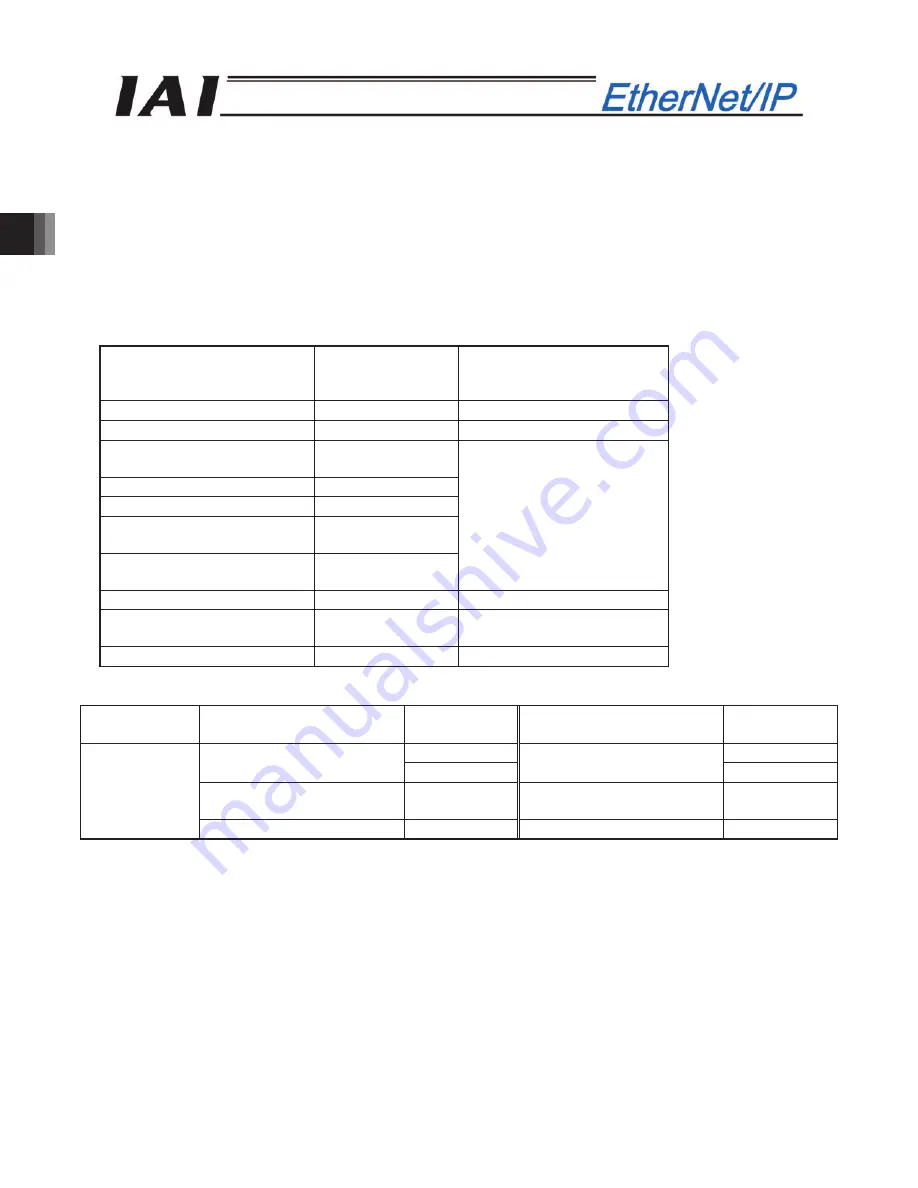
3. SCON-CA
128
3.6.7
Position/Simplified Direct Value Mode
2 (Number of Occupied Bytes: 8)
In this mode, the actuator is operated by means of force control (pressing operation based on feedback of
load cell values) and also by specifying position numbers. Whether the target position is set directly the
control signals (PMOD signals), or the value registered on the position data is used can be selected.
For the speed, acceleration/deceleration and positioning band, etc., except for the target position, the
values in the position table within the controller are used. Setup the position data referring the operation
manual for the controller main body.
The settable No. of position data items is max 768 points.
The robot cylinder's effective main functions that can be controlled using this mode, are as shown in the
following table.
ROBO cylinder function
{
: Direct control
U
: Indirect control
x: Disable
Remarks
Home-return operation
{
Positioning operation
{
Speed and acceleration /
deceleration setting
U
Pitch feed (inching)
U
Pressing operation
U
Speed change during the
movement
U
Operation at different
acceleration and deceleration
U
These items must be set in
the position data table.
Pause
{
Zone signal output
U
Zones are set using position
data or parameters.
PIO pattern selection
x
(1) PLC address configuration (* “n” indicates the node address of each axis.)
Parameter
No.84
SCON-CA input register
PLC output
address (bytes)
SCON-CA output register
PLC input
address (bytes)
n+0, n+1
n+0, n+1
Target position
n+2, n+3
Current position
n+2, n+3
Specified position number
n+4, n+5
Completed position No.
(Simple alarm code)
n+4, n+5
5
Control signal
n+6, n+7
Status signal
n+6, n+7
(Note) Be careful of using duplicated node addresses.
Summary of Contents for acon
Page 1: ...EtherNet IP IAI America Inc Operation Manual Second Edition ACON PCON SCON CA ...
Page 2: ......
Page 4: ......
Page 197: ...4 Appendix 191 PLC s IP Address Controller s IP Address ...
Page 214: ......
Page 215: ......