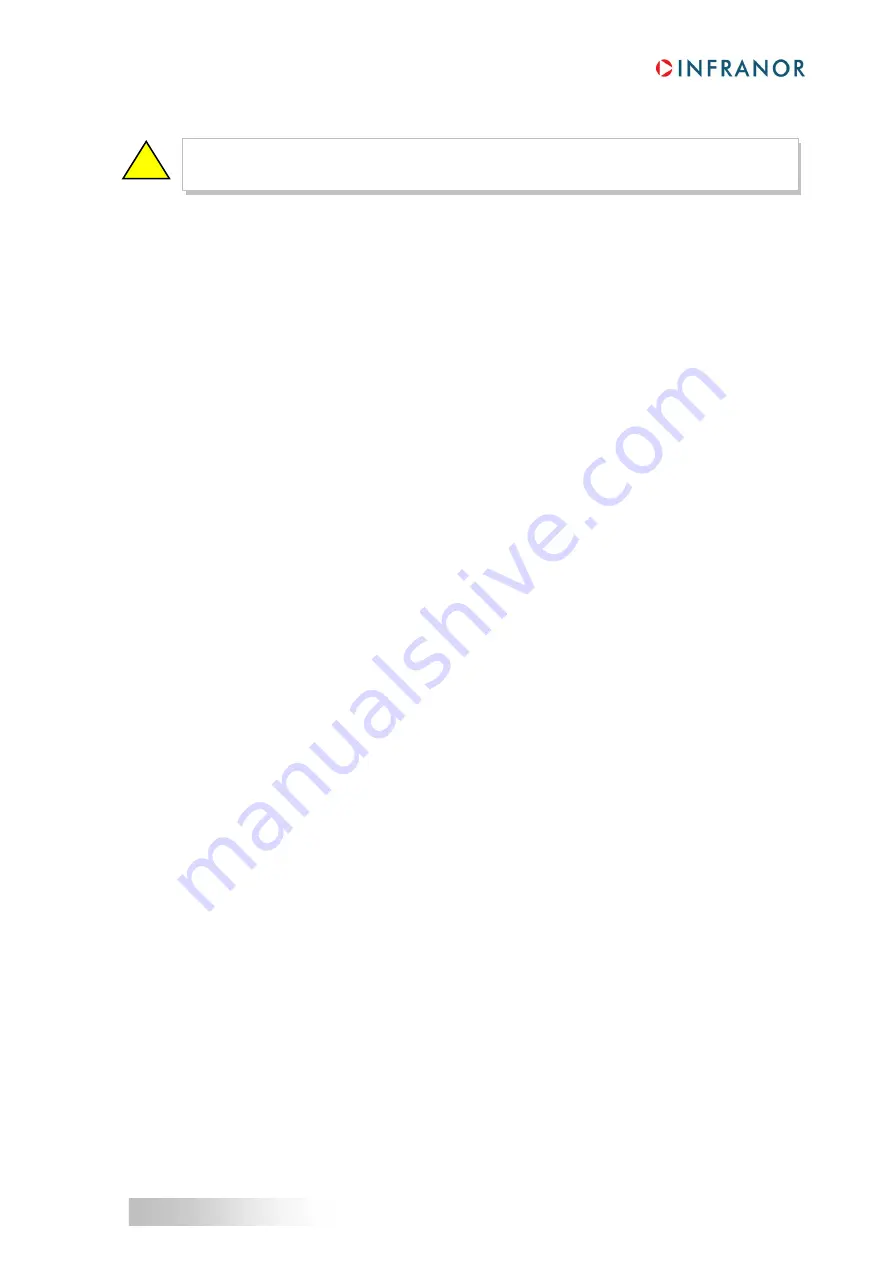
39
XtrapulsCD1-a
Chapter 6 - Commissioning
3 - DRIVE COMMISSIONING AND ADJUSTMENT
3.1 - COMMUNICATION VIA THE SERIAL LINK
Connect the serial link RS 232 between the PC and the drive.
The "ENABLE" input must be disabled and the analog input command CV short-circuited.
Turn the drive on and start the
VISUAL DRIVE SETUP
PC software under WINDOWS
®
.
If the message "
No serial communication found
" appears on the screen, click on
OK
and check following
points:
-
the drive is on (green LED
ON
must lit),
-
the drive and the PC are correctly connected via the RS 232 link,
-
the software configuration (
Com. port and Baudrate
) is correct.
3.2
– SENSOR FEEDBACK CONFIGURATION
The drive feedback sensor configuration is selectable by software and stored into the drive EEPROM.
Resolver sensor feedback is the standard drive configuration. For a motor equipped with an encoder position
sensor proceed as described below:
Select first the appropriate encoder type in the
Feedback configuration
menu.
Select then
Encoder feedback
and validate the selection.
If the motor is using Hall Effect Sensors: check that the ENABLE input is disabled and the drive turned on and
move the motor manually over one revolution, or one pole pitch for a linear motor. If the
HES
error is displayed,
turn off the drive and check the following points before turning it on again:
The HES are correctly wired on the drive X3 connector (if 60° type HES are used, check the various HES
signals wiring combinations to find the right wiring order).
The HES supply voltage value is correct.
The
Motor encoder resolution
parameter value is correct.
If the motor HES are not working correctly, select the appropriate
Incremental encoder
type (without HES) in the
Feedback configuration
menu and start the drive commissioning in this configuration.
If the mot
or is using an absolute single-turn Sin/Cos encoder (Heidenhain ERN 1085 or compliant), check that the
ENABLE input is disabled and the drive turned on and
m
ove the motor manually over one revolution. If the
HES
error is displayed, turn off the drive and check the following points before turning it on again:
The Sin/Cos encoder commutation channels are correctly wired on the drive X3 connector.
The Sin/Cos encoder supply voltage value is correct.
The
Motor encoder resolution
parameter value is correct.
Carry out the command
Save parameters to EEPROM
before switching off the drive in order to save the
feedback configuration.
3.3 - DRIVE ADJUSTMENT
Select the appropriate motor type in the
Motor List
.
Check for the compliance of the
Current Limitation
parameters with the motor and drive specifications.
For the commissioning, the I
2
t "fusing" mode is recommended. (see chapter 8, section 3.2).
If the
Incremental encoder
configuration
without HES
is selected for the feedback sensor, start the motor
Phasing
procedure.
The motor
Phasing
procedure can be released in the command window of the
VISUAL DRIVE SETUP
software or by the activation of the
CV0
input.
If the motor used in the application is not mentioned in the
Motor List
, select the
New motor
command and
follow the instructions.
Check that the
Speed limitation
parameters are compatible with the motor specifications.
The drive command cables (input command, serial link, resolver, encoder, HES) as well as the
power cables must be connected and disconnected with the drive turned off.
!