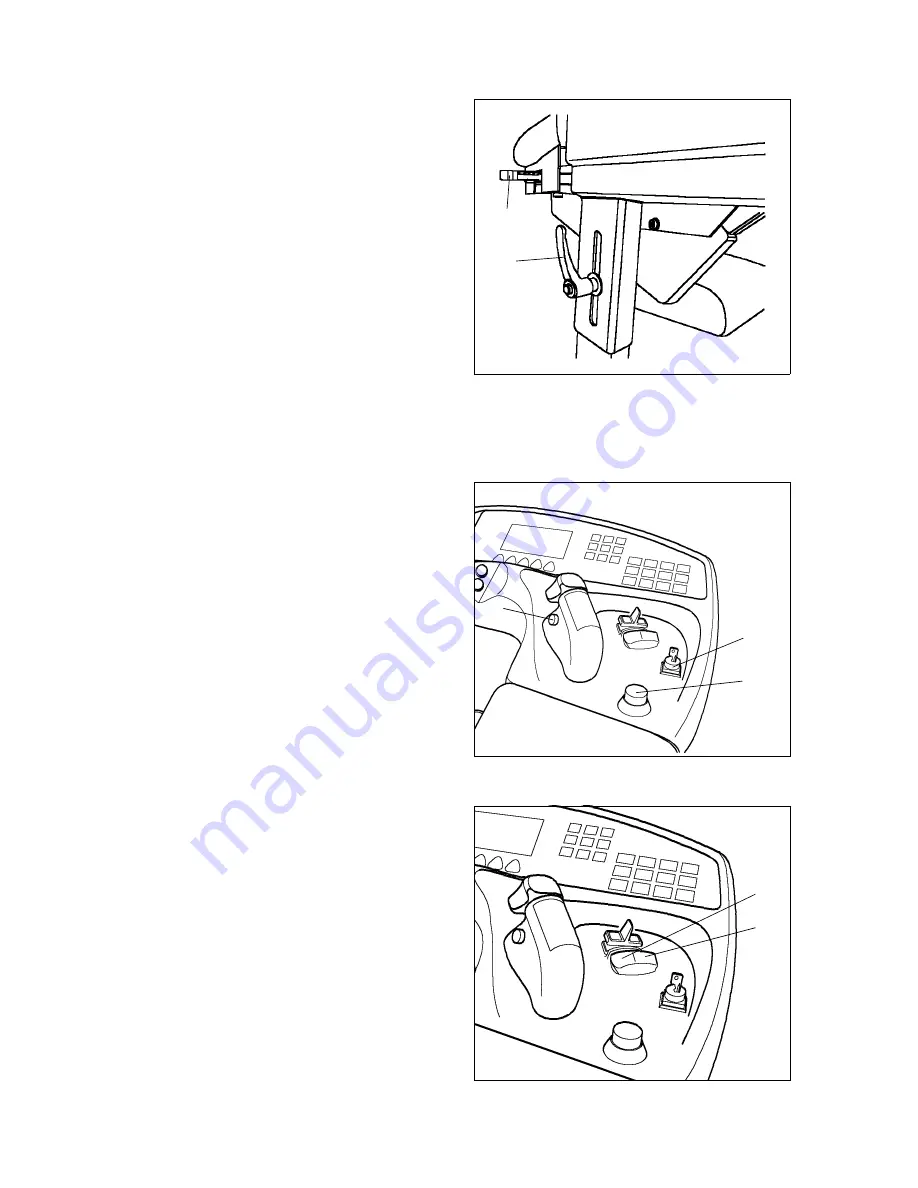
501
1
838
6 GB
E 22
3.6
Adjusting the operating panel
The operating panel can be adjusted in
height and laterally.
Height adjustment:
– Simultaneously grip operating panel
and release lever (1).
– Adjust operating panel to correct
height and retighten lever.
Lateral adjustment:
– Pull lever (2) upward.
– Adjust operating panel to correct
position.
– Allow lever to latch again.
3.7
Providing operational readiness
– Turn and release EMERGENCY OFF
(6).
– Insert key into key switch (5) and turn
clockwise.
– Check proper function of warning
facility (horn) (7).
– Check proper function of service
brake and immobilising brake.
– Perform reference drive of lifting mast
for height indicator adjustment.
f
If any undesired travel or lifting motion
occurs, immediately actuate
EMERGENCY OFF switch.
3.8
Driver position adjustment
Driver seat with operating panel and
pedals can be continuously rotated
approx. 30° in load direction and approx.
10° in drive direction by push of a button.
– Setting toggle switch to position 3:
Driver position rotates to the right
– Set toggle switch to position 4: Driver
position rotates to the left
1
2
5
6
7
3
4
501
1
838
6 GB
E 22
3.6
Adjusting the operating panel
The operating panel can be adjusted in
height and laterally.
Height adjustment:
– Simultaneously grip operating panel
and release lever (1).
– Adjust operating panel to correct
height and retighten lever.
Lateral adjustment:
– Pull lever (2) upward.
– Adjust operating panel to correct
position.
– Allow lever to latch again.
3.7
Providing operational readiness
– Turn and release EMERGENCY OFF
(6).
– Insert key into key switch (5) and turn
clockwise.
– Check proper function of warning
facility (horn) (7).
– Check proper function of service
brake and immobilising brake.
– Perform reference drive of lifting mast
for height indicator adjustment.
f
If any undesired travel or lifting motion
occurs, immediately actuate
EMERGENCY OFF switch.
3.8
Driver position adjustment
Driver seat with operating panel and
pedals can be continuously rotated
approx. 30° in load direction and approx.
10° in drive direction by push of a button.
– Setting toggle switch to position 3:
Driver position rotates to the right
– Set toggle switch to position 4: Driver
position rotates to the left
1
2
5
6
7
3
4
Summary of Contents for ETX ac 125
Page 1: ...Operating instructions 50118386 ETX ac 125 150 G 01 01 05 03...
Page 3: ...0108 GB...
Page 7: ...50118386 GB I 4...
Page 9: ...A 2 50118386 GB...
Page 16: ...B 7 50118386 GB...
Page 21: ...B 12 50118386 GB...
Page 25: ...C 4 50118386 GB...
Page 44: ...E 15 50118386 GB Display symbol assignment...
Page 45: ...50118386 GB E 16 Display symbol assignment Time of day Height display Operating hours...
Page 73: ...50118386 GB E 44...
Page 81: ...50118386 GB F 8 g Glide surfaces s Lubricator nipples...