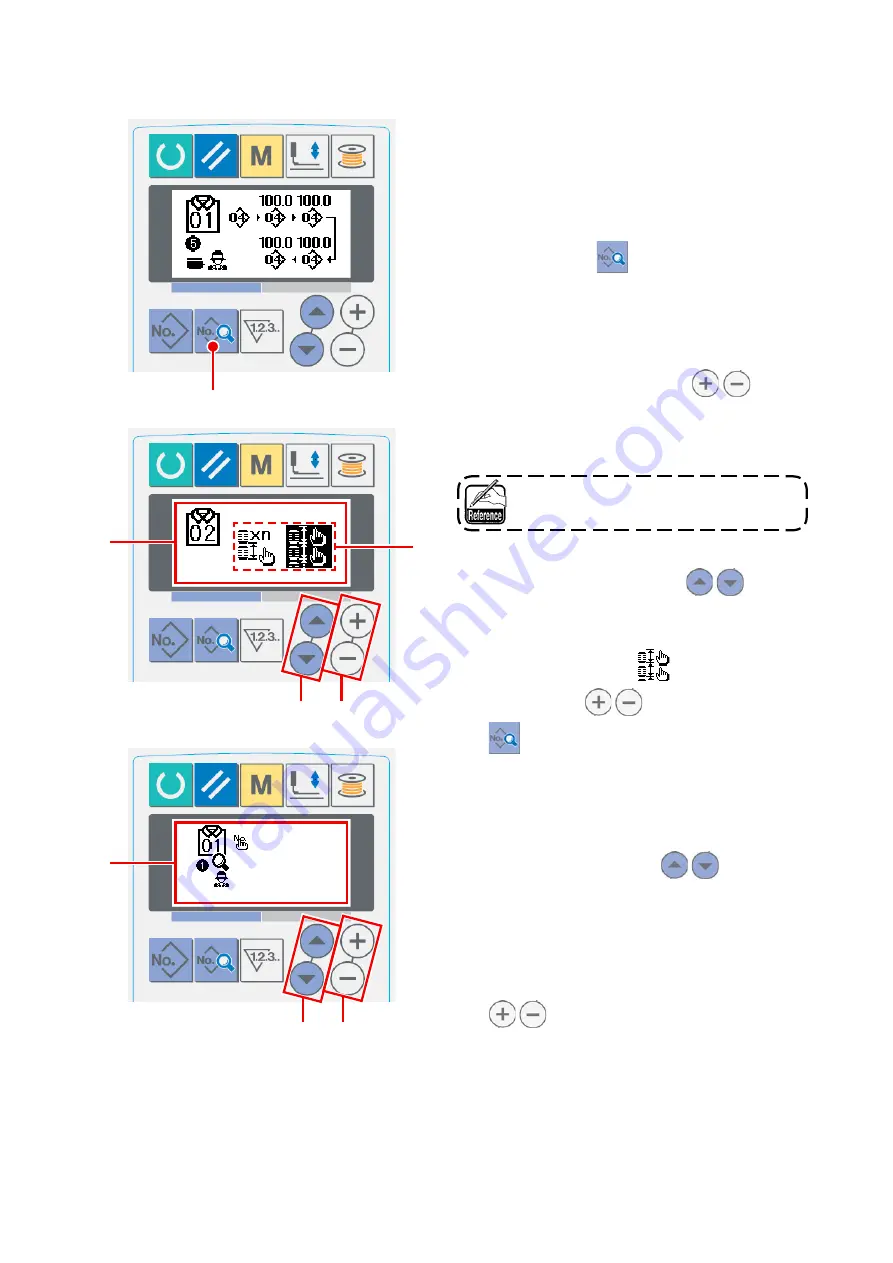
− 53 −
8
(2) Carrying out the individual input
A
C
!0
!1
!0
!1
B
1
Displaying the data input screen
New AC pattern can be regstered only on the
AC data nput screen (blue).
2
Calling the new AC pattern registration
screen
Keep DATA key
8
held pressed untl the
new pattern regstraton screen
A
s dsplayed.
3
Inputting a pattern number
Input a new AC pattern No. to be regstered by
means of DATA CHANGE key
!1
. It
s prohbted to regster a new AC pattern to the
AC pattern number whch has already been reg-
stered.
Twenty different patterns (1 to 20) can be
used as AC patterns.
4
Selecting the individual input
Press the ITEM SELECT key
!0
to
blnk the equal-nterval/ndvdual nput selecton
B
.
Select ndvdual nput
usng DATA
CHANGE key
!1
and press DATA key
8
. Then, the AC pattern number to be
newly registered is confirmed and individual
nput screen
C
s dsplayed.
5
Selecting the LBH sewing pattern number
Press ITEM SELECT key
!0
to blnk
the LBH sewng pattern number and the feed
amount to be changed.
The LBH sewng pattern number and the feed
amount data, which are flashing on and off, can
be changed by pressng DATA CHANGE key
!1
.