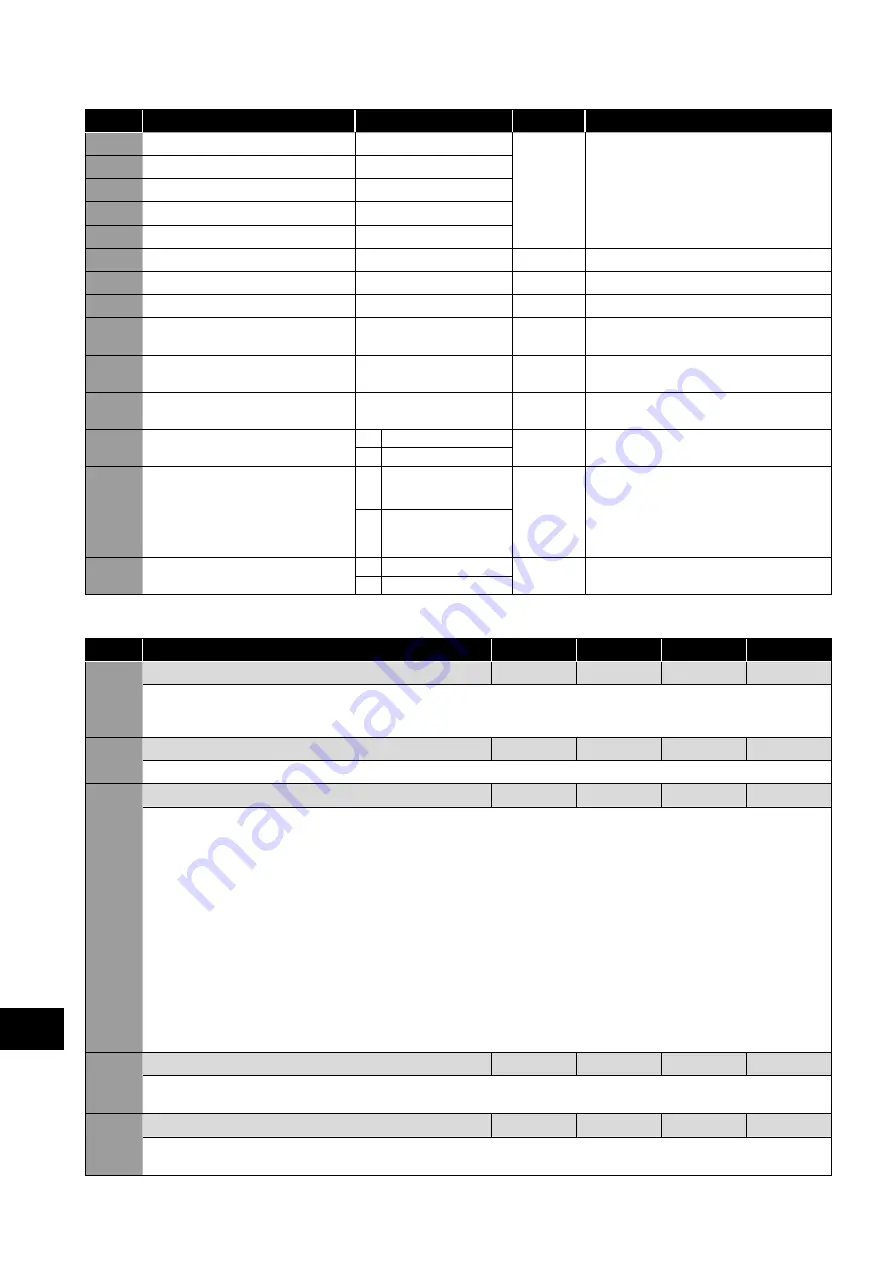
50
| Optidrive Eco User Guide |
Version 3.05
www.invertekdrives.com
9.5.2. Parameter Group 7 – Motor Control
Par.
Function
Setting Range
Default
Notes
P7-01
Motor Stator Resistance
0.000 – 65.535
Drive
Dependent
Motor date, measured or calculated curing
the autotune.
P7-04 is not used for PM & BLDC Motors.
