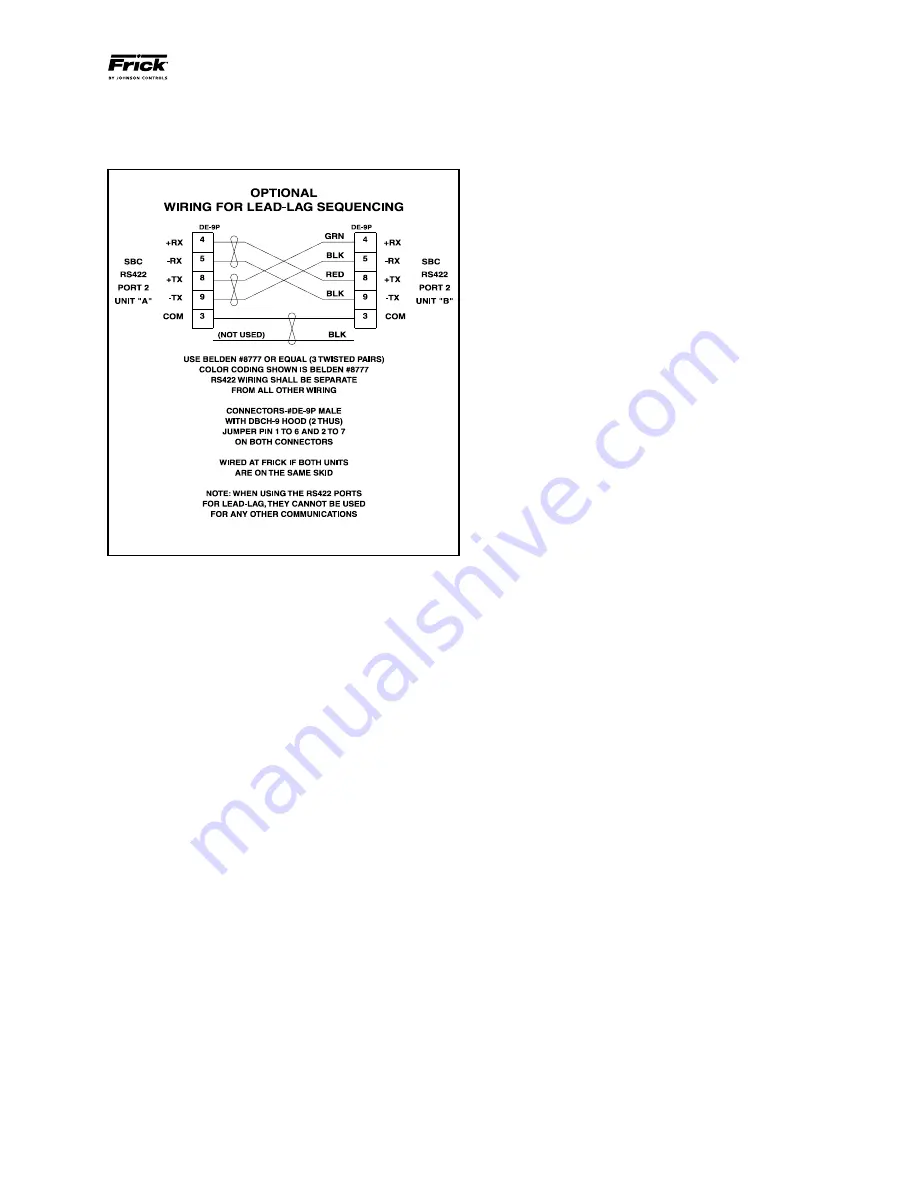
RXB PLUS ROTARY SCREW COMPRESSOR UNITS
OPERATION
070.101-IOM (JAN 13)
Page 25
a.solid.state.out.put.device.capable.of.handling.control.volt-
age.and.the.instruc.tion.is.executed..In.some.cases,.such.
as.load.and.unload.instructions,.the.computer.dis.plays.the.
instruction.on.the.Operating.display.with.an.L.(load).or.U.
(unload).symbol.at.the.same.time.as.the.appropriate.output.
is.energized.
If.the.microprocessor.receives.information.that.indicates.an.
abnormal.operating.condition.has.been.reached.or.is.present,.
it.will.generate.one.or.more.of.the.following.instructions:
1.
.If.a.subsystem.on.the.compressor.unit,.such.as.the.oil.
heater(s). or. liquid. injection,. can. correct. the. problem,. the.
microprocessor.will.energize.or.de-energize.this.system.
2.
. If. a. prealarm. setpoint. has. been. reached. the. micro-
processor.will.trigger.the.prealarm.and.display.this.informa-
tion.on.the.Operating.dis.play.and.the.Annunciator.display.
3.
