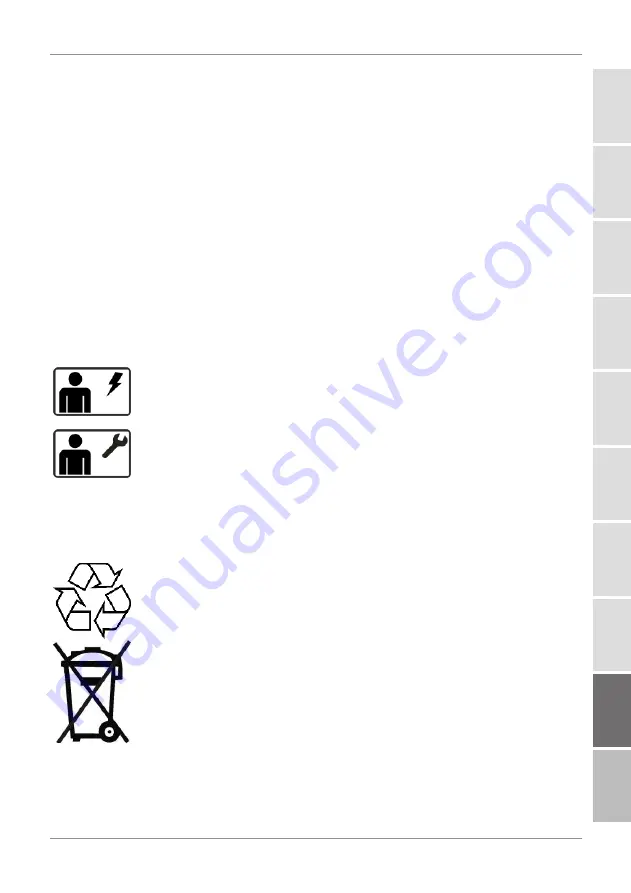
HYDAC FILTER SYSTEMS GMBH
Decommissioning / Disposal | 9
BeWa MFU-10P 4391553c en-us web
99 / 120
9 Decommissioning / Disposal
In the following chapters, you will be provided with information
regarding temporary shutdown/final decommissioning and
disposal of the product.
9.1 Temporary shutdown
If the product is being temporarily shut down, the following
measures are adequate:
1.
Switch the product off and disconnect it from all sources of
energy.
2.
Follow all the notices in the
Transport/storage chapter
9.2 Permanent shutdown
If the product is being shut down permanently, proceed as
follows:
– Empty the product fully, including all the components,
before the shutdown.
– Fully disconnect the product from the surrounding units.
– Slacken or remove the electric, pneumatic or hydraulic
connections insofar as they are present.
9.3 Disposal / Recycling
Dismount and recycle the product that cannot be used any
more, not as a whole unit, but in individual parts and according
to the kind of the materials. After dismantling and separating all
the parts by sorting them correctly, dispose of the product in an
environmentally friendly manner.
Dispose of the dismantled individual parts / drained operating
fluids / fluids in an environmentally friendly manner. Follow the
respective national regulations.
1
2
3
4
5
6
7
8
9
A
Summary of Contents for MFU-10P9S Series
Page 120: ...www hydac com ...