P7-06 is used only for PM motors.
P7-03
Motor Stator Inductance (d)
0.0000 – 1.0000
P7-04
Magnetising Current (id)
Drive Dependent
P7-05
Motor Leakage Coefficient (Sigma)
0.000 – 0.250
P7-06
Motor Q Axis Inuctance (Lsq)
0.0000 – 1.0000
P7-09
Over Voltage Current Limit
0.0 – 100.0%
5.0%
P7-10
Load Inertia Constant
0 - 600
10
P7-11
Pulse Width Minimum Limit
0 - 500
P7-12
V/F Mode Magnetising Delay Time
0 – 5000ms
Drive
Dependent
Sets the motor magnetising period in V/F Mode.
Sets the motor alignment time in PM modes.
P7-14
Low Frequency Torque Boost
0.0 – 100.0%
0.0%
For PM Motors, applies a torque boost current
at low frequency, % x P1-08.
P7-15
Torque Boost Frequency Limit
0.0 – 50.0%
0.0%
For PM motors, determines the frequency, % x
P1-09 when the boost current is removed.
P7-18
Over Modulation
0
Disable
0
1
Enable
P7-19
BLDC Light Load Optimization
0
Disable
1
When P4-01 = 4 (BLDC control) and P7-19 = 1
(Enable) the drive will reduce the output voltage
during light load operation in order to improve
motor efficiency. This setting has no effect if
the motor is driven close to its nominal current,
where the nominal flux level will be applied.
1
Enable
P7-20
Modulation Mode
0
3-Phase Modulation
0
1
2-Phase Modulation
9.6. Parameter Group 8 – Application Function Specific Parameters
Par
Name
Minimum
Maximum
Default
Units
P8-01
Pump Stir Interval Duration
0
60000
0
Minutes
This parameter can be used to set a pre-defined period of inactivity, whereby if the drive remains in standby mode for a period of time
exceeding the limit, stir function is activated, and the drive will operate at preset speed 7 (P2-07) for the time set in P8-02. This allows
the pump to stir, preventing sediment from settling and avoiding a blockage.
P8-02
Pump Stir Activation Time
1
6000
10
Seconds
Set the time period that the stir function will be active once triggered (excludes time for deceleration to stop).
P8-03
Pump Clean Function Select
0
3
-
-
This parameter configures the drive conditions that will cause activation of the automatic pump clean function. When activated, the
pump clean will operate the pump at preset speed 5 (P2-05) for the time period set in P8-04, followed by Preset Speed 6 (P2-06)
(Providing P2-06 <> 0) for the time set in P8-04, before resuming normal operation. During the cleaning cycle, the ramp time set in P8-
05 is used for both acceleration and deceleration, and overrides P1-03 and P1-04.
Where possible, P2-05 and P2-06 may be set to negative values, to allow the pump to be reversed. For best results, it is recommended
to use as high a speed as possible, and to adjust P8-05 to allow a short acceleration time whilst avoiding over current trips.
0 : Disabled.
1 : Active on start-up only.
The pump cleaning function operates every time the pump is started.
2 : Active on start-up and high current detection.
The pump cleaning function operates every time the pump is started,
and also in the event that the drive detects a possible pump blockage during normal operation. This requires the Motor Current Profile
Monitoring function to be active and commissioned for correct operation, see parameter P8-06.
3 : Active on high current detection only.
The pump cleaning function operates only when a possible pump blockage is
detected during normal operation. This requires the Motor Current Profile Monitoring function to be active and commissioned for
correct operation, see parameter P8-06.
NOTE
The pump clean function can also be activated by digital input configured in group 9 parameters.
P8-04
Pump Clean Time
0
600
0
Seconds
Sets the time period for the operation of the pump cleaning cycle. When bi-directional pump cleaning is selected, the time interval is
used twice, once in each direction.
P8-05
Pump Clean Function Ramp Time
0
6000
30
Seconds
Independent ramp rate used only for the pump automatic cleaning function (see P8-03) when the motor is Accelerated as part of the
cleaning cycle.
9
Extended P
arameters