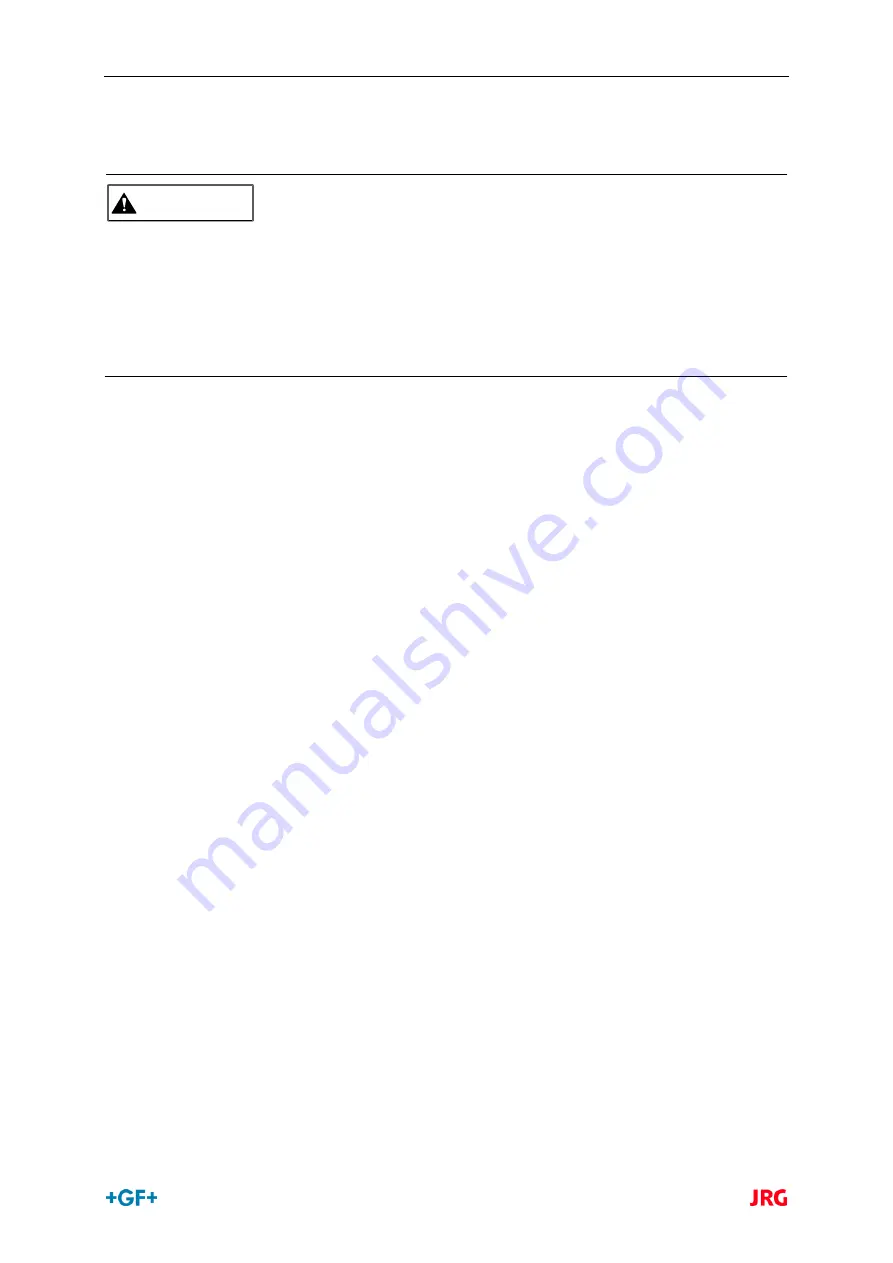
Removal
Operating instructions
78
14
Removal
Possible spillage of media harmful to health and the environment!
These media pose a risk of physical injury or damage to the environment.
Wear the prescribed protective clothing.
Collect any spilled media and dispose of according to the local regulations. Refer to the
safety data sheet.
The system must be stored salt-free and must not be emptied (the reactor must be stored
wet). See Chapter 10.5 “Decommissioning during prolonged periods of non-use
(downtime > 3 days)“ on page 55.
Empty the operating fluid tanks.
Disconnect the system from the power supply and secure it to prevent it from being
switched on again.
Dechlorinate and neutralize the chemicals and dispose of them according to the
applicable national disposal regulations.
Disassemble the system by following the assembly procedure in the reverse order.
Store the system. The ambient temperature must not fall below 5 °C.
CAUTION
Summary of Contents for 9800.002
Page 6: ...Operating instructions Intended Use...
Page 7: ......