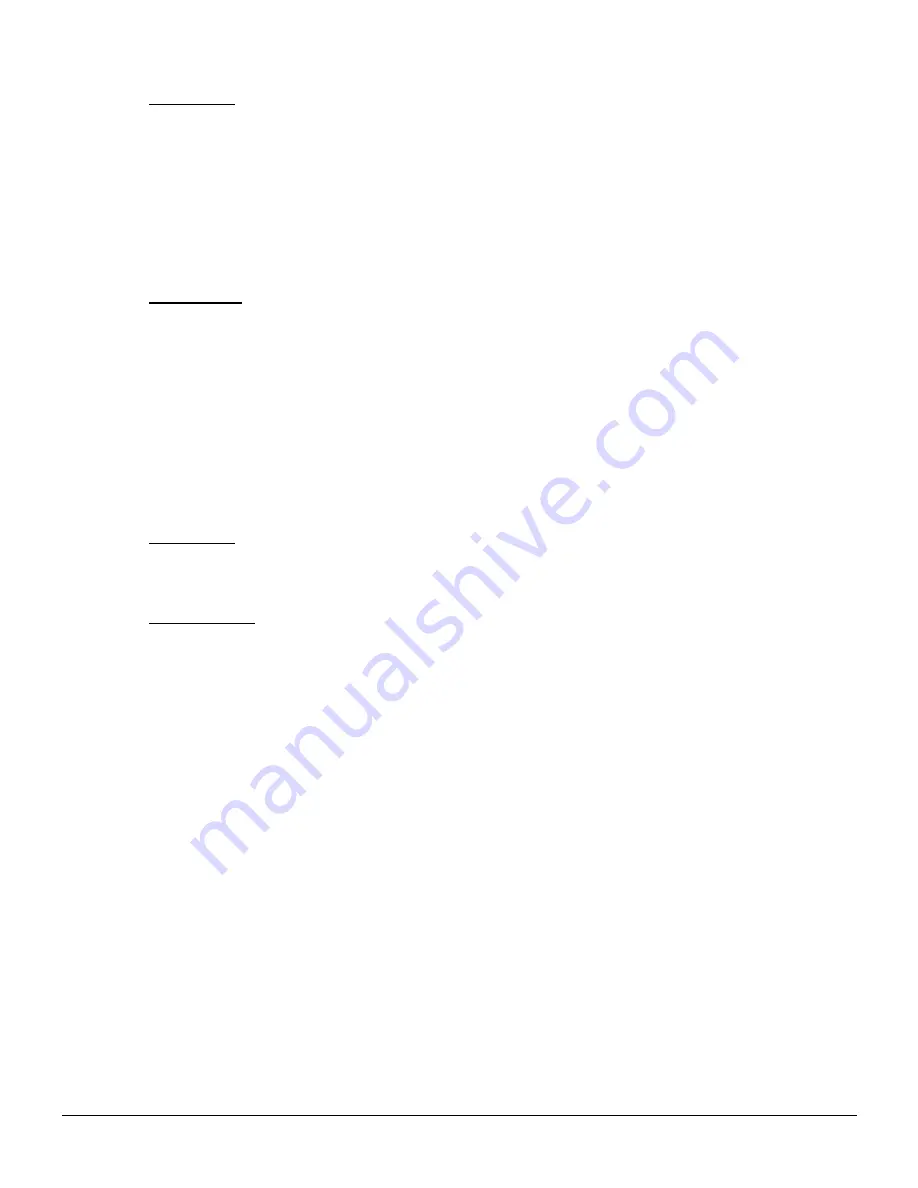
3-6
The relays:
•
INS must not be activated.
•
CDC,HDC and RED must be activated.
•
RPA must be activated (if required).
•
RPR must be in phase (is Across the line or Y-Delta start).
The alarms:
•
Hold for 2.5 seconds the « MANUAL RESET » button on the controller inspection board to
reset the controller and clear the alarms. The controller will be rearmed only if all conditions
are ok.
•
By using the LCD, erase the alarms and then consult the alarms list to check that there are no
more. (Section 1 for use of the LCD).
M.
Now the elevator must move in inspection mode by placing a jumper between the terminals "+A"
and "PCH" for move in up direction or "+A" and "PCB" for move in down direction.
Moving up: the input light PCH turns ON. The UCT (with Benshaw SOFT START), UCA and
SU CPU outputs turn ON. The two ascent valves (U and US) outputs and their corresponding
lights turn ON and the car starts moving up.
Moving down: the input light PCB turns on. The SD output light, the two descent valves (DV and
DR) outputs and their corresponding lights turn ON and the car starts moving down.
IMPORTANT
The CPU inputs are designed to operate 24 volts DC. DANGER: Never apply 120 volts AC for
it may cause severe damage to the inputs.
On reception of the controller, the "COM" terminal is grounded.
Summary of Contents for 2000 Series
Page 1: ...USER S MANUAL HYDRAULIC ELEVATOR CONTROLLER CANBUS PROCESSOR JLL 2000 SERIES VERSION 2 02 000 ...
Page 2: ......
Page 5: ......
Page 17: ...2 1 2 USE OF THE PROGRAMMING CONSOLE PRO01 OU PRO27 Not available ...
Page 25: ...5 1 5 CONTROLLER TYPE Section not applicable ...
Page 28: ...6 3 Standard tape selector installation ...
Page 44: ...6 19 ...
Page 47: ...7 22 7 TERMINAL SPEED REDUCING DEVICE FOR ELEVATOR GREATER THAN 50 MIN Section not applicable ...
Page 60: ...10 2 ...
Page 72: ...10 14 Alarms Description Causes et verifications supplied Check the door opening ...