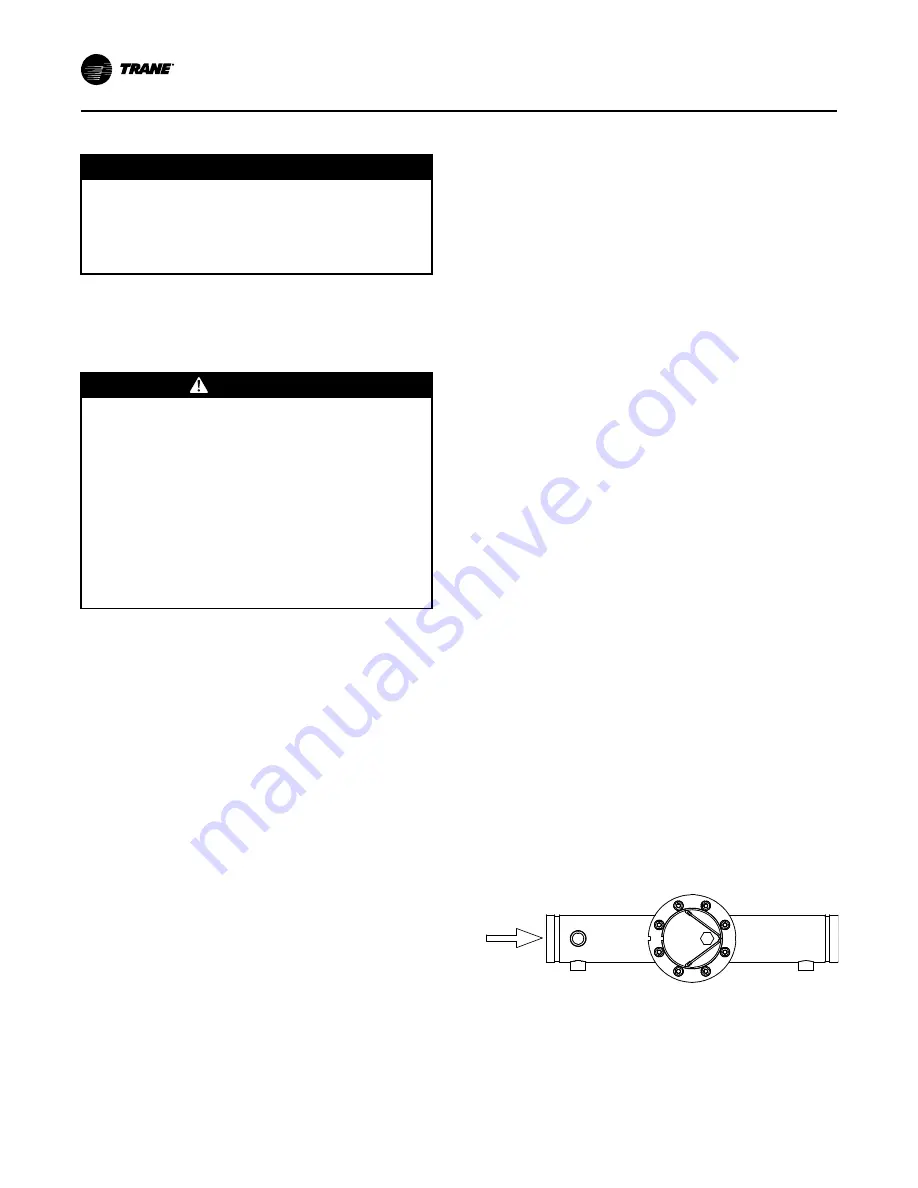
70
AC-SVX002C-EN
Cleaning Air Side of Coils
N
NO
OT
TIIC
CE
E
C
Co
oiill D
Da
am
ma
ag
ge
e!!
U
Usse
e o
off cco
oiill cclle
ea
an
niin
ng
g a
ag
ge
en
nttss o
on
n u
un
ncco
oa
atte
ed
d cco
oiillss
cco
ou
ulld
d cca
au
usse
e d
da
am
ma
ag
ge
e tto
o cco
oiillss..
D
Do
o n
no
ott u
usse
e cco
oiill cclle
ea
an
niin
ng
g a
ag
ge
en
nttss tto
o u
un
ncco
oa
atte
ed
d cclle
ea
an
n
cco
oiillss.. U
Usse
e cclle
ea
an
n w
wa
atte
err o
on
nlly
y..
Do not use detergents to clean the air side of coils. Use
clean water only. Clean from inside out by removing
end panels.
Cleaning Coated Coils
W
WA
AR
RN
NIIN
NG
G
H
Ha
azza
arrd
do
ou
uss C
Ch
he
em
miicca
allss!!
