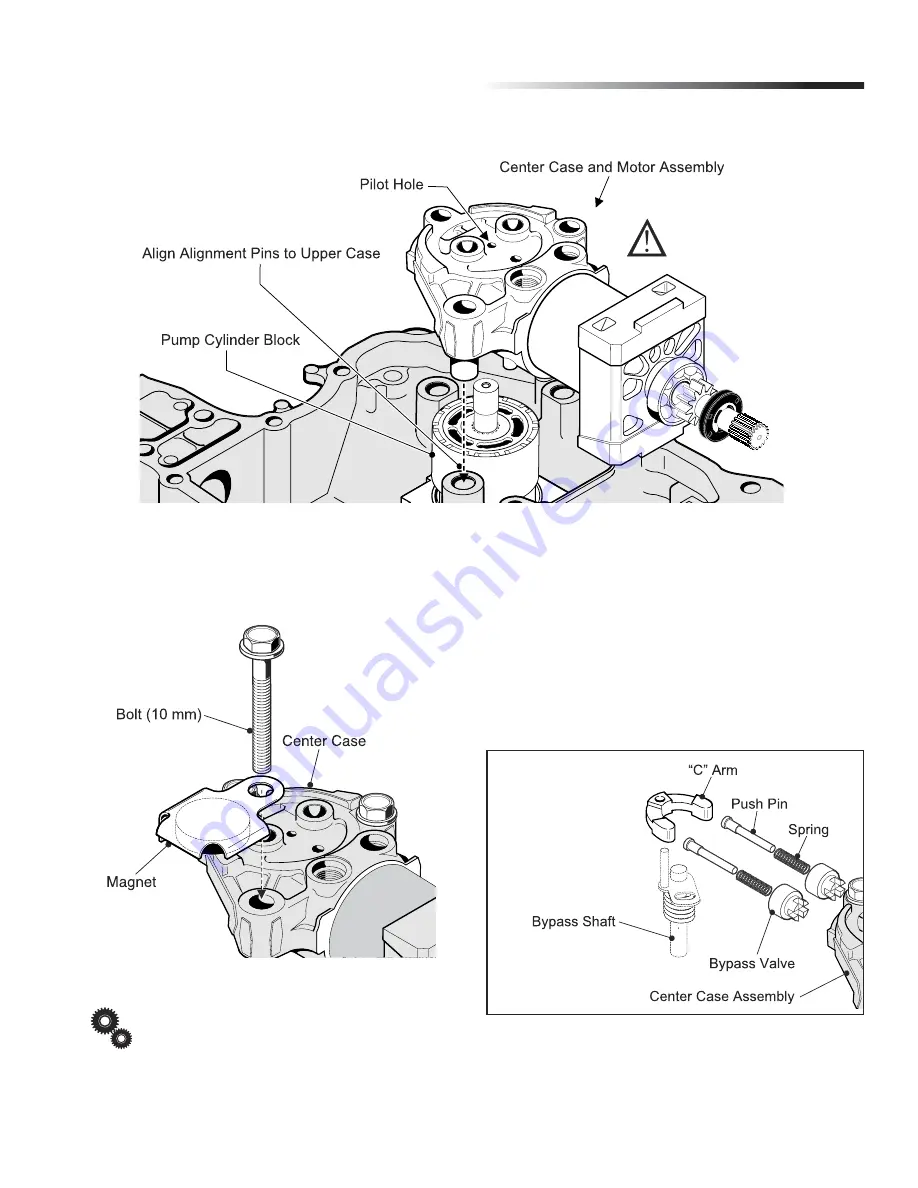
29
Tuff Torq K61 Hydrostatic Transaxle
5. Install Magnet and Bolt in third hole of Center Case.
(Fig. 36)
Fig. 36, Magnet Mounting
Magnet must be oriented, by rotating clockwise
against Center Case side, while tightening Bolts. The
Lower Case will not mate properly with Upper Case if
Magnet is not correctly located.
4. Tighten the (3) 10 mm Bolts (14 mm wrench) evenly to
draw Center Case Assembly into place.
Tightening torque
:
4.5 ~ 6.5 kg-m
44.3 ~ 63.9 N-m
33 ~ 47 ft lbs.
5. Install Push Pins, Springs, and Bypass Valves in Center
Case; then, while depressing Push Pin Assemblies, place
“C” Arm onto Bypass Shaft.
(Fig. 37)
Fig. 37, Actuating Valve Assembly
Fig. 35, Hydrostatic Pump and Motor Assembly
Motor Shaft/Center Case Assembly (continued)