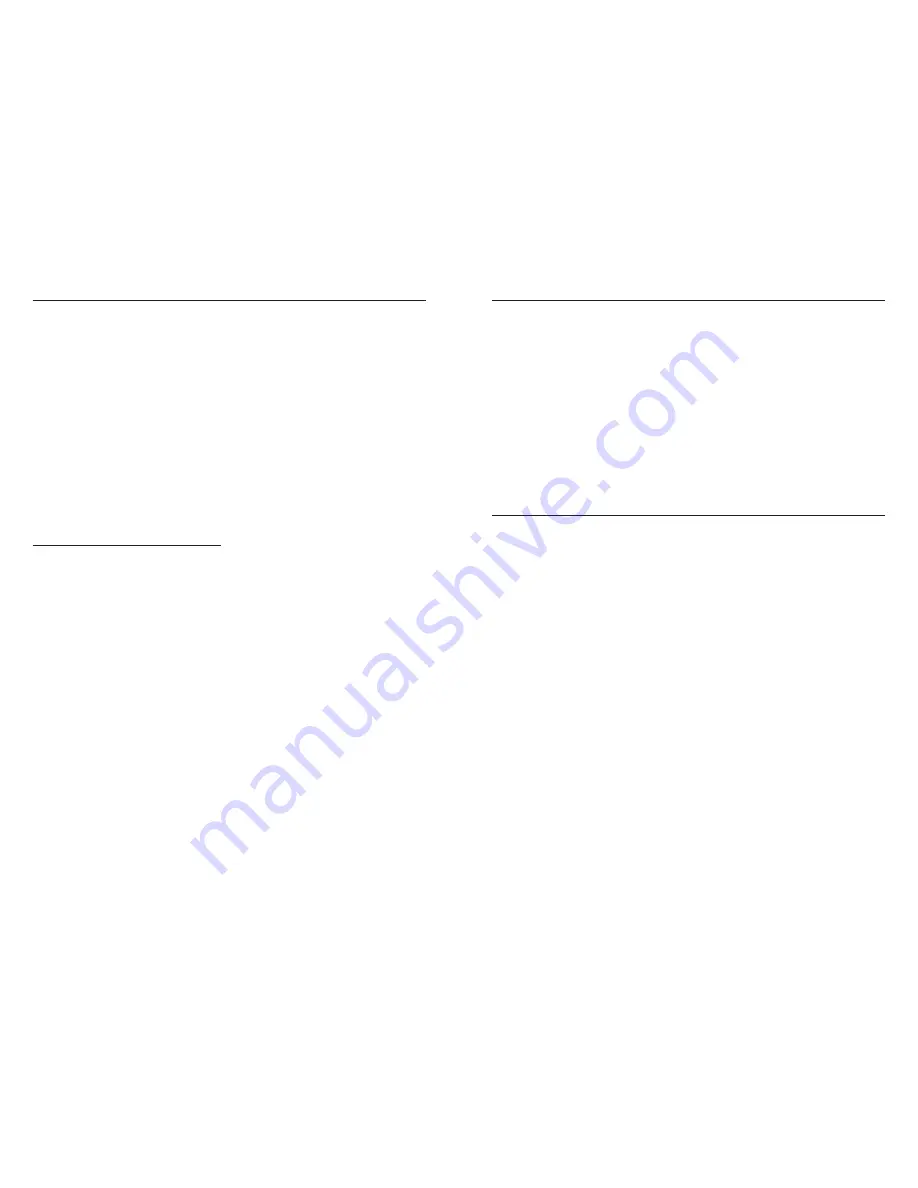
G-24
G-25
With all radio installations, the onboard power system
must provide adequate power without interruption to the
receiver even when the system is fully loaded (servos at
maximum flight loads). This becomes especially critical
with giant-scale models that utilize multiple high-torque/
high-current servos. Inadequate power systems that do
not provide the necessary minimum voltage to the receiver
during flight loads are the number one cause of in-flight
failures. Some of the power system components that affect
the ability to properly deliver adequate power include: the
selected receiver battery pack (number of cells, capacity,
cell type, state of charge), switch harness, battery leads,
regulator (if used), power bus (if used).
While the R921 receivers’ minimum operational voltage is
3.5-volts, you should test the system per the guidelines
below to a minimum acceptable voltage of 4.8-volts
during ground testing. This provides head room to
compensate for battery discharging or if the actual flight
loads are greater than the ground test loads.
