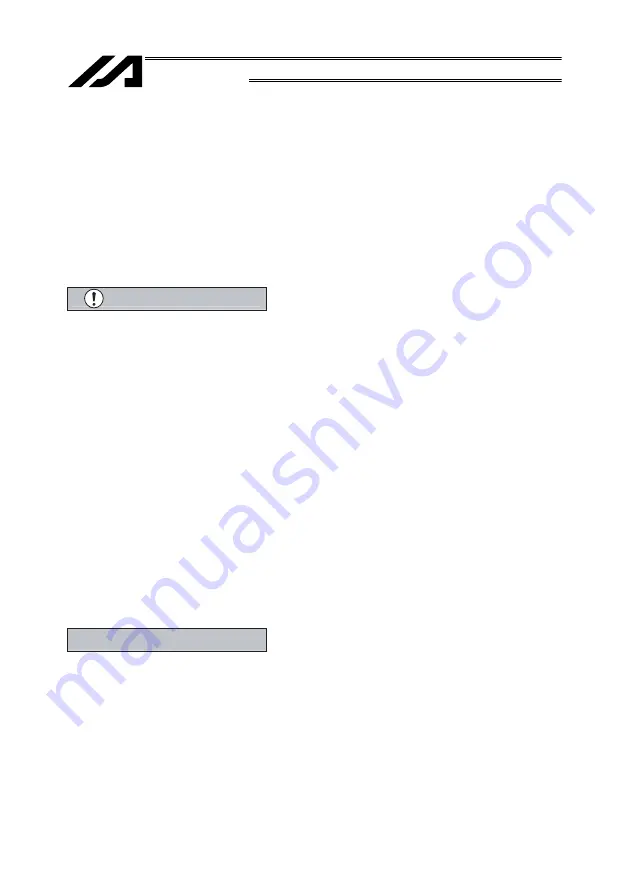
I
NTELLIGENT ACTUATOR
[Operation]
●
Turn on the power to individual equipment one by one, starting from the equipment at the highest level
in the system hierarchy. Failure to do so may cause the product to start suddenly, resulting in injury or
product damage.
●
Do not insert a finger or object in the openings in the product. It may cause fire, electric shock or injury.
●
Do not step on the product, use it as a footstool or place any object on it. It may cause scoring, dents or
deformation of the driving part, resulting in product damage, unintended stopping due to damage, or
performance drop.
[Maintenance, Inspection, Repair]
●
Wear protective goggles when applying grease to the actuator. Failure to do so may result in eye
inflammation due to spattered grease.
Note
[Installation]
●
If the product is used in a vertical setup, be sure to use the vertical specification (with brake).
●
Protection covers or other guards must be provided for the moving parts of the equipment to avoid
direct contact with the operators.
●
Do not configure a control circuit that will cause the work to drop in case of power failure. Configure a
control circuit that will prevent the table or work from dropping when the power to the machine is cut off
or an emergency stop is actuated.
●
The following conditions must be met in order to improve the straightness of the table movement and
ensure the smooth movement of the ball screw and linear guides:
[Installation, Operation, Maintenance]
●
When handling the product, wear protective gloves, protective goggles, safety shoes or other necessary
gear to ensure safety.
[Maintenance, Inspection, Repair]
●
When performing maintenance, apply the specified grease to the guides and ball screw. Pay special
attention not to let fluoride grease mix with lithium grease. The machine may be damaged due to poor
lubrication, increased resistance, etc.
[Disposal]
●
When the product becomes no longer usable or necessary, dispose of it properly as an industrial waste.
Others
■
IAI shall not be liable whatsoever for any loss or damage arising from a failure to
observe the items specified in “Safety Precautions.”
Flatness of the mounting surface must be within 0.05 mm.
The mounting surface area must be large enough to ensure the rigidity of the actuator.
1.
2.
Summary of Contents for IF
Page 1: ...IF Actuator Operating Manual Eighth Edition IAI America Inc...
Page 2: ......
Page 46: ......
Page 47: ......