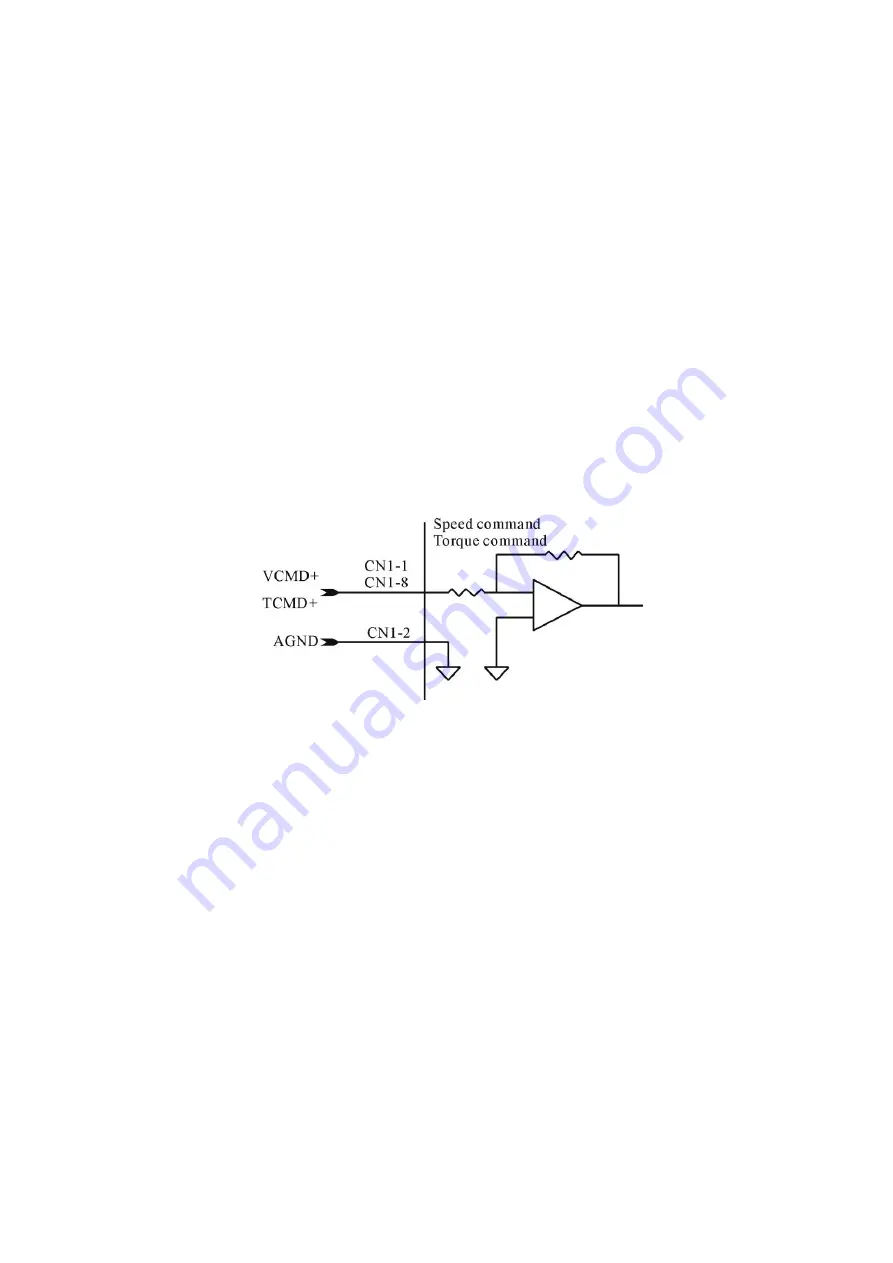
29
12.7
MDO Operation mode
If the CNTL parameter is set in the
“
Common Parameter
”
menu as S/P (speed/Position), P/T
(Position/Torque), or S/T (Speed/Torque) mode, this input signal enables the switching between operation
modes.
For example: If CNTL is set as S/P mode, when CN-34 and 24G is not connected, the servo drive is
in Speed operation mode, when connected; the servo drive is switched to Position operation mode.
12.8
VCMD+ and TCMD+ inputs (CN1-1 and CN1-8)
VCMD+: When the servo drive is in S Mode or is switched to S mode, this signal is used as analog
speed command input. The input voltage scale can be modified at the VMDL parameter contained in the
“
Speed Parameter
”
menu. The value of the VMDL parameter defines the input voltage which
corresponds to the rated speed, with positive voltage for forward rotation, and negative voltage for reverse
rotation.
TCMD+: When the servo drive is in T Mode or is switched to Torque operation mode, this signal is
used as analog torque command input. If the input voltage is 10V, the motor outputs 300% of the rated
torque.
Note: CN1-1 is for high-resolution analog signal input (12 BIT). Please purchase YPV-XXX-V series
servo drive if high-resolution analog input is needed. The input pin of the standard analog input
(resolution 10 BIT) is CN1-8.
Summary of Contents for YPV-040
Page 21: ...20 8 2 Encoder digital output interface circuit...
Page 22: ...21 9 Position control interface...
Page 23: ...22 10 Speed control interface...
Page 24: ...23 11 Torque control interface...
Page 63: ...62 15 12 Online Monitor Use Read button to read the under monitoring data and stop to exit...
Page 69: ...68 20 Wiring of MPC3024 wiring board to Mokon driver...