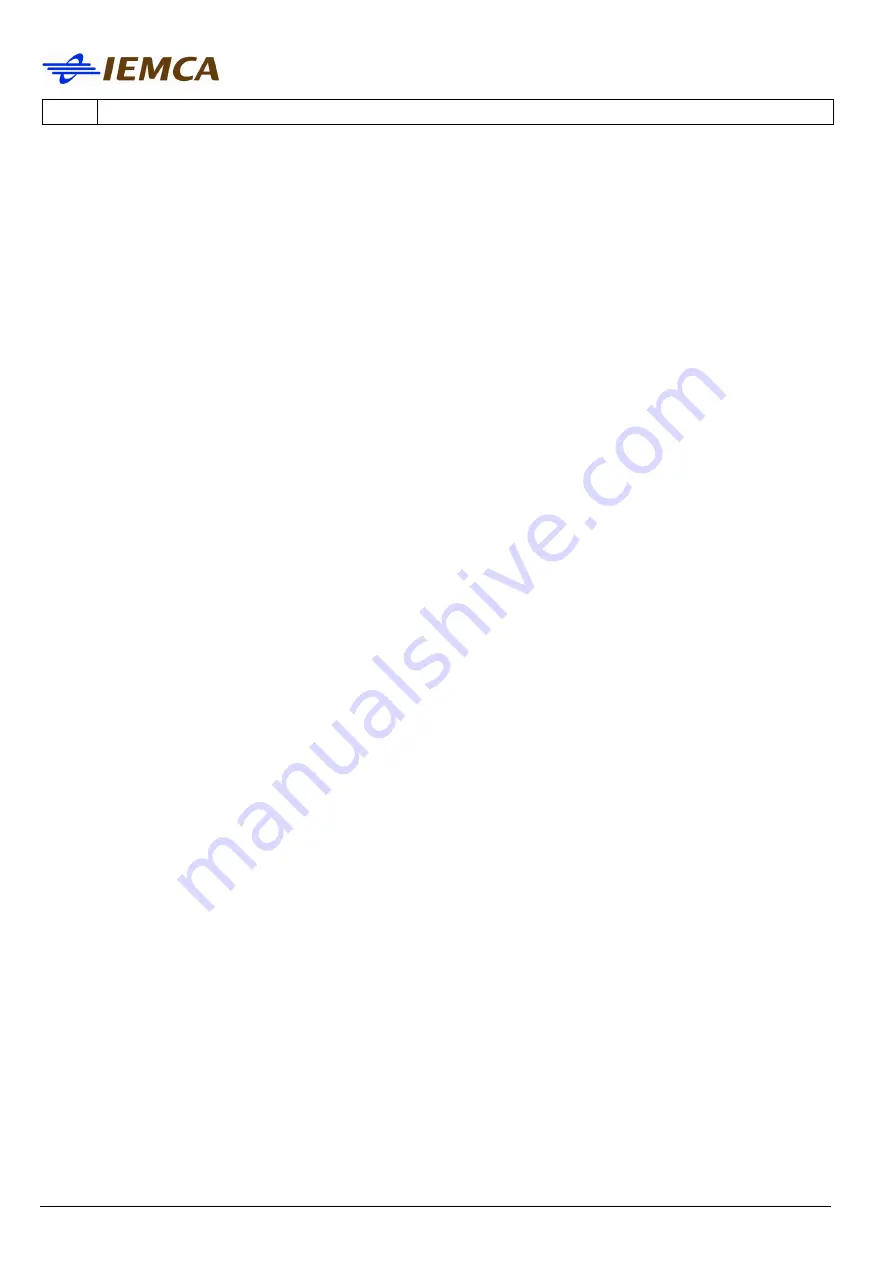
EN
3 - SAFETY PROCEDURES - GENERAL INFORMATION
KID 80 IV
3 - Pag. 6 / 6
3.7
General Description of Supply
The bar feeder you bought is a machine designed to feed machine tools properly prepared for
bar machining. It consists of:
A basic unit made up of a metal structure, a control panel, safety devices and protections in
compliance with the EU regulations governing this sector.
A set of format parts related to the specific machining processes that the machine will perform.
According to the terminology used by Iemca these parts are named: guide channels, bar
pushers, revolving tips, collets, bushes and front noses. Because of the kind of use, these parts
are subject to wear.
Any additional parts can be supplied upon request.
Applicable Safety Regulation
According to Directive 2006/42/EC article 2B, the bar feeder is an interchangeable equipment
and is supplied with the appropriate safety devices.
Together with the supply you will find the EC declaration of conformity in compliance with the
above-mentioned Directive.
The list of the safety devices is shown in section 2, paragraph 2.3, of this manual.
The bar feeder should be installed according to the manufacturer's instructions which are
highlighted in the supplied check list.
Should the bar feeder be used together with machine tools that do not have the CE marking,
Iemca reminds to their clients that they should assess if the device is in compliance with
Directive 2009/104/EC and subsequent amendments even after installing the bar feeder.
Safety warning. Only qualified and properly trained personnel can work with machine tools and
the related interchangeable equipments.
Summary of Contents for KID 80-IV Touch
Page 2: ......
Page 4: ......
Page 8: ......
Page 28: ...EN 2 TECHNICAL INFORMATION KID 80 IV 2 Pag 14 18 KID8080_III_02_14_2 ...
Page 37: ...3 SAFETY PROCEDURES GENERAL INFORMATION KID 80 IV EN 3 Pag 5 6 3 6 EC CONFORMITY DECLARATION ...
Page 80: ......
Page 85: ...7 BAR FEEDER MAINTENANCE KID 80 IV EN 7 Pag 5 6 7 3 GREASING POINTS grasso Grease olio Grease ...
Page 92: ......