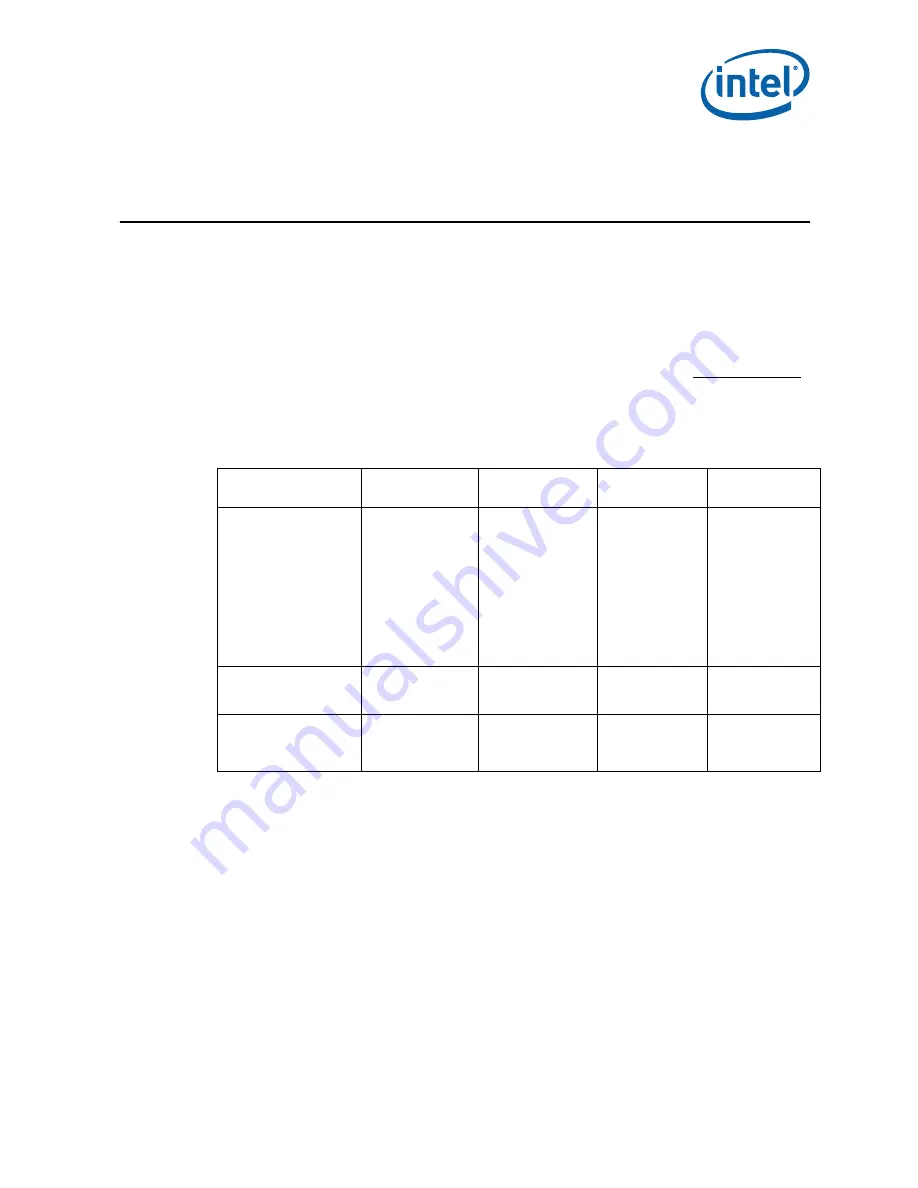
Thermal/Mechanical Specifications and Design Guide
105
Quality and Reliability Requirements
9
Quality and Reliability
Requirements
9.1
Use Conditions
Intel evaluates reliability performance based on the use conditions (operating
environment) of the end product by using acceleration models.
The use condition environment definitions provided in
and
based on speculative use condition assumptions, and are provided as
examples only
.
Based on the system enabling boundary condition, the solder ball temperature can vary
and needs to be comprehended for reliability assessment.
Table 9-1.
Use Conditions Environment (System Level)
Use Environment
Speculative
Stress Condition
Example Use
Condition
Example 7-Yr
Stress Equiv.
Example 10-Yr
Stress Equiv.
Slow small internal
gradient changes due to
external ambient
(temperature cycle or
externally heated)
Fast, large gradient
on/off to max operating
temp.
(power cycle or
internally heated
including power save
features)
Temperature Cycle
DT = 35–44 °C
(solder joint)
550–930 cycles
Temp Cycle
(-25 °C to 100 °C)
780–1345 cycles
Temp Cycle
(-25 °C to 100 °C)
High ambient moisture
during low-power state
(operating voltage)
THB/HAST
T = 25–30 °C
85%RH
(ambient)
110–220 hrs at
110 °C 85%RH
145–240 hrs at
110 °C 85%RH
High Operating
temperature and short
duration high
temperature exposures
Bake
T = 95–105 °C
(contact)
700–2500 hrs at
125 °C
800–3300 hrs at
125 °C
Summary of Contents for BX80619I73820
Page 10: ...10 Thermal Mechanical Specifications and Design Guide...
Page 14: ...Introduction 14 Thermal Mechanical Specifications and Design Guide...
Page 104: ...Thermal Solutions 104 Thermal Mechanical Specifications and Design Guide...
Page 112: ...Mechanical Drawings 112 Thermal Mechanical Specifications and Design Guide...
Page 118: ...Socket Mechanical Drawings 118 Thermal Mechanical Specifications and Design Guide...
Page 124: ...Package Mechanical Drawings 124 Thermal Mechanical Specifications and Design Guide...