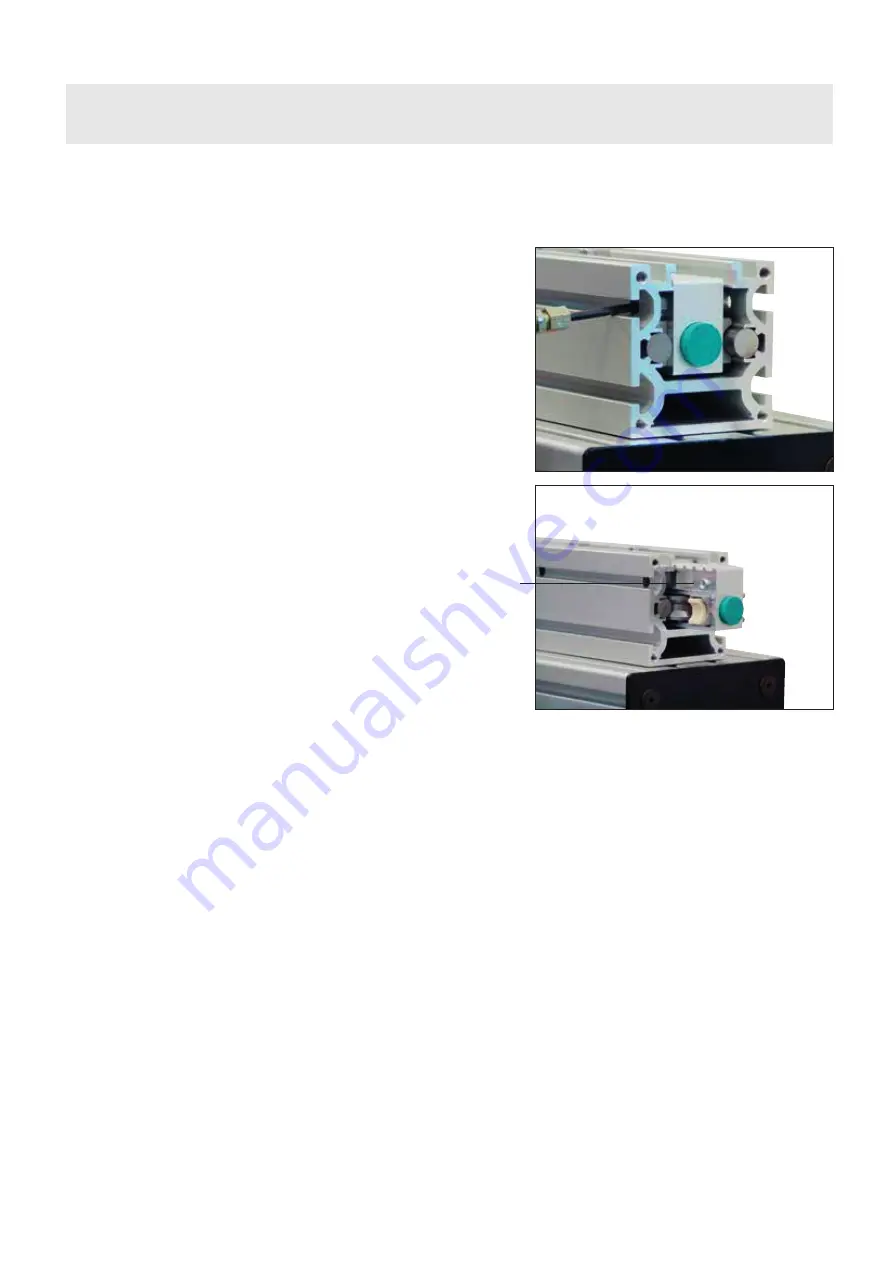
23
Basic lubrication for the guide is applied by the operator under normal operat-
ing conditions.
The service life for the initial lubrication applies to normal operating conditions.
A special oil press can be used to provide additional lubrication to the guide
system.
To do this, move the Carriage to the “maintenance position” defined by the
position of the lubrication holes and lubricate it through the three holes with the
same spacing as the grease nipples (see Section 4.2).
To apply the oil, insert the long tip of the oil press through the maintenance
holes onto the Carriage grease nipples and apply the oil.
The End Cap and Lubricating Systems need to be re-lubricated with the
required amount from one side only.
Fill quantity:
Approx. 1 ml per maintenance hole per maintenance interval (1 ml is equivalent
to one actuation of the Pressol oil can)
Maintenance interval:
Every 6 months or every 2,500 km
Greases containing solid particles (e.g. graphite and MoS2 additives) must not
be used!
Grease nipple
Maintenance
Under special operating conditions such as a special installation type,
dust, short travel distance, influence from solvents, etc. the lubrication intervals
will need to be adapted to suit the relevant application scenario.
Recommended oil:
Track Oil for Linear Guides
(recommended: Klüber Oil 4 UH1-460), Art. No. 0.0.612.75
Auxiliary tool:
Pressol oil can KLE-LR, 0.0.612.74
Normal operating conditions:
Ambient temperature: 10 °C–40 °C
50% of max. load