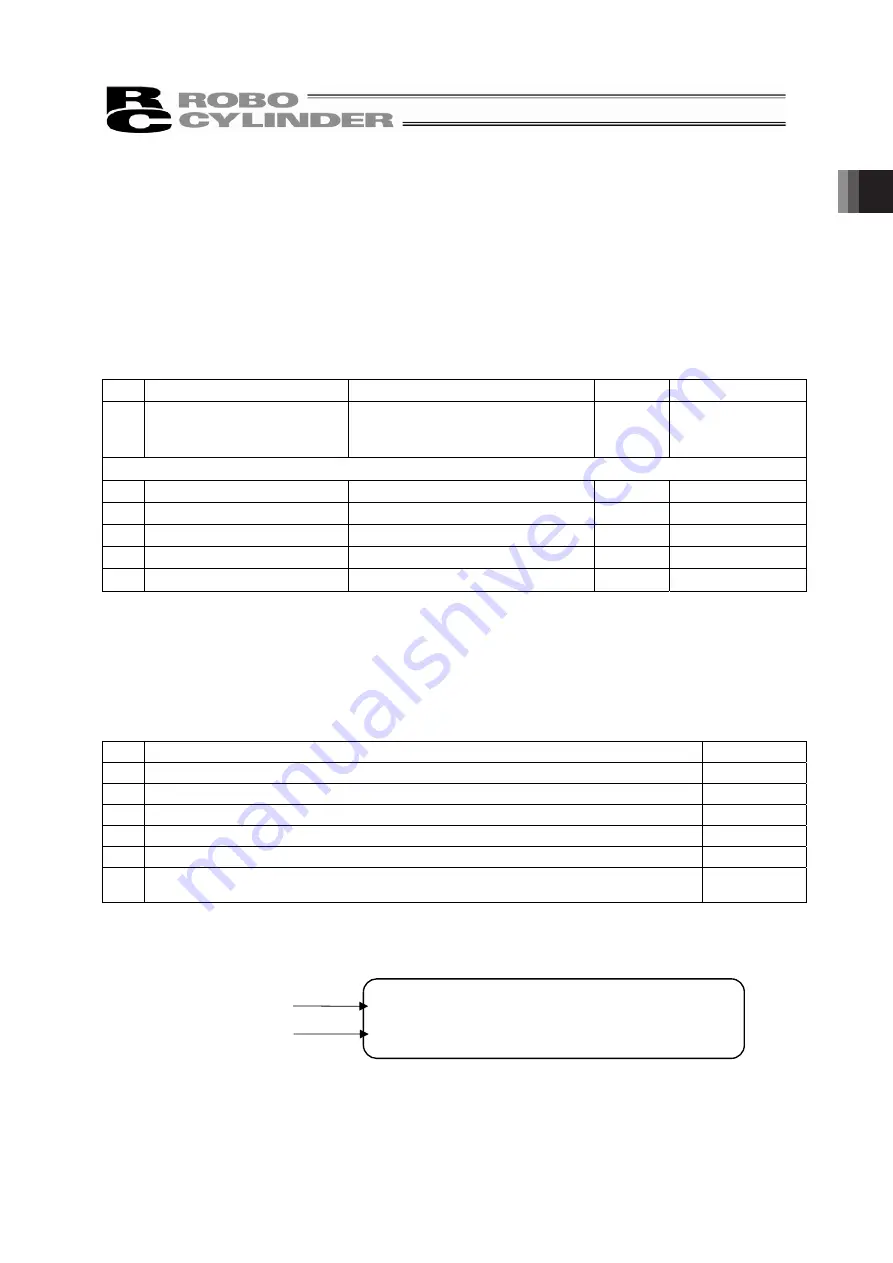
1. Specifications Check
11
1. Specifications Check
1.1 Checking the Product
The standard configuration of this product is comprised of the following parts.
See the component list for the details of the enclosed components. If you find any fault or missing parts,
contact your local IAI distributor.
1.1.1 Parts
No.
Name
Model Number
Quantity
Remarks
1 Actuator
Refer to “How to Read the Model
Nameplate” and “How to Read the
Model Number.”
1
Accessories
2 Motor • Encoder Cables
(Note1)
1
3 In-house Made Seals
1
4 First Step Guide
1
5 Instruction Manual (DVD)
1
6 Safety Guide
1
Note1 The motor • encoder cables supplied vary depending on the controller used.
[Refer to 1.4, “Motor • Encoder Cables.”]
1.1.2 Related Instruction Manuals for the Each Controller Supported by This Product
Shown below is a list of the instruction manuals for the controllers related to this product which is
recorded in Instruction Manual (DVD).
No.
Name
Control No.
1 Instruction Manual for PCON-CA/CFA Controller
ME0289
2 Instruction Manual for MSEP Controller
ME0299
3 Instruction Manual for MSEL Controller
ME0336
4 Instruction Manual for RC PC Software RCM-101-MW/RCM-101-USB
ME0155
5 Instruction Manual for Touch Panel Teaching Pendant CON-PTA/PDA/PGA
ME0295
6
Instruction Manual for Touch Panel Teaching Pendant TB-01/01D/01DR
Applicable for Position Controller
ME0324
1.1.3 How to Read the Model Nameplate
Model
Serial Number
MODEL RCP5-BA4 -WA-35P-48-1200-P3-P-B
SERIAL No.100090267 MADE IN JAPAN