.If.a.cutout.setpoint.has.been.reached,.the.microprocessor.
will.shut.down.the.compressor..The.microprocessor.will.indi-
cate.
CUTOUT
.on.the.Operating.dis.play.and.the.information.
present.on.the.Operating.display.at.the.moment.of.cutout.
will.be.stored.and.can.be.retrieved.by.rotating.displays.to.
the.Freeze.display..Additional.information.will.be.available.
through.the.Annunciator.and.Shutdown.Record.displays.
A.typical.example.of.how.the.microprocessor.re.sponds.can.
be. illustrated. by. the. responses. gener.ated. by. the. micro-
processor. as. oil. temperature. increases.. Assume. that. the.
ambient.temperature.and.compressor.unit.temperature.are.
45
O
F.and.you.have.just.pressed.the.
[RUN]
.key.to.start.the.
compressor.unit:
AT 45°F.
The.microprocessor.receives.information.that.the.oil.tempera-
ture.is.below.49
°
F,.the.Low.Oil.Temperature.Cutout.setpoint,.
and.and.shuts.down.the.unit...The.micropro.cessor.will.prevent.
the.compressor.package.from.running..The.microproces.sor.
also. instructs. the. oil. heater(s). output. to. ener.gize. the. oil.
heater(s).
AT 50°F.
When.the.oil.temperature.reached.50
°
F.the.micropro.cessor.
would.allow.the.Low.Oil.Temperature.Cutout.to.be.cleared.
and.the.compressor.unit.could.now.be.started..(Assume.that.
the.
[RUN]
.key.has.been.pressed.and.that.the.com.pressor.
has.now.started.).The.Low.Oil.Temperature.Alarm.would.still.
be.engaged.and.cannot.be.cleared.until.oil.temperature.ex-
ceeds.58
°
F..The.oil.heater(s).shut.off.on.compressor.start.
AT 113°F
The. microprocessor. instructs. the. liquid. injection. solenoid.
output.to.deenergize.the.liquid-injection.solenoid.
AT 122°F
The. microprocessor. instructs. the. liquid. injection. solenoid.
output.to.energize..
AT 110°F TO 150°F.
Normal. operating. range..The. microprocessor. contin.ues.
monitoring.oil.temperature.and.reporting.this.informa.tion.on.
the.Operating.display.
AT 158°F.
The.microprocessor.triggers.the.High.Oil.Temperature.Alarm.
and. displays. the. alarm. on. the. Operating. display. and. the.
Annunciator.display.
LEAD-LAG OPTION (continued)
TYPICAL LEAD-LAG WIRING
HOW THE MICROPROCESSOR WORKS
- SUMMARY -
The.Frick.microprocessor.has.4.major.components.and.a.va-
riety.of.sensors..The.major.components.are.the.SBC.(single.
board.computer),.two.display.screens,.and.the.keyboard.
The.SBC.can.be.considered.the.brain.of.the.micro.proces.sor.
control.console..The.SBC.contains.the.logic.center.which.
provides.the.rules.by.which.the.micro.pro.cessor.will.oper-
ate,. the. integrated. cir.cuit. chips. which. store. the. burned-in.
memory.of.how.the.compres.sor.unit.is.to.behave,.an.analog.
input.to.convert.VDC.from.the.various.sensors.into.computer.
binary.language,.and.RAM.(random.access.memory).inte-
grated.circuit.chips.to.store.information.which.can.be.readily.
changed.by.the.microprocessor.or,.as.in.the.case.of.adjust-
able.setpoints,.by.the.operator..The.SBC.collects.information,.
processes.the.information,.and.delivers.instructions.to.the.
displays.and.to.the.output.modules.
The.SBC.gathers.information.from.several.sources.on.the.
compressor. unit.. Pressure. transducers. sense. changes. in.
pressure.and.return.a.variable.DC.volt.age.of.1.to.5.VDC.to.
the.SBC..The.signals.are.converted.into.binary.code.which.
the.microproces.sor.under.stands..The.microproces.sor.scans.
the.incoming.data.many.times.per.second.and.compares.
the.information.it.receives.with.the.instructions.programmed.
in. the. PROM. chips,. information. stored. in. the. RAM. chips,.
and.instructions.it.has.received.from.the.console.keyboard..
As. operating. conditions. change,. the. microprocessor. also.
forwards.the.infor.mation.it.is.receiving.to.the.display.screen..
When.an.operating.condition.or.conditions.develop.which.
the.micropro.cessor.program.identifies.as.requiring.a.specific.
action,.the.microprocessor.generates.an.instruction.which.
is.forwarded.to.the.output.mod.ules..The.instruction.triggers.
Figure 20 - Optional Wiring for Lead-Lag Sequencing