C
Co
oiill cclle
ea
an
niin
ng
g a
ag
ge
en
nttss cca
an
n b
be
e e
eiitth
he
err a
acciid
diicc o
orr h
hiig
gh
hlly
y
a
allkka
alliin
ne
e a
an
nd
d cca
an
n b
bu
urrn
n sse
ev
ve
erre
elly
y iiff cco
on
ntta
acctt w
wiitth
h sskkiin
n
o
orr e
ey
ye
ess o
occccu
urrss..
H
Ha
an
nd
dlle
e cch
he
em
miicca
all cca
arre
effu
ulllly
y a
an
nd
d a
av
vo
oiid
d cco
on
ntta
acctt w
wiitth
h
sskkiin
n.. A
AL
LW
WA
AY
YS
S w
we
ea
arr P
Pe
errsso
on
na
all P
Prro
otte
eccttiiv
ve
e
E
Eq
qu
uiip
pm
me
en
ntt ((P
PP
PE
E)) iin
nccllu
ud
diin
ng
g g
go
og
gg
glle
ess o
orr ffa
acce
e ssh
hiie
elld
d,,
cch
he
em
miicca
all rre
essiisstta
an
ntt g
gllo
ov
ve
ess,, b
bo
oo
ottss,, a
ap
prro
on
n o
orr ssu
uiitt a
ass
rre
eq
qu
uiirre
ed
d.. F
Fo
orr p
pe
errsso
on
na
all ssa
affe
etty
y rre
effe
err tto
o tth
he
e cclle
ea
an
niin
ng
g
a
ag
ge
en
ntt m
ma
an
nu
uffa
accttu
urre
err’’ss M
Ma
atte
erriia
allss S
Sa
affe
etty
y D
Da
atta
a S
Sh
he
ee
ett
a
an
nd
d ffo
ollllo
ow
w a
allll rre
ecco
om
mm
me
en
nd
de
ed
d ssa
affe
e h
ha
an
nd
dlliin
ng
g
p
prra
accttiicce
ess..
Coated coils may be cleaned using traditional
detergents.
Repair/Replacement of Microchannel
Coil
Microchannel coils are considerably more robust in
design than tube and fin condenser coils, however they
are not indestructible. When damage or a leak occurs,
contact your local Trane office.
Condenser Coil Corrosion Protection
Inspection
Perform coil inspection each time coils are cleaned.
Inspect corrosion protection at each coil refrigerant
connection where the copper tube joins the aluminum
manifold. If damaged or missing, wrap new Prestite
Insulated tar tape (STR01506) on joint to cover area
from the aluminum header body to at least 2 inches of
the copper tube. Seal insulation using hand pressure.
Rubber gloves are suggested when handling
insulation.
N
No
otte
e:: Prestite insulated tar tape is required for all units
at each copper/aluminum connection. This
requirement is NOT associated with the coated
coil option.
Evaporator Maintenance
This chiller uses a brazed plate heat exchanger (BPHE)
evaporator with factory-installed electronic flow switch
(IFM efector) that is positioned in the evaporator water
pipe. The evaporator inlet also includes a factory-
installed immersion heater for freeze protection and a
water strainer that must be kept in place to keep debris
out of the evaporator.
N
No
otte
e:: Strainer maintenance is critical to proper
operation and reliability. Any particles larger
than 1mm entering the BPHE evaporator may
cause the evaporator to fail, requiring
replacement.
Acceptable BPHE evaporator water flow rate is 1.2 to
3.6 gpm/ton. To maintain 54-44°F in/ out chilled water
temperatures, the nominal water flow rate is 2.4 GPM/
ton.
Minimum water flow rate must be maintained to avoid
laminar flow, potential evaporator freezing, scaling and
poor temperature control. The microprocessor and
capacity control algorithms are designed to take a 10
percent change in water flow rate per minute while
maintaining a ±2°F (1.1°C) leaving water temperature
control accuracy. The chiller tolerates up to 30 percent
per minute water flow variation as long as the flow is
equal to or greater than minimum flow requirements.
Maximum water flow is 18 feet per second. Flow rates
greater than this will cause excessive erosion.
The BPHE evaporator is difficult to clean should it
become plugged with debris. Indications of a plugged
BPHE evaporator include "wet" suction due to lack of
heat exchange, loss of superheat control, depressed
discharge superheat, compressor oil dilution and/or
starvation and premature compressor failure.
Water Strainer Maintenance
Units without Pump Package
An in-line strainer with a V-shaped sieve is used for
units that do not have factory-installed pump package
option.
Figure 50.
In-line strainer, units without pump
package
WATER FLOW
DIRECTION
The strainer is equipped with a blow-down port. The
strainer is a 16 mesh (approximately 1 mm) material.
For maximum efficiency, a differential pressure gauge
installed across the inlet and outlet will indicate
pressure loss due to clogging and may be used as a
guide to determine when cleaning is required. The taps