Recommended Power System Guidelines
1. When setting up large or complex aircraft with multiple
high-torque servos, you should use a current and
voltmeter (Hangar 9 HAN172). Plug the voltmeter in an
open channel port in the receiver and with the system
on, load the control surfaces (apply pressure with your
hand) while monitoring the voltage at the receiver. The
voltage should remain above
4.8 volts even when all servos are heavily loaded.
Note
: The optional Flight Log has a built-in
voltmeter that can perform this test.
2. With the current meter inline with the receiver battery
lead, load the control surfaces (apply pressure
with your hand) while monitoring the current. The
maximum continuous recommended current for a
single heavy-duty servo/battery lead is three amps
while short duration current spikes of up to five amps
are acceptable. Consequently, if your system draws
more than three amps continuous or five amps for
short durations, a single battery pack with a single
switch harness plugged into the receiver for power is
inadequate. You should use multiple packs of the same
capacity with multiple switches and multiple leads
plugged into the receiver.
3. If using a regulator, it’s important that the above tests
are done for an extended period of 5 minutes. Currents
passing through a regulator generate heat, and this
heat causes the regulator to increase resistance, which
in turn causes even more heat to build up (thermal
runaway). While a regulator may provide adequate
power for a short duration, you should test its ability
over time as the regulator may not be able to maintain
voltage at significant power levels.
4. For really large aircraft or complex models (e.g. 35%
and larger or jets), multiple battery packs with multiple
switch harnesses are necessary. In many cases, one
of the commercially available power boxes/busses
is recommended. No matter what power system you
choose, always carry out test #1 above making sure the
receiver is constantly provided with 4.8 volts or more
under all conditions.
5. The latest generation of Nickel-Metal Hydride batteries
incorporate a new chemistry mandated to be more
environmentally friendly. These batteries, when
charged with peak detection fast chargers, have
tendencies to false peak (not fully charge) repeatedly.
These include all brands of Ni-MH batteries. If using
Ni-MH packs be especially cautious when charging,
make absolutely sure that the battery is fully
charged. You should use a charger that can display
total charge capacity. Note the number of mAh put into
a discharged pack to verify it has reached capacity.
Receiver Power System Requirements
All preprogrammed data is protected by a flash
memory that guards against memory loss .
Flash Memory
Battery Alarm and Display
When the transmitter voltage drops below 9.0-volts DC,
the display flashes “BATT LOW” and an alarm sounds.
If you are flying when this occurs, land immediately.
Tips on Using 2.4GHz Systems
While your DSM-equipped 2.4GHz system is intuitive to
operate, functioning nearly identically to 72MHz systems,
following are a few common questions from customers.
1. Q: Which do I turn on first, the transmitter or the
receiver?
A: If the receiver is turned on first, all servos except
for the throttle will be driven to their preset fail-safe
positions set during binding. At this time, the throttle
channel doesn’t put out a pulse position preventing
the arming of electronic speed controllers or, in the
case of an engine-powered aircraft, the throttle servo
remains in its current position. When the transmitter is
then turned on, the transmitter scans the 2.4GHz band
and acquires two open channels. Then the receiver that
was previously bound to the transmitter scans the band
and finds the GUID (Globally Unique Identifier code)
stored during binding. The system then connects and
operates normally.
If the transmitter is turned on first, the transmitter
scans the 2.4GHz band and acquires two open
channels. When the receiver is then turned on for a
short period (the time it takes to connect), all servos
except for the throttle are driven to their preset
fail-safe positions while the throttle has no output
pulse. The receiver scans the 2.4GHz band looking
for the previously stored GUID; and when it locates
the specific GUID code and confirms uncorrupted
repeatable packet information the system connects and
normal operation takes place. Typically this takes 2 to
6 seconds.
2. Q: Sometimes the system takes longer to connect and
sometimes it doesn’t connect at all?
A: In order for the system to connect (after the receiver
is bound) the receiver must receive a large number of
continuous (one after the other) uninterrupted perfect
packets from the transmitter. This process is purposely
critical of the environment, ensuring that it’s safe to
fly when the system does connect. If the transmitter
is too close to the receiver (less than 4 feet) or if
the transmitter is located near metal objects (metal
transmitter case, the bed of a truck, the top of a metal
work bench, etc.) connection will take longer, and in
some cases, connection will not occur as the system
is receiving reflected 2.4GHz energy from itself and is
interpreting this as unfriendly noise. Moving the system
away from metal objects or moving the transmitter away
from the receiver and powering the system up again will
cause a connection to occur. This only happens during
the initial connection. Once connected, the system is
locked-in and, should a loss of signal occur (fail-safe),
the system connects immediately (4ms) when signal is
regained.
Summary of Contents for X9503 2.4
Page 43: ...A 56...
Page 103: ...S 68...